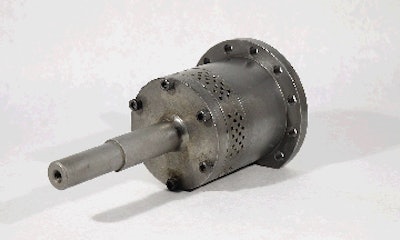
Recent extrusion hardware advances have enabled precise control of product characteristics, reports Sajid Alavi, PhD, Kansas State University (KSU), USA. Advances that have made this control possible include:
Innovative screw designs;
Post-extrusion pressure control;
Die-interchange systems.
An example of new extruder design is the conical twin screw extruder from Wenger Manufacturing (US). It provides better compression of the extrusion melt, enabling varying mechanical energy inputs and final product densities without use of special screw elements.
The post-extrusion pressure chamber is another improvement that has led to the ability to control product expansion and density by controlling the pressure after the die. Innovations in die design including hydraulically adjustable dies and die-interchange systems (Amandus Kahl, Germany) provide fast and simple changes from one die to another during a process. These die design advances have also led to greater flexibility and control over product density and shape.
The growth of the high-quality, premium petfood segment is especially high. Hence, Alavi predicts industry and academic research will focus increasingly on utilizing the rapid advances in data processing and sensor technologies. This research will lead to better online process and product control. Online sensors based on methods such as electrical capacitance and resistance and near infrared (NIR) spectroscopy will increasingly be a feature in extrusion systems. This will enable real-time monitoring of moisture at various points and other critical parameters such as residence time in the extruder barrel and thermal and mechanical energy input.
Alavi manages the extrusion center at KSU, which provides extrusion training and services for pilot-scale trial runs. For additional information, visit www.oznet.ksu.edu/grsi/extrusion.htm.
A fast track for new products
Laurent Garcia, Clextral Inc., observes that bringing new products to market is the name of the game in petfood today. In 2005, petfood marketers launched the biggest surge of new products in the history of the market, according to Packaged Facts market research. A large proportion of these new products are high-quality products with upscale appeal.
Garcia asserts that turnkey twin screw extrusion production lines processing many types of high-quality petfoods offer simple changeovers and ensure a quick return on investment. The Clextral Economic Line processing line manufactures dry foods (approximately 8% moisture), semi-moist foods with essential oils and meat ingredients (15-30% moisture) and treats with high protein and increased flavor components (approximately 18% moisture), interchangeably.
The Economic Line utilizes Clextral's Evolum twin screw extruder, which manufactures premium products due to its design ensuring homogenous mixing and optimal starch gelatinization. The Evolum's faster screw speeds and torque maintain greater throughputs, allowing the Economic Line to process 4 tons/hour of dry food, 3-3.5 tons/hour of moist food and 2-3 tons/hour of treats.
Reduced downtime for changeover and sanitation is accomplished with an automated barrel opening that facilitates immediate screw access. Quality is ensured through computerized operation, and Clextral offers traceability software to certify raw ingredient consistency.
Also available are clip-on modules for the production of multicolor and/or co-extruded (filled) products. These kits are pre-engineered for the extruder and include all ancillary equipment, greatly reducing downtime for reconfiguration. For details, visit www.clextral.com.
Removing processing bottlenecks
Galen J. Rokey, Wenger Manufacturing, notes that a line audit can identify bottlenecks to higher capacity. Bottlenecks that can limit throughputs of an extrusion line include:
Preconditioning capacity. Of all the preconditioners available today, the differential diameter/differential speed preconditioners have the best mixing characteristics combined with the longest average retention times. To fix or compensate for inadequate preconditioning, use one or more of the following steps: increase preconditioner size; increase existing preconditioner fill by one-time adjustment of beater configuration; add automatic retention time control system; and increase energy inputs in the extruder.
Available extruder power. When power is the limitation to more throughput, the options to remove this bottleneck are to a install a larger extruder drive motor; check with the extruder manufacturer to determine maximum allowable installed power; and factor in the effects of removing other bottlenecks (improved preconditioning). Extrusion systems are available with powertrains of over 2,000 kW. Lack of power is the most common bottleneck to higher production rates for existing process lines.
Extruder volumetric capacity. A bottleneck due to volumetric capacity is usually manifested by the extruder operating in a "choked" or full condition. Volumetric capacity can be increased in one or more of the following ways: install a larger extruder screw diameter; increase extruder screw speed; configure the extruder with screw geometries designed for maximum conveying efficiency; utilize grooved barrel liners; and control extruder barrel temperatures with heating/cooling systems.
Die open area. A specific die open area is required to develop the proper back pressure and barrel fill in the extruder.
Increasing the die open area to increase throughput potential is a straightforward relationship. Many die design techniques are employed to increase the number of die openings and the total die open area.
Downtime reduction. Downtime is often overlooked as a bottleneck to higher plant capacities. Many manufacturers believe they operate their lines 24 hours a day, seven days a week, and are surprised to find they have 20% of actual downtime. Practices that can reduce downtime are adjusting production schedules for minimum product switch-over time; installing hardware tools with quick-change features; designing control systems for compressed start-up/shutdown modes; training production personnel to reduce downtime; implementing preventive maintenance programs; and designing system hardware for maintenance and cleaning accessibility.
Increasing usable product. Increasing usable product is also a significant opportunity to increase capacity. Off-spec product may run as high as 8% of total production. Ways to increase levels of usable product include automated retention time control in preconditioners to reduce start-up/shutdown wastes; screw element and liner designs to give positive conveyance; high extruder speeds and variable-speed drives to shorten process response times; online, automated control of SME and recipe analysis; automated extruder control systems that compress start-up/shutdown modes; experienced production personnel to control process; process flows that handle the product gently; and waste recovery systems to recycle off-spec product.
Upstream/downstream unit operations. Most bottlenecks occur along the process flow in areas other than the extruder. An audit to increase plant production levels should include an evaluation of each unit operation along the entire flow. Potential bottlenecks could be found in one or more of the following areas: grinding/sifting, storage, conveying, drying/cooling, coating or packaging.
All unit operations along the process line must be properly sized to avoid a flow bottleneck. As each bottleneck is identified and eliminated, a new, secondary bottleneck will likely appear. A different bottleneck may be identified for each product that is manufactured in a given process line. This auditing process can continue indefinitely, but at each step it is necessary to do a cost/benefit analysis to determine if the economics are favorable. For more information, visit www.wenger.com.