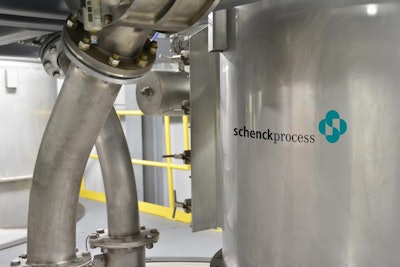
Schenck Process started out in the late 1800s by producing weighing equipment that allowed manufacturers to accurately measure production materials. From those early beginnings the company has grown and expanded its product offerings to cover multiple aspects of a manufacturing operation. Today, it helps companies by designing the best possible production process—from inputs to distribution.
“We are a design engineering company that makes some of our own equipment, and our whole tagline of ‘we make processes work’ embodies that,” says Matt Craig, Global Director of Food and Pet Food at Schenck Process. “We’ll come in and design the overall process for our clients from the ground up. We take on the overall responsibility of putting the entire manufacturing process together—design engineering, specifying and supplying equipment by providing a proposal that will meet our clients’ needs. We do this by listening to their plans and applying our knowledge of material handling, weighing and feeding processes, dust collection, and process controls to deliver a holistic solution for our customers. We will also add in multiple process steps—milling, mixing, extrusion, drying—to deliver the best possible solution for their facility.”
Pet Food Expertise
Schenck Process brings a particular expertise to pet food, with collective industry experience that goes back decades. Its team members “have made and handled pet food ingredients in-process and finished pet food inputs, and finished kibble,” Craig explains. “They understand the unique challenges facing pet food producers today, from high meat to grain free. Our team understands the nuances of getting meat meals to properly flow out of bulk bins or tote bags, or how the orientation of an airlock can cause kibble shearing in a continuous dense phase system, causing degradation and poor product quaility. The ‘tribal knowledge’ base of our sales team and project management group is second to none in the world when it comes to handling petfood inputs and processed kibble.”
That depth of expertise has led to high customer satisfaction, reflected in a five-year global compound annual growth rate of more than twenty percent in the pet food sector. Over the past 25 years, eighty percent of customers hiring Schenck Process for complete project management and execution have returned to it for subsequent projects.
A Better Design
One such customer first worked with Schenck Process in 2014, after it asked for bids on supplying equipment for a pet food manufacturing facility in North America. When the Schenck Process team reviewed the specifications in the request for proposals, it identified several problems with the planned facility design. The team approached the customer with a new design that would take into account the unique attributes of the pet food ingredients and procedures this client wanted to apply.
Impressed with Schenck Process’s applied knowledge of the ingredients and finished targets, as well as by its attention to detail, the customer accepted the new proposal. In the final scope of work, Schenck Process delivered a complete plant process, including:
- 30 bulk silos, a dozen bulk bag unloaders
- loss in weight-feeding of micro-ingredients
- fresh meat processing equipment and liquid systems for delivering 77 different ingredients to a batch mixing/milling structure, which was also designed and supplied by Schenck Process
- handling of kibble during and after extrusion
- delivery of the finished product up to storage and out to packaging
- Complete process controls for the plant’s three processing lines
- ERP integration of the entire process
- ingredient lot number tracking
- Overall batch-control system
- 12 human-machine interfaces
- 14 input-output panels
- 19 scales
- 15 barcode scanners
The customer was so happy with the final results that, just two years later, it contracted with Schenck Process to provide a detailed design for a second complete factory.
“The money is made at the extruder—everybody knows that in pet food,” Craig says. “But if you can’t get mash to that extruder in the right blend at the right time, deliver coatings at the right rate, or gently take kibble from your finished product bins out to your packaging line, you’re not making any money. And that’s where Schenck Process comes in. We make processes work.”