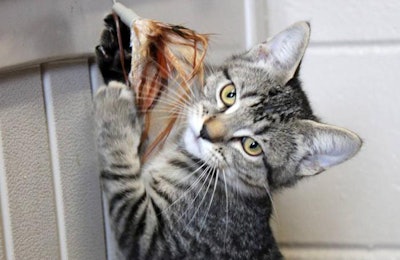
Engineers and technicians explained the inner working of twin-screw extruders, while pet food industry researchers discussed dog and cat food trends and nutrition, at Clextral’s Animal Feed Extrusion Course. Clextral, a pet food and animal feed processing machine manufacturer, hosted the interactive event from October 16 to 18 in Saint-Etienne, France. While Clextral has been hosting extrusion courses in the United States for approximately 15 years, this was their first in France. Although it was the course’s maiden voyage, 38 people representing businesses in 14 countries attended, including Australia, Russia, Romania, England and Saudi Arabia.
“The strong attendance shows a need for higher level education in extrusion,” said Georges Hallary, chief operating officer and vice president, during his opening address.
Animal Feed Extrusion Course content
On the first day of the event, Sothara Sieng, marketing director for Diana Pet Food, discussed various categories of pet food trends, such as natural and health-focused.
Another presentation explored the differences between single-screw and twin-screw extruders. Twin-screw extruders involve multiple processing sections in series, said Sylvie Brunel, Clextral process manager. For these machines, throughput and screw speed are independent. Twin-screw extruders have multiple operating speeds and screw profiles. The machines allow intense mixing with high levels of fat and raw meat.
Single-screw extruders have one processing section. Throughput and speed depend upon each other in these machines. Mixing may be less intense than in a twin-screw extruder, she said, and throughput is wear sensitive.
Twin-screw extruders tend to be more expensive than single-screw machines, Brunel said. However, that extra investment cost may be compensated for by lower operating cost from better productivity and wider range of raw materials, recipes and value added products that can be produced.
The feed extrusion course also involved trips to Clextrals’ facility in Firminy, where participants saw a twin-screw extruder in operation. Engineers explained the various parts of the device, including the preconditioner. Clextral’s Preconditioner+ contains a conveying screw positioned at the bottom of the tank, which helps increase residence time in the preconditioner thereby increasing pre-treatment of the raw material.
About Clextral
Clextral employs 310 people around the planet at four research centers, with 12 subsidiaries and offices. The company has a turnover of EUR61.9 million per year with customers in 95 countries. Food and feed makes up 70 percent of that business. In pet food, their machines are used mostly for treats and superpremium pet food. They are also involved in processing biomass for sustainable energy production, as well as producing pumps for the nuclear power energy.
Clextral was the first manufacturer of twin screw twin screw extruders for food, starting in 1956. While earlier developments focused on making larger, more powerful machines, the company’s engineers now work to create process-oriented machines.
Clextral builds their pet food production systems around twin-screw extruders. Beyond the hardware, Clextral provides its customers with turnkey processing lines that integrate extruders, dryers and ancillary equipment.