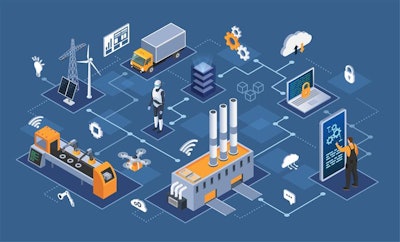
The pet food industry is experiencing a fundamental shift toward automation as manufacturers seek to improve product quality, reduce labor dependency, and meet increasingly stringent regulatory requirements. That is according to Caleb Townsend, vice president of sales with APEC, who said during a recent Ask the Petfood Pro that automation solutions are becoming essential for competitive survival in today's market.
"If you're not automating now, you have to get on the bus," said Townsend. "Things are moving at a much faster pace than they have in the past, and if you don't keep up with the innovation there, you're going to fall back and not be able to keep up, not be competitive."
Key automation applications transforming production
Pet food manufacturers are implementing automation across multiple production stages, with particularly significant impact in batching, blending and mixing operations, said Townsend. The most effective solutions include automated batching systems that ensure precise ingredient measurements and consistency while reducing waste and improving efficiency.
Recipe management software has emerged as another critical component, helping manufacturers maintain product consistency by managing ingredient set points and handling both batching and continuous processes. These systems work in conjunction with automated tracking systems that monitor ingredients from entry to finished product, ensuring quality control and regulatory compliance.
"Traceability and lot tracking, especially on the pet food side, automated tracking systems help monitor ingredients from entry to the finished product, ensuring quality control and regulatory compliance," Townsend explained.
Reducing downtime through smart coordination
Automated ingredient handling systems significantly reduce downtime during batch transitions through precise scheduling and coordination, said Townsend. These systems synchronize ingredient deliveries to create smooth transitions without bottlenecks, while pre-loading and staging capabilities allow ingredients to be pre-measured ahead of time for rapid switchover without delays.
Clean-in-place systems further minimize downtime by automating sanitation requirements between batches. Smart automation ensures seamless recipe transitions by adjusting parameters dynamically, eliminating human error and preventing disruptions before they escalate, added Townsend.
Quality control advances with inline testing
Modern automation incorporates sophisticated quality testing capabilities directly into the production process. Near-infrared (NIR) spectrometers enable real-time tracking of protein, moisture and other key parameters without destructive analysis.
"You can really track all your protein, moisture, all the key types," Townsend noted. "Especially if you use those inline, you can track as you go, adjusting on the fly -- the automation system will adjust as needed."
Additional quality control innovations include AI-powered vision systems for real-time defect detection, analyzing products for surface imperfections, misalignments, and contamination before packaging. Advanced lighting techniques enhance visibility, allowing sensors to detect subtle color variations to ensure consistency from one pellet to the next.
Energy efficiency improvements
Townsend noted that automation significantly enhances energy efficiency across heating, cooling and extrusion processes. Smart temperature regulation using automated sensors controls and adjusts heating and cooling dynamically, minimizing energy loss. Modern AC vector drive systems for extruders reduce mechanical inefficiencies and cut energy consumption substantially.
Advanced heat recovery systems capture and reuse excess heat from extrusion or boiler systems to lower overall energy demand. Automated cooling systems prevent overuse of water and energy by maintaining precise temperature control, while non-intrusive energy monitoring provides real-time tracking without disrupting production.
Addressing labor challenges and safety concerns
The automation trend has accelerated partly due to persistent labor shortages in the pet food industry, said Townsend. Automated systems can dramatically reduce workforce requirements while improving safety conditions.
"You can go from eight to 10 people on a shift down to a couple in that specific location," Townsend said, describing the impact of automated micro ingredient batching systems.
Beyond reducing headcount needs, automation addresses significant safety concerns. Automated material handling reduces exposure to potentially harmful ingredients and eliminates repetitive strain injuries associated with manual lifting and twisting.
Regulatory compliance support
Automation systems help manufacturers comply with both food safety and occupational safety regulations, said Townsend. End-to-end traceability technologies like RFID, machine vision and barcode scanning ensure real-time tracking of ingredients from receipt to finished product, meeting FSMA traceability requirements.
Laboratory information management systems (LIMS) capture and store critical compliance data, allowing manufacturers to provide documentation to authorities when needed. Automated label inspection systems detect missing lot codes, incorrect expiration dates, and mislabeling issues, reducing compliance risks.
For OSHA compliance, automated systems incorporate machine guarding and lockout/tagout procedures, with light curtains and safety systems that can trigger shutdowns when unsafe conditions are detected.
Implementation strategies for manufacturers
For companies beginning their automation journey, Townsend recommended starting with recipe automation as a foundation. "I think that's a good start, because once you get that into place, then you have that base," he said. "Now you can pass that on. That recipe is built into your system, and then when you're running a product, now let's add on batching and dosing."
The next logical step involves adding batching systems that receive recipes from the management system and handle weighing and dosing of micro ingredients or mid-size bulk bag ingredients. Companies can then progress to more expensive solutions like robotics and palletizing systems.
Market adoption and future outlook
Despite the clear benefits, automation adoption varies significantly across the industry. Townsend estimated that probably under 75% of manufacturers are currently automated, with higher percentages among larger companies but surprising numbers of plants still relying on manual hand dosing.
The COVID-19 pandemic accelerated adoption as labor became difficult to secure. "There was a big push during the pandemic years, and it's continued, maybe not as drastic as it was in those first few years, but it's still pretty steady," Townsend observed.
Looking ahead, artificial intelligence is expected to play an increasingly important role in automation systems. AI applications are emerging in equipment diagnostics, data analysis and predictive maintenance, with the potential to analyze sensor data and provide advance warning of equipment issues before they cause downtime.
The industry appears to be close to significant AI integration, said Townsend. "We're on the cusp of something there," he predicted. "I think we're going to see a lot of changes in the next two to five years.".
As premium and specialized pet food demand continues growing, automation becomes increasingly critical for manufacturers scaling up production while maintaining quality and traceability standards. Automated technology offers clear paths to improved efficiency, safety and competitiveness in an evolving market landscape.
Ask the Petfood Pro: Next up
The Power of Mentorship -- How Mentorship Has Shaped My Career
Friday, June 27 | 12 p.m. CT
➡️ FREE registration: https://lnkd.in/eyDFW73k
Join us for an engaging expert panel discussion where Women in Petfood Leadership (WiPL) distinguished leaders share personal stories about the pivotal role mentorship has played in shaping their careers. Discover memorable mentorship moments and valuable insights that inspired and guided them through their professional journeys.
Featuring:
Gail Kuhlman, retired technical fellow, Companion Animal Nutrition at Mars Petcare
Betty McPhee, sales manager, Heartland Supply CO
Laura Moran, founder & CEO, LPM Innovate
To see other recent Ask the Petfood Pros or sign up for future sessions, visit Petfood Forum's website.