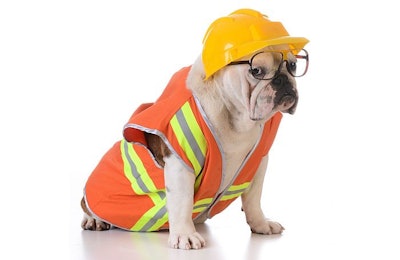
Pet food producers, ingredient suppliers and others in the industry continued construction and expansion of facilities in 2020. In some areas of these plants, established food security protocols evolved into human health measures. However, the pandemic did increase the use of automation in other parts of the operations, such as offices and cafeterias. Likewise, fewer visitors came to the offices and conference rooms as digital communications replaced potential passing of pathogens.
Automation and digital communications in the pet food industry
“The pandemic has pushed pet food manufacturers to look carefully at automation and how it could improve or support their process,” Jeff Roy, senior project director for engineering, architecture and construction company CRB, “Automation reduces the need for human intervention. It can play a critical role in safe and future-proofed manufacturing, but owners have to weigh the cost, maintenance and effect on the labor force. People are the source of the contagion so there is a lot of discussion about how can we further automate? How can we arrange workspaces to separate workstations and work practices?”
“We’ve learned flexibility,” Lyndsi Stafford, chief bark-eting (sic) officer for Nature’s Gnaws, said. “Our administrative staff worked from home during the pandemic and through the use of technology we were able to continue operating successfully despite working in various locations... We’ve upgraded our equipment, allowing us to do more work with less people in the warehouse.”
“COVID has forced us to look at our company and make operational changes for the better,” Stafford said. “We’ve upgraded our equipment, allowing us to do more work with less people in the warehouse. We continue to hire during this pandemic but we are operating safely and efficiently.”
Adapting pet food production facilities for human health
Office workers, business travelers and other white-collar pet food professionals found themselves spending far more time on Zoom in 2020, but on the production floors existing automation and food security measures morphed into pandemic preventatives.
"We had already been utilizing automation and computerization for our Customer Laboratory Services...," Alberto Muñoz, marketing director for pet food ingredient manufacturer Kemin Nutrisurance, said. "Our new QC Lab was designed with the same automation and efficiencies in mind."
In production facilities, existing measures meant to keep germs from getting on pet food also helped keep the coronavirus from passing between people.
“Pet food processors must pay close attention to employee and raw material segregation, hygiene, equipment design, conveyance, cleaning and inspection,” Jeff Matis, senior project manager for CRB, said, “This is no different from human food processing facilities.
“Facility design and organization all starts with establishing material segregation, personnel segregation and hygienic zone definition. Raw and cooked side segregation is now the expectation, and process and support functions are organized around this primary demarcation. Designs should include a linear flow into the facility to maintain these zones of segregation. Cooking or kill steps are aligned with the same practices used in human food facilities, with many of the products processed post-cooking through packaging in high hygiene zones to reduce chance of cross contamination.
“The ideal flow will account for minimal personnel and material transitions. Reduction of personnel contact and transitions will help protect the workforce. We're helping clients coordinate and segregate personnel and material movement to the extent possible to enhance safety. In some cases, shared functions such as shift change transitions, breakrooms, parts storage and cleaning may function best segregated or separated.”
In many cases, existing procedures proved sufficient for pet food producers and their suppliers to carry on in the United States and other countries where they were acknowledged as necessary for providing pets with nutritious diets.
“Remote work has not influenced TOP’s Parrot Food’s work flow,” chief operating officer Gary Rubin, said. “The state of Oregon, where TOP's is located, deemed pet food an essential industry so we have been able to continue to operate at our facility with all necessary precautions in place.”
Similarly, the pandemic didn’t influence one pet food ingredient supplier’s use of automation, mechanization or computerization, Mike Wright, director of operations and business development of D&D Ingredient Distributors, said.
“As a basic manufacturer, the trend toward remote work has not directly influenced D&D’s work flow,” Wright said. “However, with our supplier interactions and technology transfer program, it has accelerated our use of virtual meetings, such as our recent ‘Knowledge X-Change’ program on the soy protein market for livestock production.”
“If there was any ‘pandemic influence’, it would be to reinforce already good decisions about technology,” he said.
As habits formed in response to the COVID-19 pandemic become established procedures, pet food producers and their suppliers may continue to benefits from good decisions about mechanization, computerization and other forms of automation and digital communication.