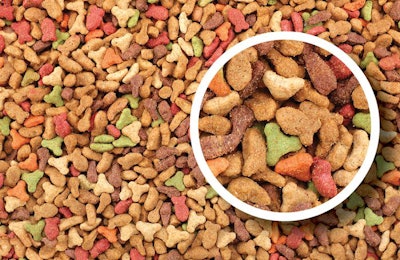
EDITOR’S NOTE: Registration is currently open for Petfood Essentials CONNECT•ED, an on-demand online learning short course offered by Petfood Industry in conjunction with September's Petfood Forum CONNECT. This program is intended to provide detailed information about the technology and processes involved in production of dry expanded (kibble) pet food. Content experts will lead participants through essential steps along the path toward a better understanding of and appreciation for the process involved with producing these pet foods.
For those not familiar with pet food production or the industry in general, a special series of articles, of which this piece is the third, is intended to provide a high-level, elementary overview of what will be learned in much greater depth during the virtual sessions. The first piece discussed ingredients and preconditioning; the second piece discussed extrusion and drying.
In the previous articles describing production of extruded pet foods, we have taken a generalized overview of the ingredient handling, preconditioning, extrusion and drying processes. The food has been converted from a combination of raw agricultural commodities into a fully formed kibble that looks and feels much like the final product found in the market. While one might consider the process complete at this stage, there are two “finishing” steps remaining — topical coating and packaging.
The finishing touches
Some critics argue that “coating” the kibble with fat and flavors is not necessary and may lead to obesity and other issues with the food. However, this process provides a vehicle to portion the fat onto the kibble in a way that does not disrupt the friction required for cooking in the extruder and provides more of the appetite drivers for intake (fat for dogs and protein flavors for cats) to the surface where they will interact more directly than if internalized. Further, being able to add coatings to the surface assures a more consistent flavor profile from batch to batch and replaces some of the flavor components that get locked away deep in the kibble interior.
Coating the final product
Once the kibble exits the cooler, it will be sent to a coating line where the external ingredients are added. There are various kinds of equipment used for this depending on the type of engineering and footprint the manufacturing plant has available. The details are important regarding the machinery involved and quantity of liquid and dry ingredients that need to be coated onto the kibble. The addition of fat is affected by type (saturated or polyunsaturated) and amount.
Ruminant (e.g., beef and lamb tallow) and pork (e.g., lard and choice white grease) fats are solid or nearly so at room temperature and must be heated to liquify and then pump/spray. So too, poultry fats (chicken and turkey) are semi-solid to semi-liquid at room temperature and require some amount of heating to move effectively through the pipes toward the coating system. However, fish oils and vegetable fats are all liquid at room temperature and do not require heating beyond what is beneficial for their absorption into the kibble.
These are typically sprayed or dripped onto the kibble as it is moved within a rotating drum or falling-curtain system. In some cases, a liquid digest flavor may be applied simultaneously with the liquified fat. A dry, powdered flavor is typically added just after the liquid fat which helps it stick to the kibble.
Considerations for fat application can be the amount. Too little (<2% topical) and the final product can appear “two-toned;” too much and the excess will not soak up into the pores of the kibble, will appear greasy and will leach into the packaging. For those wanting a high volume of external fat, a technique that is more common in Europe is vacuum coating that draws the liquid into the core of the kibble. This is very much a batch-style of application rather than the more continuous tumble drum or falling curtain systems. One other factor that influences the external fat application is the porosity of the kibble — this can be controlled or affected by the upstream extrusion expansion process.
[fancy-dog/cat-eating-kibble]
Coating and packaging are two of the final steps to kibble production before the “brown-and-round” food hits a pet’s bowl. | TBD
Packaging considerations
From coating, the kibble is conveyed to bulk storage bins and readied for packaging. There are a variety of packaging systems, from simple bag filling stations to form-fill-and-seal systems. Not to short-change this critical step in the process, but today there are about as many package types as there are products in the market. As a process, the size of the package, the material used and the filling (charge) equipment are important considerations. This is an area of practical challenges and dramatic impact with the consumer (pet owner) as this is where they interface with the product both visually and physically. It is also an area in which pet food companies invest huge sums for the equipment.
Some common aspects of various packaging systems include the overhead storage, scale system, clamps to hold the package in place during filling, weighment, seaming or sealing, transport to secondary packaging or palletizing, and metal, dud or seam detection system. Of course, most packaging systems also have quality check stations to assure that all that is intended to be packed has been done so properly.
Packaging is also responsible for making sure the final product gets from the factory, through transport and distribution, onto retail shelves and into the home without any loss to its integrity. At the latter end, it may also be responsible for providing barriers to oxidation and moisture migration which can affect palatability and nutritional composition. Finally, the artwork and information on the package are under scrutiny from regulators and become the visual interface with the consumer. The package conveys the product intent and its composition, and provides instruction for proper use. Without effective packaging, all the steps before are for naught.
Getting the final product to market
At the end of the process when all is produced and packaged, final quality evaluations and safety checks must be conducted and passed. In some cases, the product must be validated for its delivery of the final nutritional composition and utility to the animal. Various quality checks for proximate composition, bulk density, kibble dimension and color, and microbial safety must be made before it can be released.
Most pet food companies today will hold product upon sampling until a third-party laboratory verifies that the food has tested negative for Salmonella. There may also be a series of tests conducted to validate palatability, stool quality and digestibility, and even longer-term feeding protocols to verify that it is safe and effective for the intended animal and life stage. Follow-up validation may also be performed as the product matures in the market.
The process of making standard “brown-and-round” kibble is somewhat taken for granted. While today’s pet food companies produce millions of pounds annually in this manner, each consumer and their pet are precious. Understanding the process in detail is vital to successfully meeting their needs and adapting to the changes that are occurring with ingredients, engineering and distribution — all to assure that pets in our homes are well cared for and consumer confidence remains high.
Click for more information and to register for Petfood Essentials CONNECT•ED