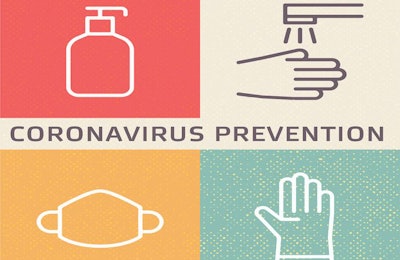
In life we encounter many crises, both natural and man-made — flooding, earthquake, food safety recalls or the current prime example, a virus-linked pandemic such as COVID-19. But all crises share a common thread: To effectively deal with the crisis and successfully emerge in its aftermath, we require strong leadership. Without this we risk wasting precious resources, we might not successfully deal with the effects and risk recurrence of the crisis, people will continue to suffer and might lose trust in our organization or business, and ultimately all our efforts might end in failure (death of our business or organization).
During a crisis, there is most likely to be a sense that many if not all is in chaos. In terms of your own organization, employees will look for a strong leader who can bring about calm, focus and clear communication in a timely manner. These attributes will build trust amongst consumers (pet owners) and employees that everything is under control and that the business can continue to supply safe pet food of the quality expected by customers.
Even with high levels of automation, pet food manufacturing requires the involvement of people. A key point in producing safe pet food of the expected quality is the culture we develop in our organization; for example food safety culture (food safety behavior) and occupational health and safety (behavior that affects the safety of how we work). Behavior is most effective when adequate resources are provided and there is strong leadership that supports a positive culture in the business.
During the current COVID-19 crisis, there is a likelihood that we will feel more under pressure, more stressed and more anxious at work. To help reduce these natural, human feelings, employees will also look to our business leaders to ensure that their health (mental and physical) and safety are being supported by leadership, procedures and resources when they are at work.
So, what does that mean in real life?
Firstly, it is important that the business “way of working” during the COVID-19 crisis is clearly and timely communicated to all employees and external stakeholders (suppliers and retailers). This should state procedures that are in place; e.g., at-home working and obligations (what we expect from our own employees and the supply chain).
Ideally for employee safety and where possible, employees who can work from home should be allowed to do so. This might include support functions like sales, marketing, purchasing and HR. But clearly this is not possible for workers directly linked to the production process, and other steps need to be taken to support their health and safety. In general terms, the areas that must be considered include:
- Access to the company/factory
- Employee hygiene and safety
- Plant hygiene and safety (premises and equipment)
- Loading and unloading of goods
- Interpersonal distancing
Access to the company/factory: Access should be prohibited to anyone with a temperature above 99.5 °F (37.5 °C) or having any other symptoms of novel coronavirus infection. Special access procedures should also be implemented for contractors/external suppliers like hygiene, pest control and sanitation contractors.
Employee hygiene and safety: It is important to reinforce personal hygiene procedures and to ensure you demonstrate these as managers. Hand cleaning should apply even when wearing gloves, even if these are changed frequently. This rule should be reinforced in the following situations: after having coughed or sneezed; after handling dirty equipment; and after any other activity where there is the possibility of COVID-19 contamination. All gloves, including those used for waste management, must be disposed of safely in appropriate, labeled waste containers.
Hand cleaning products and sanitizers should be in adequate supply next to dedicated hand-washing facilities. These facilities should also be provided with hot-air hand dryers or adequate supplies of disposable paper towels (with appropriate disposal bins). Other personal hygiene best practices include washing forearms (in addition to hands) and wearing disposable protective gowns/coats/boiler suits and disposing of these very frequently, into dedicated, labeled waste bins.
The use of personal protective equipment to protect the mouth, nose and eyes should be carried out as recommended by World Health Organization (WHO) guidelines.
Plant hygiene and safety (premises and equipment): The factory facilities (including rest rooms, canteen and meeting rooms) must be cleaned at every shift change according to agreed disinfection and sanitization procedures provided.
Humidity can promote survival of the novel coronavirus on inert surfaces; it is therefore best practice that appropriate locations have good ventilation and a higher cleaning schedule frequency. Where used, air filters should be sanitized or replaced more frequently according to supplier guidelines.
Loading and unloading of goods: According to guidance laid down by the authorities in different countries, the following (from the Italian Ministry of Transport and Infrastructure) are considered to be examples of “best practices”:
- Ideally, drivers should wear gloves or masks or remain in their vehicle.
- Drivers can access the unloading /loading area, even if no protective equipment is worn, but they must not leave their vehicle and must not be closer than 3 feet (1 meter) from other employees.
- There should be no direct contact with employees during loading/unloading, including exchange of documents, and the driver/employees must maintain a distance of at least 3 feet (1 meter).
- There should be no access to company premises except for toilets. These toilets must have adequate hand-washing facilities (as described above) and be included in the hygiene/sanitation program.
- Parcels, documents and other types of express goods are permitted, but there should be no direct contact with the recipient/courier.
- Where it is necessary to work less than 3 feet (1 meter) away from another person and no protective screens are provided, masks must be used both indoors and outdoors.
Interpersonal distancing: Where possible, meetings, gatherings and interpersonal contacts should be avoided. This includes new ways of working, such as: staggered entry and exit times and rescheduling factory shifts/hours of working.
Fixed, working teams should be used to limit the possible infection of workers from other teams.
How to apply what we’ve learned during the COVID-19 crisis
Taking a step back from the reason for implementing the types of changes outlined above, it should be noted that many of these measures are of benefit in any pet food manufacturing/ingredients business.
While we hope that we are not forced into adopting these restrictions again for many years, many of the measures outlined above are beneficial in developing your approach to both biosecurity and food defense. Examples include tighter control of access to the factory and improvements to personal hygiene facilities/practices. These help minimize the risk of both intentional and unintentional contamination of your products.
More on COVID-19
View our continuing coverage of the coronavirus/COVID-19 pandemic.