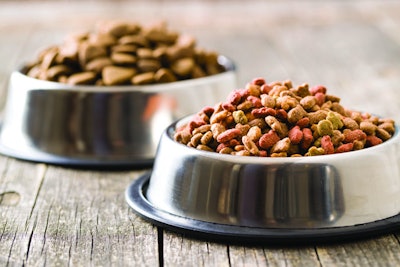
Drying extruded kibble tends to be one of the more energy-intensive aspects of making dog, cat and other pet foods. However, machine designers and operators can optimize their equipment for energy efficiency and environmental sustainability.
“In any process, the dryer is going to be your largest consumer of utilities, by default,” Will Henry, director of research and development for Extru-Tech, said during the Q&A of a presentation at Petfood Essentials. “That's something that you cannot remove because, every product has a specific requirement of moisture to achieve the processing marketability and food safety… There's always nuances that can improve that efficiency and make it a more green operation. It can lead to substantial savings.”
To do that, knowledge of process characteristics and limitations for a specific product allow designers and operators to adjust dryers’ configurations to reduce energy usage, Michel Pereira, Andritz Group global application manager and dryer specialist, told Petfood Industry.
The basic factors controlling the drying process are:
- air conditions,
- airflow,
- retention time,
- spreading and
- product physical and chemical characteristics, he said.
Before constructing the dryer, Andritz studies the reference kibbles to develop the drying curves which are considered in the equipment sizing and design, he said.
These various factors in pet food drying can be manipulated to increase energy efficiency. Economically and environmentally sustainable dryer design and operation isn’t simply a matter of reducing electricity or gas usage. Different aspects of the drying process can be manipulated to increase efficiency.
Reducing energy usage benefits a pet food manufacturer’s finances while decreasing environmental repercussions. However, few pet food producers consider energy efficiency in exactly the same terms, Robert Sunderland, dryer technology director for Wenger, told Petfood Industry.
“Less energy to one client may be defined as less wasted product or more precise moisture control,” he said. “To another, it may mean an operation that consumes less thermal energy (gas) with higher mechanical energy (electric). Advanced dryer automation controls are the most direct and cost-effective way to ensure the entire process system is being run at optimal efficiency.”
Reducing energy use by existing pet food dryers
Energy efficiency doesn’t have to involve designing a system from the ground up. Pet food production facilities can adapt or retrofit existing equipment to meet economic and sustainability goals. Sunderland said this can include updated, more efficient heaters, along with product in-feeders or process fans and product conveyors.
Replacing old, worn or dirty bedplates for new ones with more open areas increases process airflow, boosting energy efficiency, Pereira said.
“Some dryers equipped with a mechanical distributor can be upgraded with the servo motor distributor,” he said. “A humidity probe could be installed at the exhaust ductwork to control the exhaust air volume under any weather conditions. It is recommendable to train operational people in the basics of psychrometry, drying process and other best practices.”
Psychrometry studies the thermodynamic properties of moist air.
For help in identifying areas for energy efficiency improvement, extruder manufacturers may offer on-site audits, like the WEngerCARE program, that help producers optimize their dryers, Sunderland said.
Other factors influencing pet food drying efficiency
Before an extruded dog, cat or other pet food goes into a dryer, facility operators can take steps to improve the drying of that product.
“Lowering the overall moisture load that the dryers are tasked with removing is obviously the best practice,” Sunderland said. “Lowering the moisture certainly goes deeper than reducing the extruder steam or water injection by a few percentages. Our clients are evaluating the net energy savings of the entire process. An example of this may be fresh meat addition at the process kitchen, which not only produces a superior final product, but does so without the energy of pre-drying this meat meal.”
Communication among the various members of the team working in a pet food facility helps energy efficiency as well.
“Modern production lines have an open line of communication connecting the major processing steps, he said. “The dryer-cooler then makes the needed process adjustments prior to receiving product upstream. This has energy benefits on all runs, but pays large dividends on short production runs allowing operator personnel to concentrate in other areas.”
As pet food facility crews adjust their practices to reduce costs and pollution, designers work to make next-generation machines that will further improve energy efficiency.
“The market searches for higher efficiency, lower energy consumption and ecologically friendly alternatives," Pereira said. “Andritz is investing in the recovery of energy from surrounding equipment or processes that can be used to pre-heat the make-up air and reduce the energy consumption in the dryer. For example, installing a heat recovery in the exhaust of the kibble´s cooler or recovering energy from a boiler´s chimney hot gases. Alternative energy sources, such as biofuels and electric energy, are also considered.”
As pet owners increasingly consider the ecological and social aspects of the products they purchase, pet food companies also focus on sustainability. Improving pet food dryer energy efficiency may be one way to help the planet and the pocketbook at the same time.