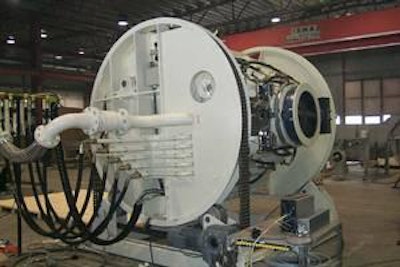
In the past decade there has been great development in the production of petfood diets made from extruded pellets. An important part of the development is the addition of different liquid additives such as digest improvers, vitamins, fat and appetite improvers.
Palatability is a key factor in producing high quality petfood. Besides involving a careful selection of ingredients, it involves the right processing technique. The multiple layer coating possibility provided by the Forberg rotating vacuum coater (RVC) has an important impact on the food quality.
Forberg International AS has been on the front lines with vacuum coating ever since the process was introduced to the industry making pelletized fish feed in the beginning of the 1990s. This technique has made it possible to increase the level of energy in the feed to new and higher levels.
It is of great importance to keep the pellets dry on the surface even after adding the different liquids, and the process of vacuum assisted intrusion of liquid in the pellets is playing an important role.
Adapting the RVC to the petfood market
To meet the requirements of the petfood market, some
adaptations to the RVC have been made (although dry petfood has
many of the same physical properties as fish feed, at least
concerning the ability to utilize the vacuum technique). These
include:
• The use of fat with a melting point higher than the
ambient temperature has triggered use of special heat cable
tracing of hoses to the nozzles and even tracing of the nozzle
assembly itself;
• Heat is traced and the coater body is insulated to
prevent build-up of solid fat in the machine;
• The machine housing and rotors can be made in stainless
304 or 316 depending on the level of acid addition.
Benefits of the Forberg RVC
The Forberg RVC is a machine that is especially developed
for using vacuum to improve the intrusion of liquids in porous
extruded pellets. Important features, according to the company,
include:
• Loading and unloading the machine through the same valve
minimizes the risk for leakage;
• Loading/unloading valve is out of the process area
during processing, ensuring what is put into the machine stays
there until the charge is ready for unloading;
• Smooth process chamber with accurately adapted rotors
ensures very low wear and breaking of the pellets during
processing;
• Total control of the vacuum cycle for the rate of
equalizing back to atmospheric pressure gives an optimum
capacity of inclusion;
• Easily included cleaning in place system allows thorough
and fast cleaning; and
• Machine is easy to change between formulas without
risking cross contamination.
Cycle and principle of operation
After pellets have been loaded through the inlet valve of the RVC, the valve is closed and the preset level of vacuum is obtained. The next step is to add liquid additives through the single-component nozzles on the machine while the rotors are running. Forberg says the RVC's ability to fluidize the product and its high internal transport capacity are the reasons the distribution of the different liquids is possible at a high level. This principle allows perfect distribution directly on each pellet even for very small quantities of liquid additive, according to Forberg.
After distributing the liquids onto the surface of the pellets, the carefully monitored process of equalizing the pressure inside the process chamber back to atmospheric presses the liquid inside the pores of the pellets, leaving the surface dry.