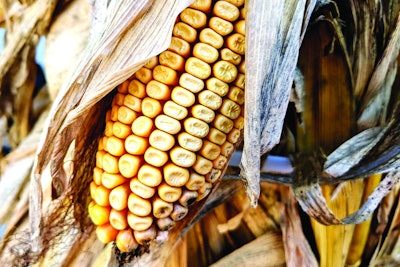
Safety and technology are two essential topics for the pet food industry.
On Thursday, September 23, speakers touched on these topics in a roundup session at Petfood Forum in Kansas City.
Mitigating the risks of unconventional and novel proteins ingredients to ensure safe pet food
Ray Mutulka, director of toxicology at Burdock Group Consultants shared questions to answer to characterize the ingredient and mitigate potential risks when bringing novel protein ingredients into the market.
- What’s the source?
- What are any modifications/chemical changes being made to the ingredient?
- What is the manufacturing process? Is there safe use of technical additives?
- Do you have a complete understanding/analysis of the whole ingredient, not just the “active” ingredient?
- What are the specifications of the new ingredient? Are they reproducible and “define” the ingredient?
- Have you conducted a stability analysis?
Protecting your consumers: Mycotoxin best practices
Tracie Sheehan of Merieux NutriSciences began her presentation talking about Midwestern Pet Food’s dog food recall due to aflatoxin that took place in December 2020 and January 2021. The recall had to be expanded from six products and 9 lot codes to 19 additional products and more than 1,000 lot codes. By Jan. 26, 2021, more than 110 pets had died and more than 210 pets became ill after eating the pet food.
Mycotoxins occur in most cereal commodities, which are also common ingredients in dry pet foods. More than 86% of current recalls are due to aflatoxins, which are from molds typically found in corn, nuts, cottonseed, rice, spices and coffee. They can cause severe liver damage, death and are carcinogenic. Dogs and cats poisoned with aflatoxin show loss of appetite, listlessness and vomiting. Most of the recalls are happening in Turkey, the United States and China.
What can companies do to prevent aflatoxins?
- Post-harvest aflatoxin preventive controls:
- Density-based and size separation
- Dehulling and polishing
- Thermal treatment
- High hydrostatic pressure
- Electronic optical sorting equipment
- Radiation (UV, gamma)
- Pulsed light or electric field
- Non-thermal plasma
- Electrolyzed water
- Chemical treatment
Among the things the FDA doing to help prevent mycotoxins are conducting unannounced inspections, personnel training, recommending inspection standard operating procedures and documentation and testing of ingredients.
Industry 4.0 and smart data: Improving your pet food plant’s performance using big data
Pete Ensch of WEM Automation wanted attendees to imagine their pet food plant is a smart factory, with everything interconnected.
Ensch said the pet food industry is entering Industry 4.0, the fourth industrial revolution. Industry 4.0 focuses on the Internet of Things, the computerization of manufacturing, using technologies in all levels of the plant and connecting humans with the machines.
Plant owners can gather data from raw material receiving through the manufacturing process, all the way to their ERP system to drive operational excellence. Ensch said owners can then make data-based decisions that directly impact safety, quality, productivity and cost.
“Industry 4.0 is utilizing various technologies at all levels of the plant and integrating the systems into a production plant control, thereby, creating a smart factory which seamlessly interconnects mechanical sensors, electronics, software and humans,” Ensch said.
Ensch said information is only one part of the story; it must drive actions that directly impact productivity, efficiency and profitability. Regardless of the function, having the right types of information immediately available to drive educated decisions is key.
Ensch said pet food facilities have unique challenges:
- Number of, and variation of ingredients
- Number of, and complexity of formulations
- Automation and central control systems are not as prevalent in pet food facilities
- Traceability to satisfy regulatory and consumer demand for transparency of where their pet’s food comes from
Having a smart factory can provide solutions to all these challenges, at the stages of receiving, grinding, batching, extrusion, drying and cooling, warehouse and traceability.
Ensch said there are six steps for implementation of the Internet of Things:
- Develop a plan
- Pick the right team
- Be honest about the people side of change
- Select the best technology that fits your business
- Deploy and implement
- Follow-up, follow-up and more follow-up