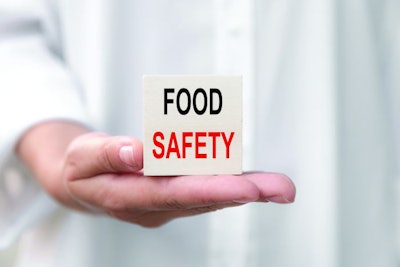
Pet food safety is a constant conversation, and for good reason. A missed toxin, a recall that comes after pets get sick, a failed safety inspection … any of these could and likely would mean significant trouble for a pet food company. But it’s also a complex conversation with plenty of ways to step wrong, which makes having a robust and comprehensive food safety plan a must for long-term success.
Top challenges in a food safety plan
Industry experts agreed that food safety plans can be daunting, but there are some clear (if multifaceted) areas that pose the greatest challenges. Dr. Michele Sayles, executive director of food safety and quality for Diamond Pet Foods, identified three main concerns:
- Identifying all existing and potential hazards and staying abreast of new and emerging hazards.
- Examining each hazard and creating strategies and specific procedures to ensure it is adequately and appropriately addressed.
- Effectively communicating these procedures in a practical way that is easy to implement and track in everyday operations.
During a January 2022 Petfood Industry-hosted webinar, “How to manage FSMA requirements and pet food product recalls,” law firm Husch Blackwell Partner Ryann Glenn said one of the biggest gaps she’s seen in food safety planning is not identifying those hazards.
“I would say the hazard analysis and preventive controls, to where a party is not thoroughly going down the entire line of their production of pet food and only looking at the entire process in a vacuum [is one of the biggest breakdowns in planning],” she said. “So they’re not identifying all known hazards, and by default they’re not able to identify whether or not a known hazard that occurs frequently or has the potential to occur frequently needs a preventive control. So that can significantly impact your risk down the line.”
Understanding the procedures can save time when it counts, on top of ensuring smooth sailing from one end of the food safety plan to the other.
“The top challenges our clients often face involve understanding the next steps in the process of production,” said Jamie Wood, senior account manager for pet food and animal feed at Midwest Laboratories. “We will get calls about what comes next after a presumptive positive or what results mean to their operations. Midwest Labs is not a consulting laboratory, but we often assist in helping our clients identify trends and contaminants in their supply chain or setting up samples for confirmation and speciation after a presumptive positive. These are important steps to biological tracking.”
Testing and education go hand-in-hand
Everyone agrees that testing is a key component to a food safety plan, and that it should be incorporated at multiple steps in the process.
“On-going testing [is a must], both at grain/product receipt from an inbound perspective,” said Christy Swoboda, technical services director at Romer Labs. “So, testing of materials before you put them into production; monitoring after production through composite testing; continuing to check that the inbound testing was effective and caught any mycotoxin load before being accepted in; understanding which test kit is fit-for-purpose with the samples and limits of detection that you need; understanding test kit limitations and how that can adversely impact your testing results.”
Of course, for testing to be accurate those involved must know what they’re doing, so training is another key to success.
“Food testing often requires specialized and trained staff to run analyses and access to such qualified staff can often be an issue,” said Henrik Elholm, Foss global market manager for feed and pet food out of Denmark. “Having necessary internal educational programs to maintain staff qualifications is of the essence. Alternatively, producers may rely on tests at external facilities, but this will significantly reduce the time to get results and ability to quickly act on the results. Establish in-house testing capabilities using fast and simple-to-use test methods is often preferred and can be supplemented with analyses at commercial laboratories.”
In addition to food testing during the process of making pet food, another type of testing should be discussed: that of the food safety plan itself.
“There are two areas that I find have the most issues,” said Emily Lyons, partner at Husch Blackwell. “The first is you’ve never tested your recall plan in any way or you don’t really have one even though it’s required by the regulations. And that is just kind of internally who has the ball. Who is in charge of this recall, who is owning it, what are the recourses that we can use to help implement it and make sure that it’s done effectively?
“And the other area is effectiveness checks,” she said. “Some of the companies that I’ve worked with that manage their recalls on their own initially and then call me afterward when they seem to be running into a disconnect with the agency is that they’re failing to follow up with their consignees to make sure that the recall has been carried out. And it’s really, really important to make sure you have the effectiveness checks in place.”
Everyone should be invested in a food safety plan
The easiest way to ensure a pet food safety plan’s success is for everyone in a company to be invested in food safety.
“Food safety is not just a Quality Control or Food Safety department function or responsibility,” said Sayles. “It is important for all departments — operations, sanitation, maintenance and management — to be engaged and understand the program, how it works and why we do it. Buy-in from all departments including management is one of the most important keys to a successful and sustainable program.”
Part of that buy-in means diversifying your food safety team.
“I find having a multidisciplinary team with a team lead really important, both at the facility level and potentially at the corporate level where you have a facility representative as part of a corporate plan if you’re a bigger company,” said Lyons. “One of the things that FDA (the U.S. Food and Drug Administration) is really starting to push for, is they’re going past compliance. They also want to know that you have a culture of food safety within your facility. Everybody understands their roles under both the CGMPs (current good manufacturing practices) and the preventive controls rule and sees how they have an impact and an ability to affect the safety of the products that are being produced.”
Finally, aiming for the highest standards is truly the only way to succeed in pet food safety.
“Pet food has experienced tremendous growth, not only in volume but also in terms of new products,” said Elholm. “Some of these are related to less-processed and more natural pet foods. And at the same time, regulation is constantly changing. Pursuing high food safety standards, where producers can ensure that products are kept safe, is absolutely necessary to maintain customer relations and protect brand equity. This development is likely to continue and may put even more pressure on the industry to adopt best practices in food safety. This will likely imply even stronger cooperation between producers, suppliers of analytical solutions and quality management systems as well as regulators to ensure even more efficient and transparent food safety systems.”
WEBINAR: How to manage FSMA requirements and pet food safety recalls