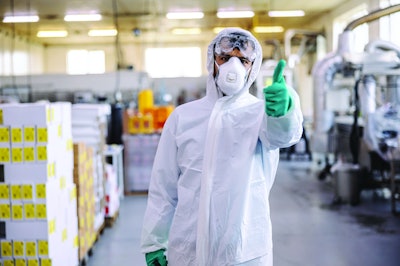
Pet food safety concerns continue to evolve alongside consumer expectations, and there’s no doubt that 2020 brought those concerns to the forefront in some perhaps unexpected ways.
“With the shift in buying from COVID-19 favoring e-commerce, a focus on high-quality food that can easily be shipped and stored has come back into focus,” said Nadeen Myers, technical development manager for Balchem Corporation, a company involved in the development, manufacturing and marketing of specialty performance ingredients and products for the food and feed (among others) industries. “Higher protein diets, unique proteins, ‘raw’ foods, these various diets are all at greater risk for microbial contamination.”
Obviously, customer opinion is key, so finding additional ways to ensure the safety of these premium or specialized diets, becoming increasingly popular in the market, from sourcing to production to transit is vital.
“Ensuring that quality parameters and safety standards are appropriate and upheld in the industry is crucial to maintaining the high level of trust that consumers enjoy, especially in the context of direct-to-consumer and fresh, never-frozen, product safety,” said Megan Ross, food safety product manager for global ingredient supplier Kemin. “As pet food follows the human food and beverage trend in accommodating new and at times exotic ingredients, pet food producers may have to widen the depth and breadth of their sourcing efforts and supply chains. Ingredients including duck, alligator or boar paired with sweet potatoes, plantains or ancient grains are not uncommon in pet food and pet food products. Less common raw materials can require new sources and supply chains which must be analyzed for potential hazards such as longer shipping, storage and new or different preservation protocols to retain freshness.”
Challenges met along the supply chain
“In addition to general safety trends behind creating safe, quality foods with higher protein contents and moisture levels, ingredient sourcing will continue to be an area of focus for consumers,” said Myers. “From grain-free diets to reactions from the recent aflatoxin recalls, consumers are demanding high-quality ingredients for their furry companions.”
Recalls are the worst fear of any pet food producer, and being able to keep track of what’s going in and out of a facility is one of the top ways to stop a potential recall before it starts.
“The ability to track all ingredients that go into a pet food product is the goal that every processing company should strive for and be held to,” said John Cerak, sales and marketing director for Computerway Food Systems Inc., which offers integrated production and inventory control systems and support for the food processing industry. “Knowing the origin of each ingredient, the product(s) that it was used in and its current location (plant floor, warehouse, shipped to pet store, etc.) are all key in successfully carrying out a precise recall. Providing safe food should be top priority for all pet food companies, and removing any unsafe food from the supply chain as quickly as possible should be a close second.”
Automation technologies in pet food production
One of the areas of food production that saw an understandable boost in 2020 is automation, and technologies that were already on the rise are now in the limelight in both existing facilities and those yet to be built.
“In recent years, the food and pet food industries have optimized supply chains to be globalized and highly efficient,” said Tim Hartter, project manager, corporate project services for industrial equipment supplier Wenger Manufacturing Inc. “However, the challenges presented in 2020 have brought to light the need to build flexibility and resilience into the supply chain to ensure continuity. These challenges expose the need to build redundancy, viable regional and international solutions, and end-to-end sustainability into the supply chain.”
COVID-19 wreaked havoc on manpower, forcing production facilities to begin looking at ways to continue getting things done on schedule with a reduced or more staggered employee force at any given time.
“What our customers are asking for is more automation,” said Cerak. “They want to be able to get the same amount of production out, or even more production out, and not need people standing shoulder-to-shoulder to do it. We’re getting asked to move things to digital and then automate them more to keep their employees safe and healthy, which allows them to continue processing.” (For more on employee safety, see “Pet food employee, facility safety in a post-COVID world” on p. xx.)
According to Ray Spurgeon, metal detection product manager for global separation technologies expert Eriez, technology needs to be “smart” in order to help the pet food industry produce at peak efficiency.
“One significant trend is the Internet of Things (IoT) — the network of connected ‘smart’ devices that communicate seamlessly over the internet. For pet food processors, IoT devices can transmit information that is useful across multiple process lines and provide valuable data (from, for example, connected metal detectors).”
IoT technologies can also provide ways for equipment and technology providers to remotely support their clients — a definite benefit when in-person visits are still being limited due to COVID-19 precautions.
“If we can leverage IoT solutions to see in real time and easily what is happening, we can support our clients,” said Matthew Craig, senior vice president of sales, food, chemical and performance materials, for Schenck Process LLC, a leader in measuring and process technology. “We are currently beta testing an online platform to review operating parameters with customers in real time. The platform does not control our clients systems and is completely independent; it is only an online dashboard setup where our technicians can help our clients start up or troubleshoot their Schenck Process Efinity Dense Phase Conveying systems. We felt this was the best place to start to provide the option of not having to have people travel to site and risk infection during the pandemic.”
Pet food safety in 2021
With COVID-19 still a very real concern, automation technologies continuing to advance, and new ways of doing business being established, it’s safe to say that the pet food safety landscape will continue to shift throughout 2021.
“I believe this is a very exciting time for nutritionists and technologists in the pet food industry,” said Myers. “We continue to see an increasing global demand for high-quality, nutritious products that must resemble food designed for humans. However, we must ensure the raw materials, ingredients and finished products are safe, legal and appropriate for our pets. While this aspect may seem challenging, as an industry it is a great time to be creative and think out of the box to deliver new innovations.”