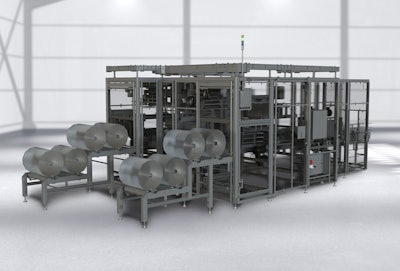
EDL Double Tight Wrap shrink wrapping machines use two perpendicular bands of LDPE film to tightly unitize and totally enclose a product or collation.
Brand Insights from EDL Packaging - A Massman Company
A leading co-manufacturer and co-packer in the pet food industry spent years manually packing bags of kibble in corrugated boxes for distribution, unaware of a better way. It wasn’t until a new customer came along and challenged the company to do things differently that it discovered EDL, a Massman Company. EDL’s solutions helped it think outside the box — literally — with the equipment, experience, service, and customizable options needed to meet the pet food company’s appetite for efficiency.
Manufacturing hundreds of formulations for numerous brands, the company makes a lot of pet food for a lot of different animals, ranging from cats and dogs to exotic zoo animals around the world. Historically, it took four to six employees per line to package the two- to seven-pound bags of kibble that were produced. The workers would place six bags in each corrugated box, send the boxes through a taping machine, and then stack them on a pallet by hand. While this system had its drawbacks, it seemed to meet the needs at the time.
Eventually, however, a new customer requested pet food bags to be bundled in shrink wrap, rather than packed in boxes. This customer was accustomed to having their product bundled with a Double Tight Wrap Machine for their kibble bags to ensure product integrity and eliminate a corrugate box. The pet food manufacturer knew it would have to adopt the Double Tight Wrap Technology in order to accommodate its customer’s changing demands.
To meet the request, the pet food manufacturer began researching available solutions to bundle products. After considering all options, it kept coming back to EDL. Not only was EDL known for being the leader in the industry for its durability and performance with its Double Tight Wrap machine, but EDL also offered time-saving accessories, vast experience, and an excellent team of people to back the product. The Double Tight Wrap machine was a perfect match for the customer’s packaging specifications.
EDL’s Double Tight Wrap machine uses two perpendicular bands of LDPE film to tightly unitize and enclose products. Low heat fuses the LDPE film to create a stable shipping unit. This type of system is especially beneficial for gable-topped bags like those used for kibble, as well as pouch products and cube-shaped products that require total enclosure.
Installation of the Double Tight Wrap machine was completed in one of the company’s two facilities, and the results were incredible. In fact, some of the advantages exceeded expectations. For instance, less floor space was needed to store the roll wrap than corrugated boxes. Instead of needing hundreds of racking spaces for the boxes, rolls could be stored in a much smaller footprint. Pallets of bundled products could also be stacked up to five pallets high, resulting in even more space savings.
Other benefits were more obvious, such as the cost savings, since the roll wrap was much cheaper than boxes. Drastic improvements in efficiency were made, too. With the Double Tight Wrap machine only one or two employees were needed to monitor the process, compared with the four to six required to manually pack the bags of kibble. Additionally, the machine’s ability to bundle enough product to fill a pallet in six to eight minutes far exceeded the speed of the manual process, which took about 20 minutes to fill a pallet.
The automation provided better consistency, too. Machines removed the human error in counting and manually placing products in cases.
The elimination of manual packaging also has great benefits for safety and employee wellness. By automating the process concerns of repetitive motion injuries, as well as numerous paper cuts from handling corrugated boxes, have been alleviated. “A four-pound bag of kibble doesn’t seem like much, but it can add up to thousands of pounds over an eight-hour shift,” said the company’s Senior Process Engineer. “Doing one motion all day will make the other muscles not work correctly, and now we’ve gotten rid of that.”
It was also discovered that the bundled packages experience less damage in shipping. Corrugated boxes have sharp corners that can catch when loading trucks, and they occasionally collapse when stacked, resulting in damaged product. Oftentimes, one pallet per load of 30 to 40 pallets would experience some type of damage due to bouncing and crushing. The bundled packages, on the other hand, proved to be sturdier and stack better, so they don’t shift during transport.
After experiencing the advantages of the Double Tight Wrap machine, the pet food manufacturer began to think that if one machine could make such a difference, what would another do for them? This thought led to the installation of a second Double Tight Wrap machine from EDL at the company’s other facility in October 2024.
Until this point, when the company only had one Double Tight Wrap machine, the majority of its products were still packed in corrugated boxes. But with the second machine a game-changing decision was made to transition almost every customer to bundles.
Getting customers on board with the bundled packages was easy, since the cost savings of the process were passed onto them. “The biggest selling point to customers was actually the reduced damage,” said the Director of Operations. “It’s an interesting concept that the pet food bags are technically exposed more in the bundles, yet less product is damaged this way.”
After getting the second Double Tight Wrap unit online, the crew became EDL fans for life. The company has stayed in close contact with EDL since the purchases and has ended up retrofitting the Double Tight Wrap machines with some exciting upgrades.
The upgrades include a Gable Tucker, which is a bar that holds down the gable flaps on the pet food bags during the wrapping process, preventing the flaps from contacting the seal bars. The Gable Tucker is especially helpful when dealing with high-density foods that have low bag fill heights.
Next, an auto changeover feature will be installed soon to maximize efficiency when switching formulations. This will save a considerable amount of time, as the company averages one or two product changeovers in a 24-hour period.
An auto splicer will also be added. This feature saves time and labor by automatically splicing two rolls of LDPE film together when one runs out. Without the auto splicer employees have to shut down production and manually tape two films together when starting a new roll. Calculations show the return on investment of this add-on could be as soon as four-and-a-half months.
In hindsight, the company wishes they would have invested in the Double Tight Wrap accessories earlier, rather than retrofitting them, which cost extra time and money in the long run. “We didn’t feel we needed the extras when we were quoting the machine,” said the Senior Process Engineer. “I kick myself every day for not including them right away. I recommend them strongly.”
Furthermore, a high-speed bagger was purchased to help increase output capacity. “Our baggers work slower than the rate we can bundle products,” said the Director of Operations. “In fact, the speed of the Double Tight Wrap machine is ample enough that it will never be a constraint to our operation.”
EDL’s service has contributed to the successful implementation of the Double Tight Wrap machines. “We had one of the controls go down at 2 a.m., and I sent EDL’s service manager a text message at that time, hoping he would see it first thing in the morning,” said the Senior Process Engineer. “He actually texted me back a minute later to diagnose the issue, and he sent out a new part right away.” Overall, service issues have mostly been nonexistent, but it’s comforting to know that if there is a problem, the response will be swift.
The transition to the Double Tight Wrap machine has led to numerous benefits through lower costs, less product damage, reduced labor requirements, higher output, and better use of space. In the end, the investment to suit one customer’s needs turned into a solution to improve packaging for many different brands. And by doubling down with a second machine, this manufacturer is well positioned to meet the needs of the pet food industry and satisfy its growing demand.