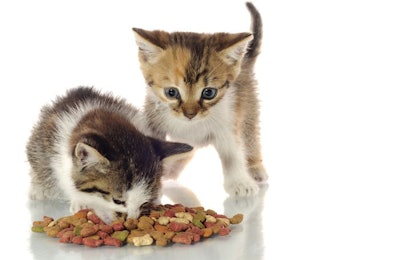
The demands of making pet food have always been complex, but never more so than today. As “unique” diets (such as high meat or grain free) take over production lines, the equipment must be able to keep up with a whole new set of processing demands.
“High-meat, no-grain pet diets really process quite differently than traditional formulas,” said Robert Sunderland, director of dryer technology for Wenger Manufacturing Inc. “This does not seem to be a quick trend — I think it’s the wave of the future. The industry seems to have decoupled itself from commodity-based pricing to very specific recipes, and I think the factories that we supply equipment to are recognizing it or wanting to move into those higher value-added products.”
Adaptive technologies meet the demands of pet food processing
According to the industry, it is no longer enough for dryers to dry and coolers to cool. All equipment must be prepared to do multiple jobs, and do them well, to accommodate today’s pet food formulations.
“The demands for smart and adjustable solutions adding a new layer of versatility and increasing the final product quality are gaining in importance, and are the latest trend in industrial technology development,” said Markus Wied Dethlefsen, senior process engineer, technology and business development for Graintec. “A technological step forward to coolers that not only cool and dryers that are doing more than just drying [is necessary]. Imagine if coolers and dryers know your product that well — not just today, not only one recipe, but can adjust the cooling and drying to provide optimal product handling and ensure the best possible final pet food quality obtainable for every run.”
Optimizing production while meeting the needs of pet food manufacturers is a continuous challenge, but one that the industry has stepped up to meet.
“Process optimization technologies have come quite a long way,” said Nick Manley, marketing communications manager for Bühler Aeroglide. “And with the advent of the Internet of Things, technologies are being developed that allow processors to be able to manage and monitor their connected production lines in real time from any location. They can gain incredible insights into how their equipment is performing, making necessary changes quickly. They can even use data collected in one area to improve operations somewhere else.”
Drying and cooling equipment answer today’s pet food processing questions
Remaining effective while improving efficiency, sustainability and safety is one of the ongoing challenges of pet food processing, and drying and cooling technologies have advanced to provide answers.
“The dryer is typically the single biggest energy consumer in an extrusion line, so any attempt to reduce energy consumption or improve the CO2 footprint of dry pet food plants should start with the dryer,” said Sander Geelen, managing director of Geelen Counterflow. “Early in 2018, Geelen Counterflow will introduce its new generation of electrical dryers to the market. Pilot line testing on extruded pet food during 2016 showed that energy efficiency can be improved by up to 65 percent, to well below 1,000 kJ/ kg of evaporated water, compared to the typical 2700 kJ/kg for a counterflow dryer on natural gas or steam. When the energy for the new electrical dryer is from renewable sources, the CO2 footprint of the drying process can be virtually eliminated.”
Extru-Tech Inc.’s advanced-feature dryers also highlight efficiency and safety, such as tool-free door assemblies and increased dryer bed floor clearance for easier access and inspection; a redesigned chute with span and speed controls for “in-process” adjustments, and reduced horizontal ledges to allow for ease of cleaning. The company has also focused on flexibility in its new designs. “Dryer sections are physically separated to manage airflow through each conveyor independently, even within the same drying section,” said the company. The advanced feature dryers also have reversible solid construction hinged interior doors that can be rearranged for sequential drying and maximum process flexibility, according to the company.
Of course, the equipment must be able to handle increasingly complex pet food formulas, and today’s dryers and coolers must be prepared to tackle high-meat moisture levels and grain-free formulations.
“Obviously, if we’re going to higher-meat recipes, there’s more water load going to the dryer,” said Sunderland. “And meat brings with it not just more moisture, but it’s pretty tightly bound moisture, so it takes a longer time to dry these products. So, we either need to get a larger dryer in that area or, if we did a certain threshold in the meat level (that might be 30 percent or 40 percent meat), we really need to approach it completely differently.
“And this is where [Wenger has] come out with some unique lines of equipment over the last four years really aimed at solving the dilemma of processing off the extruder some of these ultra-high meat recipes,” said Sunderland. “When we get to 50 percent meat, even up to 100% fresh meat, these individual kibbles coming off the extruder are very, very soft. They’re almost like molten chocolate. If we just threw that up on a traditional pneumatic line, it would be a complete mess. So, we’re needing to look at some intermediate steps to dry that product, to set that structure before we then go to a traditional drying step. This has kind of forced us to come out with a whole new line of dryers. For example, a pre-dryer: taking the product off the extruder and drying it initially, virtually in a single layer, at very high temperatures, and setting that product so that later it can go through a traditional pneumatic line to go to a secondary dryer.”
Bühler Aeroglide has also focused on the need for more comprehensive moisture control, introducing an automated closed-loop moisture control system (AeroPro MC) that can be integrated into a pet food production line immediately after the dryer. The system monitors the moisture content of the pet food exiting the dryer and automatically makes any corrections to the dryer, maintaining optimal performance, according to the company.
“Optimizing the drying process and reducing or even eliminating over drying can result in yield gains,” said Manley. “Even small gains of 1 percent can mean hundreds of thousands of dollars in added profitability in a year. Add to that the energy savings realized from a better-performing dryer, and the ROI (return on investment) on such a thing can be very quick. An added benefit of this system is that all that data that gets collected from the dryer (moisture content, temperature, bed depth, etc.) can be uploaded to a secure cloud location and accessed by production managers via any web-connected device, giving them real-time insights into exactly how their process is performing.”
The future of drying and cooling: equipment efficiency vs. product quality
As equipment manufacturers continue to meet the needs of their pet food manufacturing customers, they and their clients alike must walk the balance between cost savings and quality products.
“For years, the energy efficiency of the cooling and drying processes has been of primary focus when producing pet food,” said Dethlefsen. “As energy removal (cooling) and, especially, water evaporation (drying) are very costly operations, it has traditionally been an obvious hot spot to look for savings. And it still will be, as numerous outdated coolers and dryers are to be upgraded in the near future. However, not only details regarding energy consumption should be considered when looking to replace old equipment. There is no interest in drying or cooling the pet food as cheaply as possible if the processes cause damage to the product or lower the food quality.”
At the end of the day, it will take close partnerships between the equipment suppliers and the manufacturers to ensure the end customer is getting exactly what they want for their pets.
“I cannot see that there would be an endpoint in how complicated [formulating pet food] is,” said Sunderland. “Once things get more complicated, they tend to stay that way. As customers become more aware of nutrients, they will want specific diets for their pet, and I think that challenge is going to be pushed back to our customers to produce that, and then hopefully they’ll lean on us and that partner relationship to produce that product.”
WEBINAR on-demand: How to solve extruded LID pet food production challenges