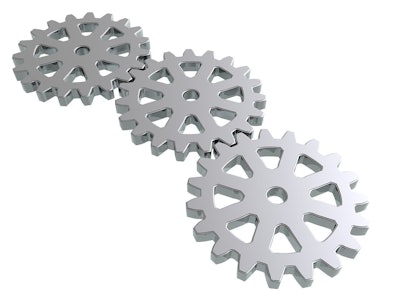
Efficiency is a pillar of manufacturing success. The saying “time is money” exists for a reason; factors such as production downtime, labor issues and other operational challenges can all conspire to decrease efficiency, leading to waste, profit loss and consumer dissatisfaction.
“There are so many things for pet food manufacturers to consider when it comes to efficiency,” said Jessica Stank, marketing manager and East coast sales for processing solutions provider Automated Process Equipment Corporation (APEC). “Pet owners have expectations of quality when it comes to the feed they choose for their pets. The key to providing a consistent product is through an efficient manufacturing process. The bottom line is always high on the list of concerns for a manufacturer, so having efficient processes, efficient manufacturing equipment and control systems are paramount. Maximizing throughput and production rate capacities with room for growth are always important considerations.”
Finding time: Smoothing out and speeding up the manufacturing process
One of the most high-level views of efficiency has to do with the overall manufacturing process. Anything with multiple steps to completion means multiple opportunities for products — and people — to bottleneck.
“Time and labor are two big factors — when you can free up both, that’s really valuable,” said Lloyd Campbell, director of wholesale for wholesale distribution company AFCO Distribution. “Embracing improved warehouse processes, supported with the right warehouse management system (WMS), rules and roles ensure the work gets done right the first time, because workers are directed to do tasks specific to their job. Warehouse employee performance metrics provide access to real-time data to benchmark productivity, suggest improvements and build employee morale.”
The good news labor-wise is that nondurable goods manufacturing has largely recovered its labor force since the COVID-19 pandemic. As of May 1, 2025, according to data collected by the U.S. Chamber of Commerce, there were roughly 4.86 million people employed in the space, with only 191,000 unemployed. Unemployment in the segment is down 24.8% from pre-pandemic levels. The bad news, of course, is that those numbers do not evenly distribute among the areas that need those types of workers — just because there are people employed doesn’t mean they’re all employed where the highest need is. And those 191,000 qualified and looking for jobs in manufacturing can’t fill spots that aren’t where potential employees happen to be located.
Equipment efficiencies and automation solutions
This uneven distribution of labor is why the equipment itself is being asked to do more for longer, and why automation is such a hot topic in the pet food space.
“In terms of operations, maintaining a high operating efficiency (downtime vs. production time) is critical in staying competitive,” said Will Henry, R&D director for extrusion system experts Extru-Tech Inc. “The more production time that we can help our clients squeeze into a week will return significant improvements on their cost of production. Raw material and labor costs are significant drivers to improve uptime.”
One of the unique challenges of pet food manufacturers is the breadth of pet food types. A manufacturer might be producing more than one type of pet food, even if they largely focus on kibble. Ingredients, particularly proteins, can vary widely in production needs, meaning increased potential for downtime.
“Equipment needs to be efficient so a pet food manufacturer doesn’t waste time and money with maintenance downtime,” said Steffen Knoedler, global food and beverage business development manager at pump systems provider Watson-Marlow Fluid Technology Solutions. “For example, as some companies have reduced their maintenance teams which would take care of the pump, it is better to have a pump that is low maintenance and easy to operate. If the pump goes down regularly, the entire system goes down and manufacturing stops. This is a very expensive scenario for the pet food manufacturer.
"The range of pet food products is also getting wider and wider," Knoedler continues. If you go into a pet food shop, there are so many different types of foods available and they are mostly being produced by the same line, so the pump must be able to have a quick turnover. The pump needs to be able to transfer different types of ingredients, with different viscosities. Pet food is different for big dogs compared to puppies for example, but those two types of food are usually done on the same line, and the manufacturer needs the same level of efficiency and consistency of product. The equipment they use therefore needs to be very flexible, in terms of applications.”
Equipment efficiencies are also where automation can step in, helping to ensure a consistent, high-quality product all the time.
“The biggest challenges we have seen in pet food manufacturing are the manual processes,” said Stank. “Hand-add batching is a good example of a manual process that hinders efficiency. We help our customers address this issue by providing an automated solution for weighing and batching that eliminates the manual scoop-and-scale method. That manual method is time consuming, labor intensive and it leads to waste from spills and human error. It causes inefficiencies with ingredient variances in the batches, which in turn leads to inconsistent final product.
“Another area we have helped customers improve efficiency is with our liquid application equipment,” added Stank. “There are different types of kibble coating technology out there, but the efficiency varies from one to another. Liquid coating should offer an even coating on all the kibble. This way, customers can use the least amount of liquid needed to achieve the desired result.”
The future of efficiency in pet food
There’s no doubt that efficiency in all aspects of pet food production will continue to be a focus for manufacturers.
“In the immediate future, I think we’ll see more and more automated storage and retrieval systems (AS/RS) in larger warehouses and distribution centers,” said Campbell. “Goods-to-person picking is an effective way to bring the inventory to the picker while minimizing the need for expensive warehouse expansions and maximizing the space you already have.”
Innovation will play a big role in ensuring efficiency challenges are solved as they come up.
“I believe we will continue to be pushed by both the consumers and our competitors to maintain a vigilant drive toward always improving their efficiency,” said Henry. “From an equipment standpoint, we will continue to review and investigate raw materials and manufacturing. A prominent focus has been integrating AI technologies both with our equipment and the entire production facility. Our initial results with a few prototype installations have been very promising.”