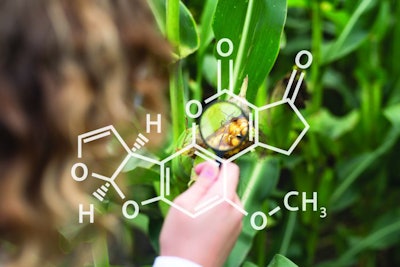
As the cold winter months set in, it can be easy to underestimate the risk of aflatoxin. Typically, it is a hazard that we spend our time, money and effort to understand when utilizing new crop corn each fall. However, the timing of recalls due to aflatoxin since 2020 suggest that this is a hazard that requires monitoring beyond post-harvest. Aflatoxin is consistently the most mismanaged hazard that I find when reviewing a facility’s food safety plans.
Hazard analysis: Moderate severity, varying probability
Aflatoxin is a known or reasonably foreseeable hazard in most grains and in the storage step of an animal food safety plan. In pet food facilities, I typically determine the hazard has a moderate severity because it can cause substantial illness and death to pets, but there is not often an immediate risk to humans. This is contrary to the high severity of aflatoxin in dairy feed. When dairy cows consume aflatoxin, the toxin is metabolized and can pass through milk, thereby causing illness to both the cow and human consuming cow milk. Likewise, the moderate severity assessment of aflatoxin in pet food is contrary to the high severity of Salmonella, where the cross-contamination risk due to frequent home storage of pet food can cause significant risk to human health.
However, aflatoxin is not known to spread as easily through cross-contact, so the risk of aflatoxicosis is typically limited to the animal consuming the affected product. For this reason, I typically rank the severity of aflatoxin in pet foods as moderate, with the justification that there is the potential for illness or death of animals consuming the hazard, but little pass-through risk through consumed tissue or products that impact human health.
The challenge with aflatoxin is that its probability is constantly in flux. Instead of reanalyzing the animal food safety plan each growing season, I find it more effective to implement an aflatoxin prerequisite program to control the hazard. Some facilities may implement the same procedures and call it a preventive control. Regardless of the name, I find that when implemented properly with sufficient records, this approach effectively manages the probability of aflatoxin in finished products.
Hazard control: Staging strategies are key
Actions to control aflatoxin should have at least three steps: 1) utilizing approved suppliers, 2) observing the receiving process and 3) implementing an effective dynamic testing process to verify the controls are working.
1. Use approved suppliers
An effective control program identifies the approved suppliers for all the ingredients that can be received. In a commodity-based world, this may mean that various farmers, brokers or co-ops may be the approved entities that are allowed to deliver to your facility. This does not need to be a complicated process, and can be as simple as a list like as follows:
- The following products may only be received from these suppliers:
- Corn: Company X, Broker Y, Farmer John Doe, Farmer Joe Smith, Farmer Jane Jones
- Corn DDGS: Company Y, Broker Z
- Corn gluten feed: Company M, Company O, Broker Z
- Corn gluten meal: Company M, Company O, Broker Z
2. Visually observe the receiving process
An often-missed step in hazard control is to visually observe its unloading. While aflatoxin itself is not visible to the naked eye, it is often accompanied by other indicators of poor-quality conditions. This may be specified in the animal food safety plan and reinforced with signage in the receiving operator’s office:
“The entire receiving process is visually observed by a Receiving Operator. If black or moldy material is observed in susceptible ingredients during the unloading process, the conveyor from the pit to the bucket elevator is immediately stopped. The contaminated material is manually probed, ground and analyzed. Based on the result, the ingredient is either received or diverted to an empty loadout bin and removed from the facility.”
3. Utilize dynamic testing to verify actions
If a facility knows the geographical region an ingredient was grown in, that information can be considered as part of the frequency of testing. However, when the geographic source is unknown, testing frequency may vary from a daily composite with a weekly weighted average, to a daily composite by supplier, to a test-prior-to-receipt process. Here are the stages that I typically find useful:
- Stage 1: General daily composite. A daily composite is built at the scale house and tested daily, then rolled into a weekly weighted average. If each daily composite is below 10 ppm aflatoxin and the weekly composite is below 5 ppb for aflatoxin, no further action is necessary. If either occur, Stage 2 is implemented.
- Stage 2: Supplier daily composite. A daily composite for each supplier is built and tested daily, then rolled into a weekly weighted average. Any suppliers identified as having daily composite levels above 10 ppb will be moved to Stage 3, while other suppliers may stay at Stage 2.
- Stage 3: Load-by-load test prior to unload. Suppliers that fall into Stage 3 will only have loads accepted if each load is determined safe. Prior to unloading, at least 10 probes are collected using a double X pattern. The probed samples are combined, ground, sifted through a No. 20 sieve and analyzed for aflatoxin in accordance with the varying manufacturers’ recommendations. Only loads with a composite sample analysis of <19.9 ppb aflatoxin can be received. If the composite sample is >20 ppb, the load is rejected.
Typically, suppliers can return to a previous stage after one week or 10 consecutive loads that meet the previous stage’s parameters. However, if a supplier has more than four weeks at Stage 3 or a single load or composite sample >40 ppb, the supplier should be removed from the approved supplier list.
Effective implementation and records demonstrating these steps are key. These should also be accompanied by a test-and-hold process in finished product. Most importantly, a true quantification of aflatoxin is important in this method. A single grab sample analyzed by a test that only indicates +/- 20 ppb does little to help us truly understand the risk of aflatoxin. A robust testing program and decisions based on the resulting data help us best control aflatoxin and keep it out of finished product.
5 ways to avoid aflatoxin in pet food ingredients