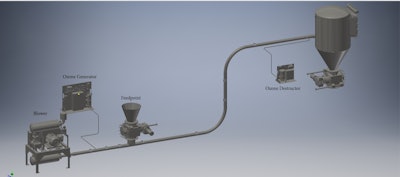
Pneumatic conveyors are essential to the dry pet food manufacturing process. With large volumes of ingredients and finished kibble traveling through them every day, they must be kept at the same state of cleanliness required of other food-handling equipment.
However, pneumatic conveyor piping presents a challenge to cleaning and sanitation for several reasons:
● Disassembling pipes for cleaning and sanitation can cause significant disruption to the manufacturing process.
● Surfaces in need of treatment are internal, so they are inaccessible by normal cleaning methods.
● Pipes are typically installed in areas that are difficult to reach.
● Pipes naturally have joints where debris can accumulate.
Options for cleaning pneumatic conveyors
The cleaning process should remove any debris that could harbor microbial growth. For lines that feed into an extruder, this reduces bacteria and similar contaminants to levels low enough that, even if they come into contact with ingredients, the high heat of the extrusion process will render them harmless.
For cleaning, three main methods are used:
● Pigging means sending several projectiles, or “pigs,” through the pipeline to remove buildup. Each pig should match the interior diameter of the pipe so that it scrapes debris from the entire pipe wall as it moved forward. The dimension of the flow path must be consistent throughout; otherwise a pig can get stuck, or it may fail to scour the entire pipe interior.
● Dry ice is carbon dioxide frozen to −78.5 °C (−109.3 °F). Sending dry ice pellets through the line freezes debris, making it brittle and easier to remove, while the pellet shape scrubs the pipe interior. Evaporated dry ice leaves no residue and can be vented with the convey gas.
● Scouring material removes debris through high-velocity contact with pipe walls. The scouring material may be off-spec kibble, dried corn, salt, or any abrasive food material that would be acceptable in the line if small amounts remain after cleaning.
Options for sanitizing pneumatic conveyors
Once cleaning has taken place, sanitation may be necessary—particularly in post-extrusion lines, where the presence of microbes can lead to contamination of the final product. The goal of sanitation is to destroy these pathogens.
Three methods are common:
● Ozone gas is an oxidizing agent that has the ability to destroy the cell walls of microbial contaminants. Using ozone gas to sanitize conveyor lines involves injecting ozone into the line, monitoring the concentration of ozone along the line, and maintaining adequate levels to destroy microbes. As a gas, ozone expands to cover the entire internal surface of the line, ensuring complete sanitation.
● Liquid sanitizer is sprayed directly into pipes through a hose or via injection points, or it is infused into a sponge-type pig. There is no validated way to ensure adequate surface coverage with liquid sanitizers, and they may be difficult to remove..
● High heat is commonly used to address pathogenic microbes, but the type of heat is crucial. Research by Schenck Process shows that moist heat is much more effective at killing microbes than dry heat. “Elevated temperatures with purposely raised moisture content have a much larger killing ability,” says Jonathan Thorn, executive director of process technology at Schenck Process. “The pathogens naturally want moisture, and as they take it in, they are scalded by it.”
Determining the best cleaning & sanitation methods
No one method matches the needs of all pet food plants. The “right” method depends on a variety of factors, including the plant environment, the ingredients handled, equipment specifics, and cost.
“The approach is going to differ slightly depending on whether [the pneumatic conveyor] is a new system or an existing system,” explains Thorn. “In a new system, we design the piping, couplings, and rest of the line to accept the customer’s preferred cleaning method. When it comes to existing systems, we review what’s in place and what obstacles there are to employing each of these methods, then work with the customer to choose the best solution.”