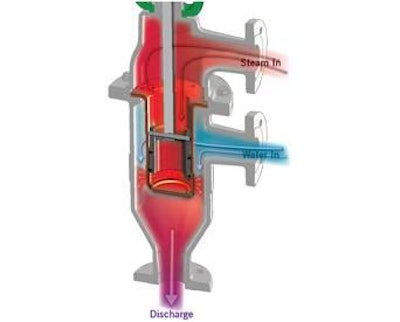
Direct steam injection (DSI) heating is a specific method used during petfood and food processing where steam is directly mixed with the process fluid that needs to be heated. This type of heating is seen as an efficient, cost-effective alternative to indirect-contact heat exchangers, which have multiple fluid flow paths that don't allow for direct mixing of the fluids.
The benefits of DSI, according to Ed Beecher of Coperion Corp., are significant. In his Petfood Forum 2014 presentation, "Innovations available for petfood extrusion processes," Beecher said the single-stage process requires no preconditioning and provides reliable production. In addition, since the process utilizes direct thermal energy input, it reduces the need for specific mechanical energy input, which results in lower energy costs than other methods of heating.
There are also more physical advantages, according to Hydro-Thermal Corp. "Both equipment expense and space requirements can be trimmed," said the company. "Direct-contact steam injection systems generally require less space than other methods of heat transfer, and they also eliminate the need for condensate return systems, which are often required for indirect heat exchangers. Additionally, maintenance costs may be significantly lower than those of other heating systems."
There are multiple types of DSI heaters currently in use, with varying abilities and limitations, including externally modulated devices such as spargers and mixing tees, and internally modulated steam injection heaters.
External modulation varies the velocity at which the steam is injected into the liquid, as well as the relationship between the steam and the liquid. The transfer of thermal energy is quick and efficient, but accurate temperature control can be difficult to maintain under certain load conditions, according to Hydro-Thermal.
In sparging, the oldest and simplest method of direct steam injection, steam control is attempted via an externally modulated steam control valve. Steam is injected directly into a fluid-filled tank, and the steam pressure is adjusted to control the flow rate of steam with a control valve. There are several issues with sparging, according to steam injection heater manufacturer ProSonix. For one, steam hammer and vibration often result from poor mixing and condensing of the steam. As temperature demand drops, steam pressure drops, lowering the steam velocity and potentially causing instability. Uncondensed steam bubbles will typically collapse when they come in contact with a cold pipe wall in the liquid piping. When these bubbles collapse, the water rushes in to fill the void and impacts the pipe wall. In some cases this will result in some pinging noise and, in severe cases, steam hammer and vibration. Equipment failure can result due to the vibrations.
Poor temperature control and energy loss are two more pitfalls of sparging. According to ProSonix, up to 30%-40% of steam energy can be lost to atmosphere. The system is also prone to tank failure and high maintenance costs.
Mixing tees offer manual, semi-automatic and automated systems that mix steam and cold water with varying degrees of accuracy. With manual systems, where an operator controls the cold water flow rate and the steam valve, only approximate temperatures can be achieved, according to Hydro-Thermal. While semi-automatic mixing tees have preset temperatures, they (like manual systems) experience difficulty in compensating for changes in steam or water pressure or hot water demands.
Other, more sophisticated externally modulated systems control the steam flow rate from outside the injection device. Steam is injected downstream of the control valve through multiple orifices located inside the steam injection heater. A piston rises and falls with changes in the steam flow rate, compensating for changes in steam pressure, inlet water pressure and hot water demand. But, because the steam is still controlled outside the injector, the pressure at the point of injection can vary and upsets in the system may occur, said Hydro-Thermal.
Internal modulation controls both steam flow and mixing by employing a stem/plug assembly inside the heater.
Internally modulated heaters are the most efficient of DSI options, using the full steam pressure available to choke the steam flow through precisely engineered nozzles. Choked flow, according to ProSonix, allows for the metering of steam mass flow to control the heating of the liquid. There are multiple advantages to using internally modulated steam heaters. One is that there are no process upsets-the high-velocity steam flow optimizes the steam mixing and condensation with the liquid, as well as eliminates the problems with steam hammer and vibration found in sparging.
There's no external steam control valve required in internal modulation, and temperature control is extremely reliable-rapid and complete condensation of the steam allows for temperature holding to within +/- 1°F. High-velocity steam is self-cleaning and eliminates debris along scale and mineral build-up on the steam diffuser, which results in lower maintenance costs.
Overall, the sustained benefits of DSI are measurable when compared to indirect heat exchangers. DSI near-instantaneously transforms heat energy with 100% efficiency. Productivity increases, as DSI can handle fluids that are difficult to heat (highly viscous or abrasive slurries are no problem). Perhaps most notably, cost savings can be seen in multiple areas: lower production costs, reduced maintenance costs and energy savings are all hallmarks of using DSI. All these benefits together make DSI a viable option for petfood producers.