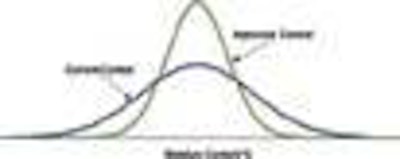
When it comes to petfood production, manufacturers know that time is money. The time spent removing moisture from the finished product is time wasted waiting to produce the next run. To minimize dryer time and prevent wasted energy that could be used more efficiently, moisture control becomes an important consideration.
This article will explain the differences seen in a petfood dryer operating under its "current control" versus an "improved" moisture control situation. As seen in Figure 1, the "before" and "after" moisture content (MC) variation curves for petfood exiting a dryer operating under current and improved MC control are demonstrated. The difference in moisture variation between the two curves is primarily a function of the dead time (time for a disturbance entering the dryer to be detected) for the respective control systems.
The dead time for current control, where the moisture sensor is located at the exit or beyond the dryer, is at its maximum. In comparison, the dead time for improved control, where the moisture sensor is inside the dryer and closer to the dryer inlet, may range from 35-45% less than that for current control. Since the moisture variation is directly proportional to the dead time, the moisture variation reduction is also approximately 35-45%. Because of its wider variation, the current control dryer must be operated with a significantly lower mean MC to prevent the production of wet product. The consequence of such operation is lower production, higher unit energy costs and poorer quality.
Since moisture variation of petfood exiting the dryer is directly proportional to the dead time, the most effective method for reducing the dead time is to place the moisture sensor inside the dryer.
"Improved" control
Looking at Figure 2, we see the same distributions as in Figure 1; however, the position of the improved curve is shifted to demonstrate the advantages of using a MC control system chosen under a new set of selection criteria. Because of its reduced MC variation (narrowed curve), the curve for improved control in Figure 2 may be shifted to the right until its + 3 standard deviation point coincides with the + 3 standard deviation point on the current control curve.
The difference between the means of the two curves is proportional to the benefits derived from improved control: Increased production; a reduction in unit energy consumption; and the elimination of over- and under-dried product. Additionally, the difference in the two means may be used to estimate the increase in MC that may be left in the product without exceeding the upper limit for MC. Improved control usually reduces the standard deviation from 35% to 45%, which allows the mean of the exiting moisture values to be increased about 0.5-1%.
Current MC control system
The main purpose of a MC control system is to keep the exiting product sample values within the specification limits with the lowest variation possible, so that the mean value will be maximized without exceeding the upper specification limit. Limitations inherent in conventional MC sensors require that they be installed at the dryer exit or beyond, thus dictating open- or closed-loop feedback moisture control systems.
Such "after-the-fact" control systems produce wide MC distribution curves as shown in Figures 1 and 2. Factors that negatively affect current MC control systems are addressed later in this article.
MC control selection criteria
As previously stated, the MC variation (standard deviation) of a product exiting a dryer is directly proportional to the time it takes for a change in water load to be detected (dead time); therefore, the location of the MC sensor with respect to the dryer is probably the most important factor influencing MC control. Since lower dead time equates to improvement in the bottom line, the ideal location for the MC sensor is inside the dryer.
Present practice is to continuously sense after-the-fact" MC at the dryer exit, or to periodically take samples for laboratory analysis. This type of sampling necessitates use of a feedback control system. Since such systems make only one correct control decision out of three attempts, they are extremely ineffective in tightly controlling moisture variation.
Conventional MC sensors require frequent, costly calibrations for just about every product dried. If installed, they are usually relegated to measuring trends in MC rather than as closed-loop MC control systems. Some serve as open-loop MC control systems that require step changes in the manipulated variable to be made by the operator in response to "after-the-fact" MC data. Therefore, a criterion for selecting an effective MC system is to select a sensor requiring no calibration.
Conventional MC sensors sense a relatively small spot on the surface of the product, thus neglecting the effect of vertical MC gradients. It is important that the sample be sufficiently large, frequently sampled for statistical significance and include the entire bed depth. Thus, another criterion for selecting an effective MC control system is to include a sensor that uses a statistically-significant sample.
Some manufacturers use exhaust temperature as a surrogate for product MC. This correlation holds as long as there are no water load changes entering the dryer. However, such changes are inevitable, and the operator must continually search in an "after-the-fact" manner for a new set point that will produce the target MC. Needless to say, selecting an effective MC control system should include the selection of a sensor that correlates strongly with MC under varying operating conditions.
MC sensor calibration is a major factor to be considered when selecting a MC control system. Frequent calibration and the need for custom calibration for all products require the selection of a MC sensor that is universally applicable to each dryer type and most products. To reduce costs and MC variation, select a sensor that will effectively operate in any environment on any product or dryer type. For a MC control system to be effective and accepted by the operators, it must be based on a MC sensor that is simple, rugged, reliable and one which requires minimum maintenance.
The control solution
The "Delta T" MC control system presently meets the recommended selection criteria for an effective control system for petfood. It has been proven to control various products from most dryer types. It is based on the patented predictive model seen below:
MC = K 1 (ΔT) p - K 2 /S q
This equation relates the moisture content (MC) of the petfood leaving the dryer to the temperature drop (Delta T = ΔT) of hot air after contact with the wet product and the dryer production rate or speed (S).
Figure 3 illustrates the manner in which the improved control system senses the MC inside a single- or multiple-pass conveyor dryer, or a vertical dryer using temperature sensors. After the hot air supply to the dryer contacts the wet product, the temperature drop of the air is used by the above model to predict the exiting product MC.
As the petfood passes the temperature sensors, if the temperature drop is higher than the set point value, the controller uses the Delta T value to calculate an output signal that increases the heat input. If the temperature drop is lower than the set point value, the heat input is reduced. Any change in water load entering with the feed will be detected and corrected before it leaves the dryer. This predictive model-based MC control system is automatically engaged by a "cruise control" method that requires no learning time or tedious and costly calibration.
Figure 4 shows the advantage of the "improved" moisture control system in continually forcing the mean value of the exiting petfood MC upward toward an operating value that is always +3 standard deviations below the upper MC specification limit (UCL). The installation of the improved control method reduces the wider variation (higher standard deviation) produced by the current control (left side of curve) and allows the mean value of the MC to be increased, without exceeding the upper specification limit.
As control is improved, the improved control system continually calculates the MC standard deviation and moves the mean (see dashed line shifting upward) MC value upward, always keeping it three standard deviations below the upper specification limit to ensure that the maximum amount of water is left in the product.
Criteria overview
As demonstrated in this article, the recommended selection criteria for a MC control system:
- Includes a MC sensor that operates insides a dryer to reduce dead time;
- Has a large sample size, including the effect of bed depth MC gradient;
- Includes a MC sensor that is simple to operate, rugged and reliable;
- Has model-predictive control needing no calibration or learning time;
- Is universally applicable;
- Utilizies "cruise control" operation to make it user-friendly; and
- Uses statistical methods to maximize water content of exiting product from 0.5-1.0% without exceeding the upper MC specification limits.
It is our view that due to the reduction in moisture content variation, the improved MC system will pay back the investment in less than one year.