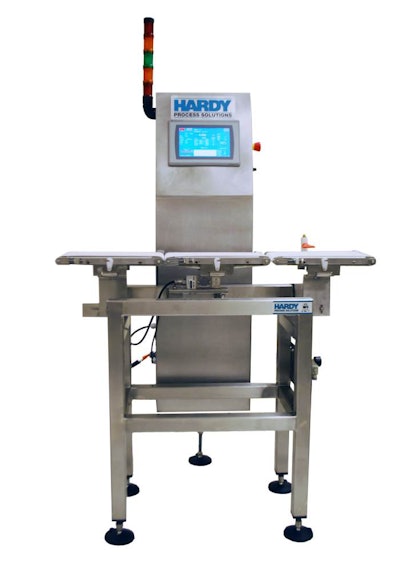
Hardy Process Solutions’ Dynamic Checkweighers were able to diagnose and reduce overfill rates through process optimization with filling machines. With integration into the factory control system via Rockwell Automation’s FactoryTalk, the Hardy Dynamic Checkweigher is saving the manufacturer overfill expenses of approximately US$35K annually.
Machine control, statistics and analytics are managed with an integrated Rockwell Automation CompactLogix PLC while the high performance Hardy HI 4050CW check weigher controller contributes as a co-processer, generating fast, stable and accurate weight data. The resulting high speed check weighing system can process up to 350 pieces per minute and generate a myriad of process data that is easily shared with any other device on The Connected Enterprise Network.
Using Wide Area Networking (WAN) connectivity, the customer was able to:
- Monitor real-time production trends and process performance
- Set alarms around real time trend data
- Share and distribute TAGS with upstream control systems
- Track and Monitor local changes made on the equipment
- Push down product recipes and operating parameters from a centralized control center
Hardy provided these capabilities to the customer with standard integrated software. The Hardy Dynamic Checkweigher series is a fully automated system designed to automatically weigh items while in-motion. The Checkweigher controller can
communicate both upstream and downstream across Rockwell Automation’s The Connected Enterprise.
Flexible and accurate, the Hardy Dynamic Checkweigher weighs products of virtually any shape or size in containers such as boxes, cans, bottles, rigid shrink-wrapped packages or flexible packages. Items compatible with the system include bagged and boxed sugars, raw meats, fruits, vegetables, chemicals, fertilizers and consumer packaged goods.