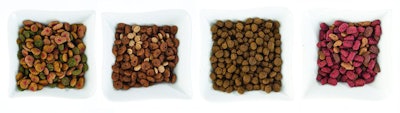
Equipment is a significant capital investment, which means a lot of factors come into play when it comes time to consider purchasing a new asset. Today’s pet food trends are more demanding than ever, which means the production line is expected to do more — that means looking for not just new equipment, but also new ways to use current equipment as companies evolve to meet consumer needs without breaking the bank.
“The pet food industry is changing fast,” said experts at CRB, a full-service facility design, engineering, construction and consulting firm for biotech, pharma, food and beverage, and science and technology. “To keep up, manufacturers need to examine their traditional equipment and processes, looking for ways to accelerate and diversify their operation without impacting quality. This isn’t about learning new tricks — it’s about improving the old ones.”
Efficiency: More important than ever to save on costs throughout production
Economic factors are more of a key focus than ever in the production process, which means current challenges such as inflation and labor shortages are making efficiency the name of the game in order to avoid raising costs beyond what pet owners are willing to absorb.
“Pet food manufacturers are looking/asking for equipment and technology that allow them to produce a certain product with precision control on quality, such as cooking level, color, shape and size, meanwhile saving raw materials and energy,” said Enzhi Michael Cheng, Ph.D., global business development manager for pet food and aqua feed with plant equipment manufacturer Bühler Group. “The challenges we at Bühler, as a full solution provider, are facing, are how to fine tune and develop the equipment and controls to meet all these elevated demands.”
One of the challenges in improving efficiency is simply in figuring out how to effectively change established procedures.
“The pet food industry is at an inflection point driven by two opposing forces: roduct-level innovation and process-level convention,” said CRB. “A new kind of consumer is driving the former, one that sees the household pet as a humanized family member and wants the dog bowl to contain the same diversity, quality and nutrition that they find on their own dinner plate. This has incentivized pet food manufacturers to rapidly expand their throughput, rethink their ingredients and add new products to their pipeline. These shifts may succeed in attracting today’s pet food buyer, but they introduce formidable challenges for an industry whose core production methods are well-established and not easily changed.”
Flexibility: Today’s needs are multifaceted and sometimes contradictory
“Challenges such as labor shortages, supply chain/ingredient disruptions, packaging shortages (especially in glass, aluminum and cardboard), increased costs in fuel pricing, transport logistics and energy, in addition to an ever-increasing focus on food safety regulations, are driving pet food manufacturers to seek new or evolving technological solutions to meet increased pet ownership,” said Ed Williams, general manager, Americas for high pressure technology provider Quintus Technologies. “Consumers are looking to provide their pets with healthier, safer, better-tasting, preservative-free products which provide greater digestibility, palatability and other benefits.”
It's a tall order to fill, to be sure, and flexibility would seem to be the key. But how can companies go about making their production lines more flexible?
“[We’re seeing a need for] flexibility in a single architecture that can produce products across multiple categories (LID, high meat, grain-free, low carb),” said Will Henry, R&D for machinery industry company Extru-Tech Inc. “The primary challenge with this design is to maintain an economic capacity (lbs./hr.) regardless of the product being produced. This is especially true with kibble.”
Dealing with multiple food types is a primary challenge of equipment suppliers working with their clients.
“As a manufacturer, we are helping processors to optimize the flexibility of the twin screw extruder to process multiple products on the same line,” said Hadrien Delamazure, process engineer for extrusion equipment supplier Clextral. “It is a small learning curve to help customers transition from making one food to multiple styles utilizing a variety of ingredients, as all their recipes are stored for easy access at the control panel. In addition, automated start up and shut down procedures allow processors to repeat the same optimized operations, without direct personal input from the operator: This saves time, reduces raw material waste and improves the overall production rate.”
How efficiency and flexibility needs will continue to shape the pet food equipment space
Demand for multi-capable equipment is only expected to increase around the complex needs of pet food producers to meet the goals their pet owner customers set for them.
“The main technological focus in the pet food industry is the precision of a full production line,” said Cheng. “This can be achieved by standardization of equipment and full automation control to minimize human error in everyday production. For the near future, we will see self-adjusted facilities, where equipment and process control are optimized in a closed loop and product quality can be guaranteed as designed with minimal raw material and energy waste.”
Continued timing improvements will be key.
“[Customers will want to] improve equipment operating efficiency (EOE), the measure of ‘run’ time compared to ‘total time available,’” said Henry. “In the competitive world of pet food extrusion and co-manufacturing, there are substantial costs that are true across the board (raw materials, labor, equipment). Being able to leverage your facility efficiency as a competitive edge is crucial.”
Those equipment suppliers who want to succeed in the space will need to ensure their products’ adaptability.
“The future in pet food manufacturing will require equipment that is flexible and capable of adapting to various changes while producing a quality product with the required nutrition and palatability, within the required density range,” said Delamazure.
Balancing legacy equipment with optimization needs