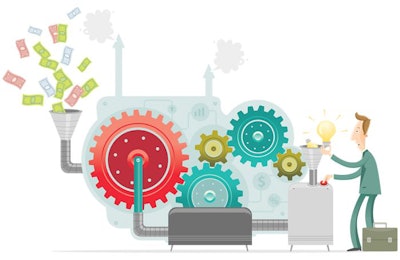
The wide variety of pet foods being formulated these days has meant a lot of changes and challenges for the experts at various steps in the pet food production process. For those dealing with extrusion equipment and processes, maintaining a mastery in their core strengths while becoming flexible enough to adapt to the pet food challenges coming from their customers has been key in remaining successful.
“We are really talking about multiple trends with highly segmented markets — from vegan to BARF [biologically appropriate raw food] — with much smaller production and shorter time to market, all requiring more and more flexibility and agility everywhere, from R&D to production to changeovers,” said Gilles Maller, vice president, sales and international for Clextral, an extrusion technologies and equipment manufacturer based in France.
In particular, according to Galen Rokey, director, process and technology, companion animal division for extrusion equipment manufacturer Wenger Mfg., today’s pet food trends have led to the following challenges during processing:
- Expanded ingredient inventories
- Increased levels of meat inclusion and other slurries
- Raw material availability and variation
- Maintaining product stability and freshness
- Control of food safety hazards
- Rising production costs
- Process complexity and required flexibility
Partnership: The only way to meet today’s pet food extrusion challenges
The customer-provider partnership has always been vital in gaining and maintaining business, but in today’s pet food industry, it’s not just important — it’s mandatory.
“I would say our primary challenge is focus,” said Will Henry, research and development manager for extrusion equipment manufacturer Extru-Tech. “We never want to be cavalier with regards to being able to predict what the consumer/producers are looking for in product. We do our best to be nimble both in providing quality service to our equipment base and in how we drive finished product development for our clients.”
Wenger’s focus has always been on partnership, but according to Rokey the partnerships are more versatile than ever. “The vision, mission and values of Wenger have always been to partner with industry clients to develop hardware and services that allow the pet food manufacturer to meet the processing challenges brought about by current and future trends,” he said. “This brings a focus on continuous improvements and disruptive innovations for the extrusion, drying and related processes in pet food manufacturing. Even the terminology used today is different — pet food is no longer manufactured in a ‘feed plant’, but in a ‘kitchen.'”
For Wenger, part of being successful in providing technologies to the pet food industry is in being able to provide machinery solutions for multiple parts of the pet food production process — solutions like this sanitary dryer. | Photo courtesy Wenger
Working closely with clients now means being prepared to make changes all along the production line, according to Maller. “We work closely with industry marketing experts and our customers to anticipate emerging trends and work upstream to help pet food processors find new solutions,” he said. “Often, this means changes in ingredient specifications and processing parameters. We are developing more ‘clip on’ modules that add specific functionalities as needed to make products that will satisfy the nutritional needs of pets and please their owners.”
Clextral focuses on innovation that can strengthen existing technologies, such as this coextrusion “clip on” module that mixes and injects filling for filled products. | Photo courtesy Clextral
Adapting extrusion technology to meet current pet food trends
As trends expand across various pet food market segments, extruders must be able to keep up if they want to stay in business.
“Several trends have emerged in the pet food industry, which have caused equipment manufacturers to either amend or enhance their technology and educate the market on their abilities to process,” said Sharon Nowak, business development manager for industrial equipment manufacturer Coperion K-Tron USA. Some of those trends, according to Nowak, are:
- Breed-specific formulations: “These formulations require added versatility in both the raw ingredient feeding and material handling to handle a variety of material characteristics as delivered to the extrusion process,” said Nowak. “In addition, versatility in formulations on the extruder technology is required. This results in designs which can be quickly configured to adapt to various production volumes as well as ingredient formulations.”
- Enhanced probiotic addition to pet food formulations: “Probiotics are typically added after the cooking step, which would otherwise kill this beneficial bacteria,” she said. “Probiotics require special handling for both feeding and material transfer so as not to contaminate the probiotics strain.”
- True meat slurries/raw meat additions to extruders: “As the request for high-meat products increases, there is also an increased request in providing higher throughput rates,” said Nowak. “Customers are currently asking to provide these higher throughput rates with the twin screw extruder, while at the same time keeping overall machine sizes and foot prints. Processing high meat levels requires a reduction in throughput rate relative to classic dry food. The challenge for the extruder manufacturer is to develop methods that allow the higher throughput rates needed to process the high meat slurries within the extruder, while still maintaining overall physical size.”
Coperion has test centers in both New Jersey, USA, and Stuttgart, Germany, to help pet food manufacturers with process and product development challenges brought on by current industry trends. | Photo courtesy Coperion
Trends and innovative leaps aside, technology does have its limitations. So how are extrusion experts working with existing technology to continue making things happen with current needs?
“We have learned over time to train ourselves to constantly think ‘outside the box’” said Henry. “The industry has learned that innovation for the sake of innovation usually reaps poor returns. They have become less impressed with shiny new packages and more focused on true value-added improvements. Extru-Tech watches the market and market trends very closely and has open communications with our client base to not only keep abreast of current manufacturing needs but also to fully understand what the future market challenges will be.”
Keeping abreast of current industry trends really is a team effort.
“We believe it is more about the internal culture of technology and equipment suppliers that drives solutions for the industry,” said Rokey. “Within Wenger, the challenges related to innovation are overcome by support from leadership, utilizing internal experience, and an environment or system that encourages a culture of ingenuity, integrity and initiative.”
And, overall, the biggest “must-have” for success is flexibility, not just in ideas but also in actual machinery, as far as current technology will carry it.
“The extrusion lines must be able to cope with this acceleration and variability in product launches,” said Maller. “Therefore, the base extruder must have substantial built-in flexibility for quick change over. Features such as quick opening of the barrel and intelligent control can be complemented with clip-on technologies; e.g., ancillary equipment that can be added on the extruder to make different products.”
There’s no doubt that extrusion experts in pet food see the need to push their technology to the limits, and they will continue to do so — with innovation, with teamwork, with an eye towards the future — to keep the industry thriving.
Two things to know about the future of pet food extrusion