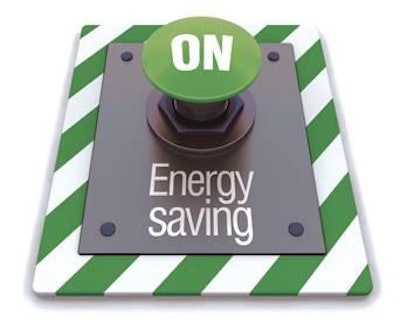
Running an energy-efficient petfood processing line isn't just important for the environment—it's important to your company's bottom line. Alternative cooking processes like pasteurization and direct contact steam injection can help by removing pathogens and sealing in flavor at lower cooking temperatures, while sanitation-obsessed machinery and operator-friendly cooking equipment can make processes run faster and smoother. Here are several petfood and treat extruders, dryers, coolers and cookers that will help manufacturers go 'green' in energy costs and their wallets.
Radio Frequency Company's Macrowave Pasteurization System uses a high-frequency electric field to control pathogens in petfood—a process often referred to as "lightly cooking." Utilizing clean electrical energy from the grid, the petfood formula to be treated is conveyed through a high-frequency electrode array where the alternating electrical energy causes the material to heat rapidly and uniformly throughout the product thickness, according to the company.
Radio Frequency heating is a highly efficient, "direct" form of heating such that no energy is wasted heating large volumes of air or preheating the system itself. The technology is "instant-on, instant-off," using energy only during the treatment process. This green technology line of Macrowave Pasteurization Systems operate at 40MHz, ensuring effective microbe kill and avoiding the deleterious effects on product quality from prolonged exposure to high temperatures. These systems from Radio Frequency are available in conveyorized or batch configurations.
Petfood Steam Cooker Systems from Hydro-Thermal feature a unique, 100% energy-efficient heating process called direct steam injection (DSI). According to the company, DSI heating is a general term that refers to any type of fluid heating that utilizes steam being directly mixed with the utility or process fluid. Several forms of direct steam injection include: spargers, externally and internally modulated heaters and educator pumps. The advantage of using direct steam over indirect heating methods, Hydro-Thermal claims, is that directly injecting steam into the process fluid is totally energy efficient because it uses both the latent and sensible heat available in the steam. According to Hydro-Thermal, by replacing the old sparge system or heat exchanger, you can eliminate energy costs up to 30% in your processing line.
Bühler Aeroglide has developed a number of innovations focused on sanitation and efficient cleanability, and is incorporating them into the latest generation of its dryers, roasters and other thermal processing systems for petfood applications. Improvements in sanitary design come in the form of one-piece slab roofs and floors that are pitched to one side of the machine to eliminate water pooling; a comprehensive water management system that directs water and other cleaning fluids to a drain; a non-tubular open channel frame design that eliminates water and fines entrapment areas; minimized flat horizontal surfaces, crevices and other collection points making cleaning easier and faster; vertical and horizontal support members that have been turned 45° to further decrease cleaning time; access doors that feature a continuous and polished weld on all seams combined with surface mounted hinges and handles, providing an unbroken barrier against water collection and bacteria growth; and a number of other design improvements to aid in energy-saving and time-saving.
“This is not a package we slap on a dryer and call it ‘enhanced’ or ‘extra sanitary’,” says Steve Blackowiak, food safety manager at Bühler Aeroglide. “These innovations are the result of a mindset that is core to our engineering mentality and permeates the design of all our products." The company debuted many of these customer-inspired sanitary innovations in a dryer installed in the recently-opened FDA-grade Food Innovation Center at Bühler’s Minneapolis, Minnesota headquarters. The new lab allows Bühler customers to run process trials on a complete extrusion line including raw material handling, extrusion, drying, grinding and bulk packaging.
Wenger's most recent work dedicated specifically toward energy efficiency has been the development of Wenger's Thermal Twin Screw extrusion system. The Thermal Twin extruder, with its patented steam injection system, has the capability of utilizing up to four times more steam in the extruder barrel than previously possible, says the company. "This allows a shift of the process to a more economical energy source by utilizing thermal energy rather than mechanical energy for the cooking process," explains Doug Baldwin, director of business development for Wenger. "This thermal extrusion process also has the added benefit of being able to use a wider range of high fat and/or high moisture raw materials than was previously possible with traditional extrusion processes."