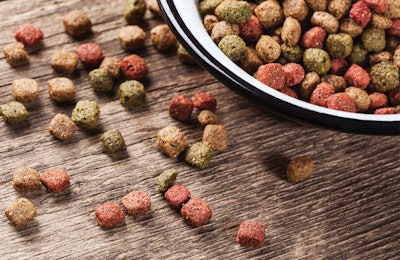
Extruder suppliers who make the equipment that keeps the pet food industry in production has more than ever to pay attention to in terms of trends and client needs. “Many pet food manufacturers continuously produce mass quantities of products on strict deadlines,” said representatives at Ever Extruder. “The production of these pet foods needs to be fast, clean and accurate. Manufacturers need the ability and flexibility to effectively run a wide range of products on a production system without having to perform equipment configuration changes or sacrifice production speed and output.”
And it’s no secret that the pet food industry is rapidly diversifying. Specialty formulas are at their peak, consumers are looking for innovation, and those who make pet food need the tools to stay on top of ever-shifting market needs. “Pet food producers continue to use their creativity to push the envelope on the types of ingredients used and in final product appearance and performance,” said Dennis Funk, vice president of Wenger Manufacturing Inc.’s companion animal division. “Many of these trends are not only dramatically different from each other, but are actually polar opposite approaches.”
Current pet food trends in focus
“The addition of functional pet food ingredients is one of the biggest pet food trends,” said Urs Wuest, director of product management of pet food and aqua feed for Bühler AG Nutrition. “And interest in high-meat [formulation] is driving research and innovation as consumers seek nutritional pet food with higher levels of protein.” Bühler is working with customers to find new ways to incorporate high levels of protein into their products and manage water content, according to Wuest. The research is helping pet food processors learn what can be accomplished using existing processing lines and what accessories may be required for meat handling and additions.
Hygienically designed dryers from Bühler Aeroglide give operators complete access with easy-to-clean materials and tool-less connections that help to reduce overall cleaning downtime, according to the company. | Courtesy Bühler Aeroglide
“The companion animal food trends that have garnered a majority of our focus have been fairly consistent for the last two to three years — fresh meat inclusion, limited ingredient diets, grain-free, organic, ketogenic and other niche genres,” said Will Henry, research and development with Extru-Tech Inc. The company’s more recent experiences have been to improve upon those genres by increasing overall proteins levels, increasing animal protein contributions, and improving the manufacturing environment via an economical processing profile and a more secure food safety system.
“High level of meat definitely continues to be a major topic, perhaps to the point of growing past the ‘niche market’ stage and into mainstream acceptance,” said Funk. “The ‘no grain’ segment is also still trending up and is followed by other trends showing strong developments into recipes with low carbohydrates, non-meat proteins and even processes utilizing extrusion systems to make ‘baked style’ products.” Wenger, he said, is attempting to stay one step ahead of pet food manufacturers’ dreams, with the goal of having innovations ready for industrial use at the exact time the market swings towards a new trend. “Our engineering and process experts continue to design and test new evolutions of extrusion equipment right here in our own technical center,” said Funk. Advancements in high-intensity preconditioning, thermal extrusion, dual stage drying, extruded-baked production and full line automation systems complete with on-line product analyses are just some of Wenger’s recent developments.
Food safety and production flexibility
Two things that continue to be vital in extrusion innovation are food safety improvements and the flexibility to follow trends, and the industry is determined to stay on top of both.
“The pet food industry must have the same equipment design requirements as the food industry,” said Steve Blackowiak, director of food safety, research and development at Bühler Aeroglide. “A heightened food safety focus is driving changes in pet food equipment design and supply, with attention to features that minimize contamination risks with high-hygiene dry clean processing solutions that will reduce downtime for cleaning.” At Bühler Aeroglide, construction materials and manufacturing processes are being improved to lower the risk of contamination, from an open channel frame structure that eliminates tubes to more hygienic welding technologies that reduce growth areas for contaminants. Dozens of design elements such as tool-less connections and hygienic door latches will reduce cleaning downtime and significantly increase the effectiveness and ease of cleaning, said Blackowiak.
Ever Extruder has also recently focused on meeting these needs. “The Ever Extruder sanitary start-up discharge system with flow-control valve provides the flexibility that manufacturers need to improve cook and density control in high-meat product, reduce scrap, improve sanitation control and improve overall product quality,” said the company. The system allows high-meat product to meet cook requirements, and the flow control valve design allows for precise adjustment to be made while the system is running. The result, according to the company, is flexibility to control through-put and restriction of the product before reaching the die, while adding shear and density control. It also features improved sanitation control, specifically keeping product that hasn’t reached necessary temperature away from the die and take-away system.
The Ever Extruder clean cut hub and cutting system offers a self-tensioning hub and one-piece cutter assembly for many sizes and brands of extruders. Operators have the ability to control cutting speeds to match products being made, which minimizes product clumping and product deformation issues, according to the company. | Courtesy Ever Extruder
"We continue to see a push from the industry to further mitigate their risks in terms of food safety,” said Henry. “The industry, for some time now, is no longer in the ‘wait and see’ mode. They are eager to learn how they can better secure their clients and produce a safe quality food for the companion animals.” The primary innovation that has assisted Extru-Tech in the development of new products suiting current trends is an open-idea approach to the processing scheme. “We learned quickly that the traditional ‘dry-expanded kibble’ approach would not allow our client base to maximize the performance of the traditional single screw extrusion architecture,” said Henry. “Further, the continuing research and innovations with our food safety systems and the ETI quick clean 3-pass dryer system have all been instrumental in meeting these ever-growing challenges of the industry.”
Looking towards 2017
Continued research is one prime target in 2017. “Bühler is researching what can be accomplished with existing extruder machinery and processing solutions with regard to fresh meat and freshly prepared meat,” said Wuest. “The latest findings have identified a base line for moisture set points. We know the maximum moisture that can be handled in a processing line determines the maximum meat addition possible. Bühler is assessing existing lines and determining what kinds of accessories are needed for meat handling and additions.”
Bühler’s twin-screw extruders ensure safe, reliable production of high-quality pet food, with gentle processing that is both efficient and economical, according to the company. | Courtesy Bühler Aeroglide
Whatever else is on their dockets, extrusion experts all agree that flexibility will be vital for the pet food industry success going forward. “Flexibility is our key focus for 2017,” said Funk. “We see this as an absolute necessity for our industrial partners, as the pet food market trends continue to expand exponentially. The days of dedicating a processing line to one specific product type are a relic of the past. Producers need to have the flexibility to make wide ranges of products on the same line, or they risk missing out on lucrative trends. Wenger’s belief is that the more flexible a pet food manufacture can be, the more secure and productive they will be. Our solutions allow for this flexibility, and we intend to continue to build on this approach in the coming year.”