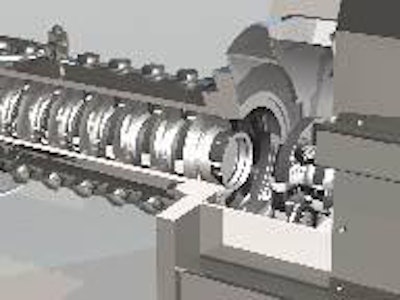
Improving plant performance and upgrading production are constant concerns of everyone in our industry from the highest executive to the people on the production lines. Focusing on processing developments is often the key to a successful investment that leads to a good return and a higher standard of quality in the end product. New extrusion products and processing technologies are the fastest ways to reach these goals.
Control product characteristics with die design
Innovations in die design including hydraulically adjustable dies and die-interchange systems provide faster and simpler changes from one die to another during the extrusion process. These improvements to die design have also led to greater flexibility and control over product density and shape.
Extru-Tech Inc. offers the Multi-Color/Multi-Shape Die System, an example of a die-interchange system designed for single screw cooking extruders. The die assembly design allows the production of multiple colors and multiple shapes of finished product simultaneously and is revolutionary in the industry, according to the company. The system eliminates the need for post-run mixing and blending of product without reducing production capacity, thereby reducing costs and improving profit. It is available in a variety of configurations - two, three and four color - to allow for tailoring the number of product colors and product shapes in a single production run application.
Amandus Kahl has recently introduced the Kahl Extruder, which is different from common, older model extruders because the die plate is fitted on a hydraulic piston. The die can be removed from the extruder outlet during operation. The handling of the machine is much less complicated compared to a normal extruder with a static die because of the easy start-up and quick pressure relief in case of blockages. The extruder can also be supplied with steam jacketed barrel housing and friction discs.
Use hardware to improve process stability
Wenger has new technology for single or twin screw extruders with rotating elements designed to impact more shear and mixing compared to mixing lobes. Homogenizing screw elements improves mixing and is very effective for use in high meat recipes and those high in internal fat.
An adjustable back pressure valve (BPV) has several new features including a third position for relief of die pressure, as well as a reject position and process position. The stem now accepts inserts with round openings and an electric drive is available on the BPV to replace hydraulic drives. The BPV varies extrusion restriction independent of the die, diverts product from the die/knife area during startup or maintenance and allows for adjustments to be made on-line while the system is in operation. The main benefits of BPV are:
- Diverting off-spec product for improved sanitation and quality control;
- The ability to service die/knife/conveyor without stopping the extruder process;
- On-line adjustment of specific mechanical energy to control product properties;
- Improving process stability; and
- Eliminating extruder configuration changes.
Also new from Wenger is the Quick-change Breaker Plate, a plate with holes that is inserted between screw and die. The filter helps with uniformity of product, collects foreign material, controls back-pressure and is changeable during operation. The Breaker Plate can operate at up to 10,000 PSI.
Extended Wear knife blades from Wenger wear as much as 11 times longer than originals and decrease wear cost by as much as 53%. The knives also significantly reduce the amount of time necessary to set the blades and minimize the product quality cycles usually associated with worn blades.
Reduce wear with metallurgy
Clextral has addressed the extruder wear issues of processors by conducting research in high density metallurgical solutions for twin screw extruders. This led to the development of premium metallurgy that increases the operating life of extruder screws and barrels four to five times when compared to standard metallurgy, according to Clextral. From a processor's standpoint, this development offers multiple advantages: reduced downtime for component replacement; fewer dollars spent on replacement screws, barrels and barrel liners; and long-term consistency in product quality. Metallurgy is used for tips of flights on screws or 100% monoblock construction as well as on monoblock barrels and barrel liners.
Clextral employs HIP (hot isostatic pressure) and HIC (hot isostatic compression) procedures that allow multi-materials to be manufactured in a homogeneous method using varied compositions. This new metallurgy significantly outperforms standard materials due to its high densification, the company says. This is a response to thermal, chemical and mechanical stresses that are the typical causes of screw and barrel damage in the high work zones of twin screw extruders.
Powder metallurgy is a method that allows for an effective marriage of strength and hardness. Numerous distinctions are possible in the form of powders, and several processes are capable of simultaneously making them denser to obtain a screw or barrel blank with a high quality interface. High density compression along with a sintering operation to obtain the metallurgy, a new laser fusion technique and the HIP process makes the two powder layers denser and allows sintering.
This process consists of:
- Packaging powders and eventual nodes in capsules;
- Turning the capsule into a vacuum;
- A simultaneous compression and sintering stage using a pressure oven and a maximum temperature of 2,000°C;
- A blank extraction by machining the capsule and eventual nodes.
According to Clextral research, reducing wear and surface degradation often associated with an unchecked loss of material is key to reducing energy losses. Replacing mechanical parts means new manufactured parts and maintenance, creating additional energy consumption and financial losses. Increasing reliability and the operating life of mechanisms limits replacements and guarantees system safety.