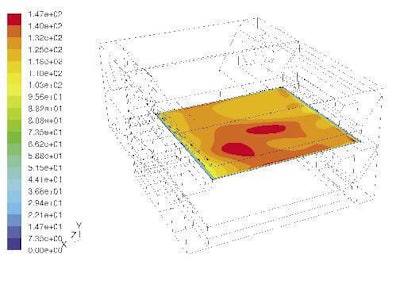
Petfood companies have worked hard in recent years to shed costs and maximize productivity. "However, oftentimes in our industry," notes Wenger Manufacturing's Robert Sunderland, "we find most of the attention focused on the extrusion cost center. Other cost centers tend to be overlooked until plant capacity is reduced."
"Most petfood producers are well aware of the energy cost for their drying operation," says Aeroglide's Dan Poirier. "However, too many producers do not track the costs of overdrying or downtime."
Overdrying due to non-uniform drying. "A well-designed, well-adjusted petfood dryer," says Poirier, "should be able to dry your product to within ±0.75% or better. Suppose that your extruded petfood cannot contain over 10% moisture. If the product coming out of your dryer has a moisture variation of ±3%, you must dry your product to 7% moisture on average to ensure that no product is over the specified 10% moisture limit. The result is a 3% loss in production. If your petfood line is producing 75,000 tons per year, a 3% loss in production from this line represents 2,250 tons per year of lost production. At US$600 per ton, that adds up to US$1.35 million."
Downtime for maintenance and sanitation. "A dryer producing 10 tons per hour of extruded petfood can be producing well over US$100,000 worth of product each day," explains Poirier. "If you're spending even three hours a week of unplanned maintenance or cleaning downtime, you have lost 30 tons of final product per week, which equates to US$650,000 per year of lost production."
Many producers can significantly reduce their drying costs and increase their production rates by taking a closer look at their drying operation.
New technology
Efforts to maximize productivity often require employing new technology. A good example is the use of computational fluid dynamics (CFD) to improve dryer engineering and performance.
Sunderland told Petfood Industry: "CFD provides detailed information on airflow velocity (speed and direction), particle distribution (for fines), temperature and pressure."
Wenger engineers decided to use CFD to gain a more scientific understanding of how its dryer worked. Fluent Inc., a leading vendor of CFD software, assisted in the efforts. Wenger is now using its new understanding of CFD to make better use of the current dryer design and streamline the process of developing the next generation. CFD offers the potential to improve dryer design by allowing engineers to quickly evaluate alternate configurations and get a much better understanding of why a particular configuration performs the way it does.
The results of the simulation, which were displayed in a graphical format, revealed far more information about the dryer's operation than had previously been available. By viewing graphical depictions, Wenger engineers gained a much deeper understanding of how the existing design worked (see figure, left).
In particular, the airflow path lines in the settling chamber revealed strong swirling flows that helped explain why the Wenger design was so effective in removing fines from the air streams. The engineers were also able to quantify the flow distribution over the product beds, which helped explain the consistent performance provided by the original design (see figure, right).
More on energy efficiency
When asked his thoughts about state-of-the-art drying technology, Sander Geelen of Geelen Counterflow replied, "With the current cost of oil, energy costs are a major concern. There is no single process in your plant that uses more energy than the dryer does. For that reason alone, the dryer is a prime target for any efforts to reduce the energy bill. The good news is that large gains are usually possible when you focus on the dryer. The large majority of dryers older than five years are unlikely to have maximum energy efficiencymostly because they are based on the wrong principles."
Geelen believes that drying technology has improved so much that only the latest generation of vertical dryers are optimally efficient. He thinks if you replace a dryer more than 15 years old with the latest technology, you likely will be able to reduce energy consumption by 50%. The investments involved can be significant, he notes, but the savings usually provide a payback time of two years or less. When you take into account the savings, thanks to reduced maintenance, higher moisture uniformity and less cross contamination, the payback time is even better.
"In general, you can say that any extruded petfood process that consumes more than 2,500 kJ/kg of evaporated water is not efficient enough," contends Geelen. "Energy injected into the product by the hammer mills, conditioners and extruders can and should be recovered by passing the cooler exhaust air into the dryer. If that is properly done, the risk of polluting the dryer is controllable. In any case, the increased cleaning frequency that it may cause is easily recovered by the energy savings."
Geelen states that any dryer exhausting air above 60°C is usually wasting energy. "In practice only counterflow dryers can achieve this number without adding expensive energy recovery systems for the air exhaust. If the dryer is designed and operated for optimum efficiency, there is hardly anything that can be recovered. The air that is exhausted from a counterflow dryer will be close to the condensation point, which means the drying air has been used to maximum advantage.
"In short, there are many tricks for improving an old dryer, but the results will always be a compromise. Investing in a modern dryer is the best way to go. Adding up all pros, the payback times become very interesting."