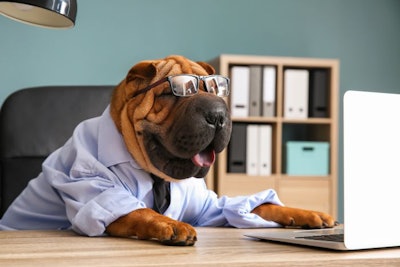
Labor markets remain tight, and pet food processing facilities may need to adjust their management cultures to attract and retain workers. Employees can be hard to find and keep in any industry now. Manufacturing jobs are yet more difficult to fill with the appearance of new options, such as Amazon warehouses and online work. Meanwhile, bonuses lure away even established workers. Dog, cat and other pet food manufacturers face additional challenges, but facilitating communication may help these facilities keep workers and find new ones.
“You can argue that pet food facilities are some of the most difficult food and beverage manufacturing environments to work in,” Osvaldo Granillo, sales director with Redzone Software, said at Petfood Forum 2022 on May 4 in Kansas City, MO, USA. “It's wet, it doesn't always smell the best. It's a very messy environment. There's a lot of wash down happening. So we need to find different ways to engage our people. Because if there's a dry warehouse, such as Amazon doing the same anymore, what incentive does someone have to work in your facility?”
Those incentives need to be strong now. In 2020, business analysts believed the job losses caused by the COVID-19 pandemic would reverse when the disease abated, he said. However, workers fired because of the pandemic haven’t returned to the jobs they lost.
“It's a completely different market,” he said. “The jobs market has been disrupted, with nearly 10,000 Baby Boomers leaving the workforce every single day. Who are they being replaced by? Millennials, Gen Z, generations that value very different things, generations that can make money in different ways, like making more money from home computers. They grew up with technology. It's not just a nice thing to have anymore, it's a must have. And those organizations that are getting out ahead of it and adapting are the ones that are going to win right now.”
“Not only that, but there's a manufacturing image problem,” he said. “Recent manufacturing study showed that only 27% of parents say that manufacturing is an acceptable career for their children to go into.”
Manufacturing plants in all industries are shorthanded. Among 15 companies working with Redzone in 2019, plant managers reported a shortage of four workers on average. In 2022, that number climbed to 34. In 2019, frontline turnover averaged 28%, but climbed to 44% now. The length of frontline worker tenure declined from six years to three years between 2019 and 2022.
To address this shortage of manufacturing workers in future generations, plant managers may need a new philosophy. Granillo believes workers now want jobs with a purpose, not just a paycheck.
People of all generations want to feel that their life’s work has purpose, as Lindsay Beaton, editor of Petfood Industry magazine, pointed out in a question. However, first, they must keep the wolf from the door. People need to make a living wage before they can aspire to altruistic labor.
Once basic physiological and safety needs are met, pet food facility workers move up Maslow’s hierarchy, a hypothetical pyramid of mental fulfillment. In the United States and other prosperous nations, manufacturing employees may desire more from their jobs that the security money brings.
Payment as motivator for pet food plant workers
In RedZone’s survey of pet food plant workers, pay ranked fourteenth on a list of reasons people would stay in their job long term.
“Wage compression is forcing organizations to say, ‘Okay, now that we've hit that threshold, what can keep ticking that number up,” Granillo said.
Now that many facilities are offering US$15 per hour, what will keep an employee coming back to a pet food facility? Beyond payment, workers want to feel that there is a family culture, he said. Facility employees want to know somebody is looking out for them and that their voices travel beyond the shop floor. Beyond themselves, workers want to know that what they're doing is for a greater good. To create that feeling of community and engagement, Granillo recommends developing strong lines of communication among all levels of a facility.
“What a typical communication process will look like in most organizations that we see, a lot of times an operator comes up with a great idea,” he said. “It will make their daily life much easier. They communicate that to a supervisor. It goes to a manager. It goes to someone else. It gets written on paper. ‘Yeah, we'll get to it eventually.’ People forget about it, not because we're bad people, it's just we have one hundred things to do.”
What’s more, many companies lack a framework for that manager to actually do something to implement the worker’s observations.
“So what does that operator do?” Granillo said. “After they give you idea, after idea, after idea to make their lives easier. They're begging you to fix some of these problems, and it doesn't get solved? Well, as you can imagine, they slowly start to become disengaged. They don't give me more ideas. Nobody cares about what I'm saying so why say anything?”
Facilitating communication in pet food facilities
Letting those opportunities for improvement slip by brings an economic toll for companies in the long run. Making a production-line employee’s life easier also tends to make the job itself more efficient and safer, saving time and money for the business. Inverting the pyramid of the leadership structure can help with this, he said. Give the people doing the work a means to improve how that work is done. Technology can form that bridge bringing real-life observations to executives’ attention. Digital communications platforms allow that interchange among levels.
“We need to get the communication platform in the hands of our operators in our team, we need to understand what's in their head, what's important to them, what are some of their top issues,” Granillo said. “As a leadership team, we not only need to provide them with the technology or communications platform for them to understand that, but we need to do something with it.
“Let's say I'm an operator on a line. I've been there for 10 to 15 years. Over me is the VP of ops. I've never once told them anything. I just take orders.
“Well, how would it feel if you have a really good idea? Say, for the past 10 years, I've run into this exact same issue every single day. I communicate that idea within a piece of technology. I create an action to it. Now, the VP of ops accepts that action to say, yes, I will get this taken care of now, right away. You come into work tomorrow, and it is solved."
The dynamic changes for that employee. They are no longer just reacting to orders, but feel empowered to give a few orders themselves. The technology gives them the means to do this.
People that have been very quiet in organizations see one of their ideas come to fruition, then here's another one, there's another one, there's another one, he said. This changes the culture of shop floor ownership, it's no longer just the line that a person comes and works at. This is now their line, and the managers are going to fix it to make their life easier, safer and more efficient. A worker who feels like that keeps coming back, and maybe tells a friend.