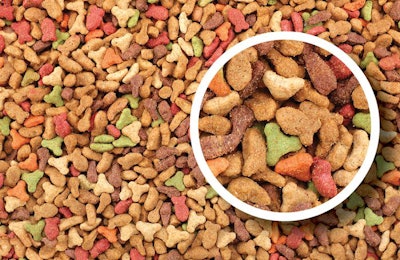
EDITOR’S NOTE: In the next few weeks, registration will open for Petfood Essentials CONNECT•ED, an on-demand online learning short course offered by Petfood Industry in conjunction with Petfood Forum CONNECT. This program is intended to provide detailed information about the technology and processes involved in production of dry expanded (kibble) pet food. Content experts will lead participants through essential steps along the path toward a better understanding of and appreciation for the process involved with producing these pet foods.
For those not familiar with pet food production or the industry in general, a special series of articles, of which this piece is the first, is intended to provide a high-level, elementary overview of what will be learned in much greater depth during the virtual sessions.
Production of quality dry expanded pet food is no easy feat. We have been producing this type of food, often described as kibbles or croquettes, for nearly 70 years and it constitutes nearly 70% of the pet food market. The production process requires synchronization among many assembly steps, all key to producing a consistent, quality product. The wishes of the consumers, regulators and critics are many and the coordination of all these demands present numerous challenges. In short, this is a complicated process.
In this first article, an overview of the raw material preparation will be provided along with some highlights of where we must pay special attention.
The beginning: ingredient preparation
Quality ingredient choices and preparation are essential to producing a superior pet food product. | Andrea Gantz | WATT Global Media
It all starts with consistent, quality ingredients. Many of the pet food battles today are being fought along the ingredient choice line. What the market may not understand is that not all ingredients are the same when it comes to handling and processing. Grains differ from legumes and tubers, protein meals differ greatly from raw meat, fibers differ in how they absorb moisture, and fats can exert a negative effect on the process.
At the beginning of the process, the ingredients selected are defined by the marketing organization to match what they think consumers will want or reject. The formulator puts it all together — on paper — with an eye toward nutrition and regulatory compliance. Then, it is up to the production side of the organization to make it happen. The total formula is parted-out into its components: dry ingredients, meats (if they are included) and topical coatings. These are handled separately through the various unit operations within the manufacturing process.
Procurement sources the ingredients, hopefully to specifications. They arrive in their various forms — whole, pellets, granules, powders, liquids, etc. — and are conveyed to the appropriate storage bin or vessel. From here, they must be converted into the appropriate particle size or consistency. For whole grains and pelleted ingredients this may include grinding, and for frozen blocks of raw meats it may be tempering, block-breaking, grinding and mixing with water to create a slurry to make it pumpable. For bagged premixes and other powdered ingredients, it may simply be placement in the appropriate bin.
Typically, the dry ingredients are weighed per the formula, heaviest to lightest, into a hopper. Some companies may have sub-assemblies upstream in the process for major, minor and micro ingredients. This assures that a consistent dry blend is created. The standard mixer for dry ingredients is a double-ribbon mixer where they are blended for a period of three to five minutes. From here, they drop to a hopper for conveyance either to a final grinding step or to the overhead bins above the preconditioner and extruder.
A great deal of importance is associated with this weighment, mixing and conveyance as it sits at the center of where the extrusion process starts. This is a great source of liability should something go wrong as the dry blend constitutes roughly 70–90% of the formula.
Preconditioning and working with blends
Dry blended pet food ingredients must first be conditioned before transfer to the extruder. This is done in a preconditioner such as this one, the Preconditioner+ from Clextral. | Courtesy Clextral
In extruded pet foods, the dry blended ingredients (ration) must first be “conditioned” before transfer into the extruder. This apparatus is commonly described as a preconditioner and is responsible for the initial heating and moisture addition and subsequent mixing of these elements with the ration. This begins the cooking process of the starches (gelatinization) which is important in the conversion of the starch from a tightly packed granule to a less ordered structure. This unpacking of the starch granule takes some time and happens in the preconditioner.
Additionally, the preconditioner is where some operations will add meat slurries and fats. They should be added toward the middle to end of the conditioning steps lest we coat the starch granules and diminish the ability of the heat and water to penetrate the starch. Mixing large proportions of meat slurry which is high in moisture and fat is no easy matter. It requires metering of the slurry at the perfect rate relative to the dry ration and a great deal of energy and shear to assure a consistent blend.
If you have ever tried to blend butter into biscuit dough, you will quickly realize the potential for creating clumps. If the slurry is not properly mixed at this preconditioning step it has detrimental effects later in the extrusion process leading to surging and inconsistent piece density, the net effect of which are drying challenges and mold growth. Finally, some companies use the preconditioner for product pasteurization — the validated “kill step” for pathogens. The temperature at the end of the preconditioner should reach approximately 80°C for 30 seconds to assure a near-complete knock down of organisms and provide compliance with the Food Safety Modernization Act (FSMA).
The preparation of the ingredients — types, grind size, weighment, mixing and pre-conditioning — are vital to successful extrusion, drying and product consistency. If this process is captured properly it can assure nutritional quality, proper expansion and bulk density, a smooth consistent appearance, and optimal nutrient utilization. To short cut this step can lead to heartache, frustration and poor-quality products. The proof, as they say, is in the pudding.