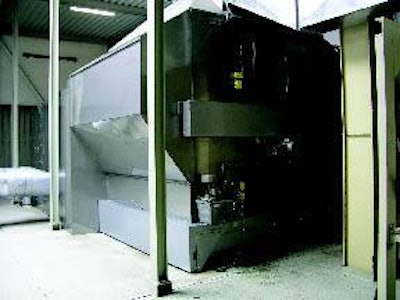
Cost-efficiency and energy-efficiency in particular, combined with high quality production, is an increasingly hot topic for every manufacturing sector. In the case of the petfood industry, a great benefit in this regard can be obtained through optimized use of drying and cooling systems.
Hybrid technology
Geelen Counterflow's president Sander Geelen suggests a remarkable parallel between modern counterflow dryers and hybrid drive cars, which are now very popular because of their superior fuel efficiency. Hybrid cars usually use fuel efficient engines to ensure the highest possible effectiveness when running on gas or diesel. "Our dryers exclusively use the counterflow principle that is scientifically proven to be the most efficient method to exchange energy between any two flows of gasses, liquids or solids," says Geelen. "By applying this principle in our dryers, we can minimize the amount of drying air we need and maximize the amount of energy that can be transferred. This results in a lower air exhaust volume and a lower exhaust air temperature."
Another parallel between hybrid vehicles and counterflow dryers is their energy recovery. When the driver brakes, the mechanical energy is transformed into electrical energy and stored in the batteries that are used to power the electric motor. "In counterflow dryer-coolers we can recover the product heat that is injected by hammermills, conditioners and extruders. That energy is recovered from the cooler in the form of warm air. All of that warm air can be reused as make-up air for the dryer," explains Geelen. "However, it is important to properly design the coater, cooler and air system to make sure the warm air is sufficiently clean when entering the dryer."
Each counterflow dryer from Geelen has internal air recirculation systems that ensure only air with a very high relative humidity passes the exhaust fan, according to the company. For a typical petfood dryer this means that only 25-30% of total drying air is ever exhausted. Counterflow dryers already have over 50% market share in countries such as Japan, France, Spain, Italy, Belgium, the Netherlands and Argentina.
Even the most efficient dryer can waste energy if not controlled properly. According to Geelen, the key is to ensure all of the relevant process variables product flow rate, moisture percentage, air volume, air temperature and drying timecan be precisely measured and controlled in real-time.
Control more than temperature
Operators on the manufacturing line want their dryers to always deliver the exact same moisture percentage for their particular product, independent of variations in raw material or weather. Geelen Counterflow thinks it may have the solution. "In counterflow dryers," the company president explains, "we employ an accurate planar microwave sensor in the dryer hopper, which performs on-line measurement of moisture percentage, product temperature and bulk density." The moisture signal is used to fine-tune the temperature of drying air, so the dryer reacts automatically to any deviation from the set point.
Drying a product helps reduce water activity and thus, increases shelf-life, according to Tom Barber of Aeroglide Corp. (now part of Buhler Inc.). It can also impact palatability, texture and chemical properties of the product, as well as reduce both waste disposal and shipping costs.
Dry, dehumidify or cool
The Rotary Batch Dryer-Dehumidifier-Cooler from Munson Machinery is for direct or indirect drying, dehumidifying or cooling of bulk solid materials. The configurations for direct drying, dehumidifying or cooling are equipped with a material intake chute with ports for introducing heated or cooled air directly into the batch. Configurations for indirect drying, dehumidifying or cooling come with a jacketed vessel that heats or cools the batch indirectly, and are offered with nitrogen-purged systems that eliminate exposure to the atmosphere.
Münch-Edelstahl GmbH also manufactures and designs a machine with multiple functions. Its Carousel Dryer/Cooler has a modular construction design that allows for an increase of capacity after the first installation, and is available at a maximum of 9 sqm of footprint, in different can diameters and with two to 12 decks.
What makes Carousel different from other counterflow drying systems, according to the company, is the cylindrical body. An air stream always flows in a round shape, so that means dryers based on a square bin will always face dead spots in the four corners. Petfood in the corners retains more moisture, while petfood in the center of the machine is over-dried and has less water content.
The round profile of the Carousel allows gentle and uniform drying as the airflow stream needed to evaporate the water content is always based on a round form.