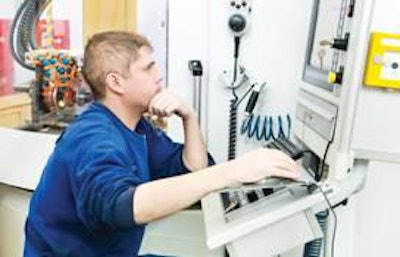
Petfood manufacturers are looking for innovative ways to modify existing facilities and processing lines to accommodate the safest petfood processes possible. But as the recent Nestlé Purina recall of dry cat food due to Salmonella contamination demonstrates, there are significant challenges in manufacturing, packaging and delivering these products in the supply chain. The easiest way to combat troublesome issues such as recalls and contamination is to focus on just how your food and treats are being made and look at what equipment you are currently using to take your product from a recipe and a batch of ingredients to a totally safe, sealed, packaged meal.
When a petfood company wants to upgrade food safety, the facility must first be analyzed. Key processes that might create risk or potential pathways for microbial contamination should be identified. Next, enhancements to the system currently in place must be completed successfully. Although this article focuses on hardware and equipment that can be used to upgrade a processing line's safety, not only manufacturing methods require re-engineering. The understanding of plant personnel toward sanitary practices needs to be emphasized and should be thoroughly understood. Every aspect of the facilities—from product movement through the plant and contamination from outside sources to equipment design—all require rethinking in light of recent Food and Drug Administration regulations, sanitary practices and good manufacturing processes.
According to David S. Mast, PE, senior project manager at SSOE Group, the major plant areas that are typically impacted by this sort of overhaul include processing lines, floor surfaces, drains, waste systems, HVAC, dryers, raw ingredient handling and packaging—nearly every system in a manufacturing plant is a contamination pathway. Every surface that contacts a product must be examined for potential microbial growth. Moisture, in contact with product, is one of the primary concerns and creates the potential for unsanitary conditions. Airborne dust, pollen and pesticides migrating into the plant can contaminate the product. The treatment of fines, the product dust that collects at the bottom of all process and packaging equipment, may be another contamination pathway that is overlooked. Now to arm yourself with the best possible tools to keep your pet products sanitary, safe for people to handle and animals to eat!
Tapco Polyethylene, Nylon and Polyurethane buckets are made with FDA-compliant resins. Both the plastic and pigment are FDA-approved, according to the company. Tapco buckets contribute to food processing safety because plastic resins will not leach into or affect the integrity of ingredients used for food products. Precision injection molds create non-porous surfaces and seamless construction, which means commodities tend to slide off, not stick, leading to minimal cross-contamination and a bucket that is easier to clean and keep that way.
The Mepaco line of Clean Sweep surge loaders eliminate loss yields and cross contamination as well, according to the company. Equipment sanitary design and operation are critical elements to the control of bacterial contamination in processing plants, and Mepaco designs and builds all its products to comply with the most stringent sanitary design principles. According to Mepaco, their surge loaders are cleanable to a microbiological level, are accessible for inspection, maintenance, cleaning and sanitation, and don't allow for product or liquid collection because hollow areas should be hermetically sealed. The surge loaders are available with bead-blast, pickle passivated or electropolished finishes.
National Bulk Equipment Inc. offers a sanitary tote dumper designed specifically for compliance to FDA, US Department of Agriculture, 3-A, BISSC or international standards, according to the company. The dumper includes clean-in-place features such as 304-2b stainless steel framework, sheet and plate; a fully enclosed, 304-2b stainless steel, hydraulic pump cabinet; and non-metal components with resistance to corrosive materials.
As much as petfood manufacturers attempt to control Salmonella, E. coli and other contaminants, they're still able to enter or move around the plant on personnel and equipment, via airflow and through contaminated ingredients. Fortunately, Wenger has addressed the problem with a full line of hygienic products known as the Wenger Hygienic System Components. Offerings include Waste Recycling Systems to capture emissions and/or under-processed material to prevent recontamination; a new, closed-loop Pneumatic Conveying System; on-line measurement and control systems to decouple personnel from direct product contact; new, stainless-steel hygienic machine frames that can be retrofitted to pre-existing extruders; and a new preconditioner slide gate and dust-tight downspout. Under-processed material and dust, which can act as a host for pathogens, are the greatest sources of contamination. Stopping them in their tracks is one of Wenger's primary goals, according to the company.