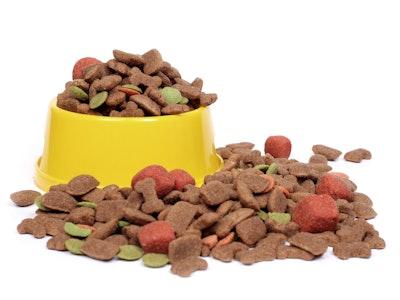
Food safety and security have become big driving forces in food manufacturing, whether for humans or pets. ERP integration solutions can help address these issues by tracking essential information about inputs: when materials arrive at a plant, where they came from, how they are used, and more. This data makes it easier to prevent safety issues before they arise.
Attempts have been made to create one-size-fits-all ERP integration solutions for food production. But every plant is different, as are the materials they bring in and the formulas they use. Such cookie-cutter solutions often fail to meet each manufacturer’s needs. The manufacturer may have to run multiple types of software and interfaces in different parts of the plant, leading to inconsistencies in tracking and reporting. Or the manufacturer might change its desired process to match the limitations of an off-the-shelf system.
Neither of these outcomes is optimal when designing with food safety in mind.
The Benefits of Schenck Process Custom Integrations
That’s why Schenck Process dedicates its expertise to creating only custom ERP integration solutions. “A lot of integrators often have a rubberstamp solution, where our solutions are made to fit customers’ needs,” says Dan Schuster, senior project engineer with the process controls group at Schenck Process. “Because it’s a custom solution, you don’t have to compromise on the data that you want to pass back and forth across the floor and between the floor and the office. And we can accommodate specific requirements that are unique to the customer.”
This customization doesn’t end with the design phase. “What really differentiates us is that we work closely with the customer over the long term,” says David Hammes, senior process control engineer with Schenck Process. “As the process goes along, we continue to refine and modify what we're doing. If the customer develops new needs, we continue to work with them and do whatever is necessary to get what they want. We work with them as though they’re part of our family.”
Custom Integrations at Work
In a recent project for a new pet food production facility, Schenck developed ERP system integrations to track materials throughout the plant. These integrations employ the same user interface across the plant and different brands of equipment. This consistent interface has several advantages:
- Users do not need to be trained to a new interface if they move to a different part of the floor.
- Information gathered is consistent across the plant, regardless of the type of material used. This allows uniform integration of the information into the ERP.
- Maintenance of and updates to interface software are uniform across the plant, preventing a hodgepodge of solutions that need to be deployed separately.
At the new pet food facility, Schenck Process supplied barcode scanners at all introduction points that integrate with the ERP system. These integrations verify incoming material, report how long it has been in storage and transit, check for any recalls the supplier may have put out while it was in transit, and confirm where the material should be stored. The material gets scanned every step of the way from storage to production, so any new recalls or other concerns can be detected immediately—before the material enters production.
Built-in reporting tools allow the office to see exactly where that material is—whether it's in the warehouse or a tank or has entered production—as well as the exact amount of each material that goes into production, its source, and what time it entered production. The tools also let the office know when to order more material or when to notify fork trucks to move material within the plant.
Another integration enables the office to push recipe schedules directly to the plant floor. The integration helps automate the process of pulling down ingredients in the correct type and weight, with handshakes in place that ensure the operator runs the formula exactly as specified. This helps streamline the manufacturing process and ensure consistent quality.
“We work closely with the customer to meet their food safety and security needs,” says Hammes.
Schuster agrees. “Ultimately, each customer is going to have a different game plan. The overarching goal of food safety is the same.