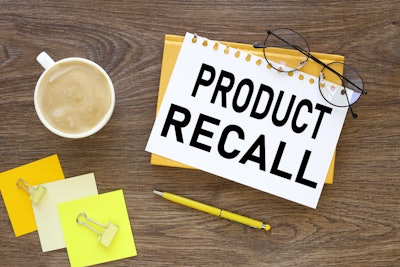
Companies in the pet food supply chain have three important steps to take in order to be ready for a recall, according to Laurie Henry, partner at Chicago law firm Shook, Hardy and Bacon.
Henry spoke May 2 during 2023 Petfood Forum in Kansas City, Missouri, USA.
The three steps are to identify a problem, notify relevant people about the problem and fix the problem.
“With a recall, the devil is in the details because, while it’s true that each recall involves these three steps, behind them are many questions and many action items,” Henry said. “Recalls bring stress and uncertainty to the business, it’s a huge time demand managing a recall, getting through a recall, and then at the same time that you’re doing that, you’re still having to keep the business going forward on a day-to-day basis.”
3 steps in more detail
Henry explained the details behind each of the three steps.
1. Identify the problem by pinpointing what the problem is and who in the supply chain is affected.
Recalls are for problems, Henry said. By the U.S. Food and Drug Administration’s (FDA) definition, a recall is “a firm’s removal or correction of a marketed product that the Food and Drug Administration considers to be in violation of the laws it administers and against which the agency would initiate legal action, e.g., seizure. Recall does not include a market withdrawal or a stock recovery.”
This means a recall should take place if a product violates FDA regulations, and FDA would do something about the problem. Examples include fungal contamination or the incorrect amount of a certain ingredient or nutrient.
Henry said it is important to know your products to be aware of the likely ways that your product could run into a problem, and to know the potential safety risks for that problem.
“If you’re a pet food manufacturer, you’ve likely already done that work. It’s the hazard analysis in your food safety plan,” she said.
It is also important to know which products are affected by identifying and understanding what information your system tracks, including receiving, manufacturing and shipping.
“What you’re going to have to do is go through a traceability exercise,” Henry said. “So what we’re talking about is, how can you identify the problem … based on what you know about receiving, manufacturing and shipping. So you have to be ready for it here on the front end before you ever find yourself in this situation. How do you make sure all your records line up to know what goes into each product and each one of these points and out the doors?
“There’s not a right or wrong way to do it. You just have to make sure that that traceability all fits together from the very start to the very end, such that if you’re in a recall you know which products to try to go after,” she said.
2. Notify people about the problem, including customers, suppliers and FDA. In your recall plan, you should specify who needs to be notified of a recall and how they should be notified.
“If you’re ever in a recall situation, you have lots of fires to put out, so just go ahead and take that issue off the table” ahead of time, Henry said.
Similarly, if your supplier has a recall, they should know how to contact and support your company.
“That can mitigate risk and ease up the burden on your side if you are doing that as well with your suppliers,” she said.
While FDA doesn’t technically need to be notified of a recall, the agency and your customers will expect you to do so. Be aware of who your FDA recall coordinator is and what they will ask for, such as certain documents.
“Your recall coordinator may not have the technical expertise to walk you through some of the wrinkles of a recall, but they’ve seen a lot. They’ve been through a lot of recalls, and they are well versed in compliance. So, work with that person,” Henry said.
3. Fix the problem: After there has been a recall, FDA will want to know what will be done in the future to prevent it from happening again. It will also want to see a corrective action and a preventive action (CAPA). Your company’s food safety plan and supplier approval should be re-evaluated to prevent a recall from happening again.
Additionally, Henry said, “FDA wants to make sure that the non-compliant product is off the shelves. They want to make sure they know what you do with it,” when it comes to properly dumping or destroying the recalled product.
After a recall
Once a recall has occurred, how do you know when it’s over?
“It’s over when you’ve exhausted all reasonable efforts to get the problem product back that you think you’re going to get back. The regulations are intentionally vague about when you get to that point,” Henry said. “Spoiler alert: When the recall’s over, you may not be done, or rather FDA may not be done with you. A recall can trigger a facility inspection. It’s not uncommon that after, or even during, the recall that FDA wants to see a plant’s conditions.”
FDA may also request a regulatory meeting to talk about preventive actions, and it may issue a warning letter.