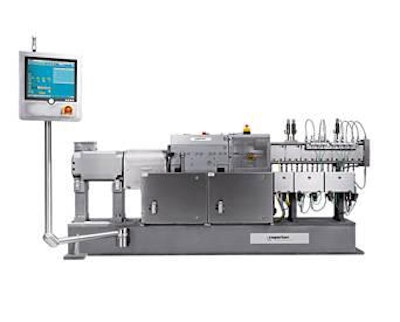
Every year brings unique challenges to the extrusion segment of the petfood industry, and 2014 has been no different. Two key factors, brought on by significant industry events, are foremost on expert minds as the year closes: petfood safety and innovation.
“As with many other types of food processing, the major areas of focus [right now] include food safety and cleanability,” say experts at Coperion K-Tron Food & Pharmaceutical Industries (Sharon Nowak, business development manager; Stefan Gebhardt, business unit manager; and Ed Beecher, process laboratory manager). “The ability to minimize any risk of contamination, as well as minimize downtime for cleaning and product changeover, by including proper design techniques in the extruder and material handling equipment can make a huge difference in the process, product safety and overall process efficiency.”
Coperion (www.coperionktron.com) is meeting the food safety challenge through ease of machinery cleaning. For example, the process sections of the Coperion ZSK extruders consist of several barrels in which the screws co-rotate. The closely intermeshing, self-wiping screws prevent stagnant zones along the whole length of the process section, for constantly high conveying and optimum self-cleaning. The recently introduced Coperion K-Tron Sanitary Filter Receiver has a top entry and custom-engineered side access filter assembly that allows for high efficiencies, with minimal degradation of the product due to decreased can velocities, and extremely high access to all internal areas of the receiver for cleaning.
Bühler Aeroglide (www.buhlergroup.com/drying) is another company with petfood safety on its radar. “The Food Safety Modernization Act is now advancing the safety of petfood and is expected to follow the food industry with the same focus on hazard analysis, preventive controls, monitoring procedures, corrective actions, verification and record-keeping,” says Bühler Aeroglide Food Safety Manager Steve Blackowiak. “Updates to rules are all trending toward a standardized, more strictly regulated environment. As food regulations get applied to petfood, the needs for processing equipment will be similar.”
Bühler Aeroglide’s food safety team has developed a new generation of dryers for the food industry, and the company expects the advances to carry over significantly to the petfood industry. “Our new hygienic generation has significantly reduced cleaning times, energy efficiency and a design that packs more production into smaller spaces,” says Blackowiak. “From a sophisticated chainless conveyor system to the simplicity of tool-less connections and hygienic door latches, the new hygienic generation can be cleaned in far less time than existing technologies.”
Wenger Mfg. (www.wenger.com) offers a temperature sensor with dual RTD input to measure actual product temperature during the production of petfoods. The temperature data from this sensor can be used to monitor and record accurate product temperature as a CCP (critical control point) for food safety programs and to automatically divert under-processed product from the extruder production flow.
Beyond the specific focus of petfood safety, the industry is, as ever, focusing on innovation to drive extrusion, drying and cooling technologies forward. One way innovation comes about is through improvements on existing technology. “Our team has worked with a variety of petfood processors to realize improvements,” says Joe Tordella, Bühler Aeroglide’s manager of field engineering. “We make adjustments in zone temperatures and modifications in product bed depths that increase production capacity. We recently helped a North American processor with modifications that resulted in a 12% savings in energy. We’ve also worked with South American processors to improve moisture uniformity, which meant more product weight could be packaged.”
Ever Extruder’s (www.everextruder.com) Clean-Cut Hub and Cutter System 2.0 is currently configured as an upgrade for existing Wenger and Extrude-Tech single screw machines, as well as specific designs for other machines. The system consists of a self-tensioning clean-cut drive hub that eliminates adjustment and alignment issues and has a rotary cutter knife blade that offers long-term, high performance cutting life and is both reversible and re-sharpenable. It installs easily with no modifications to current equipment, and it’s been designed so that any extruder operator can achieve consistent, repeatable set-ups in minutes, according to the company.
Innovation has also stepped in to solve a growing industry issue. Extru-Tech Inc. (www.extru-techinc.com) has aimed for improving extrusion flexibility, according to Corporate Sales Manager Norm Schmitt. “High fresh meat inclusion has been a significant focus in the industry over the past 12 months,” says Schmitt. “One of the objectives of Extru-Tech’s new advanced feature product line is to serve the specific needs of extruding these high fresh meat grain and grain-free based formulations. Our team based their designs around the ability of the pre-conditioner and extruder to handle fresh meat high inclusion levels, and product development tests have far exceeded market expectations.”
Wenger has also addressed the focus on high fresh meat formulas. The company’s thermal twin screw technology was developed for process applications requiring an emphasis on thermal cooking and for extruding those petfoods formulated with a high level of fresh meat, says the company. Specially configured screw elements were complimented with a unique steam injection design to increase the level of process steam incorporated into the extrudate. This process was coupled with the HIP (high intensity preconditioning) technology to give a flexible extrusion system that can handle a wide range of ingredients plus enough fresh meat to supply all the animal proteins required in premium petfoods.
Finally, there is the not-so-simple matter of efficiency. Geelen Counterflow (www.geelencounterflow.com) has introduced a new range of sanitary design dryers (VDS) and sanitary design coolers (VKS) that aim to minimize horizontal surfaces, maximize accessibility for inspection and cleaning, and avoid hollow spaces. With higher standards for weld finishing and surface treatment, risks of microbe build-up have been significantly reduced, according to the company. Large doors, hatches and retractable rotors provide access to areas that need to be inspected and cleaned frequently under strict food safety guidelines, and where wet-cleaning is prescribed, all components and surfaces can be prepared accordingly.
Amadus Kahl GmbH & Co.’s (www.akahl.de) extruder OEE 8 is equipped at the outlet with a hydraulic ram. The die can be extended into and withdrawn from the outlet case by exact control of this ram. Machine power is regulated by extension of the hydraulic ram, which can be quickly withdrawn in the event of overcurrent. The die change is carried out by means of hydraulic actuation, increasing speed and efficiency, according to the company. The knife head is provided with a separate drive and remains in its position during the die change.
What’s in store for the future of extrusion in the petfood industry? “The next year will bring growth, not only in emerging markets such as Brazil, India and China, but will also include growth in the extruded snacks and pet treats of petfood consumption,” say the experts at Coperion. “Unique shapes and compositions will require special technologies and innovations in the traditional pelletizers or cooling die designs. In addition, due to the increases in consumer demand, higher volume extruders will enable petfood manufacturers and co-packers to produce higher volumes of petfood in lower overall profile machines.”
More innovation leaning towards efficiency and petfood safety will be the key to productivity in 2015 as the industry continues to shape itself around consumer needs and regulatory mandates, and prudent extrusion experts say they plan to be at the top of their game.