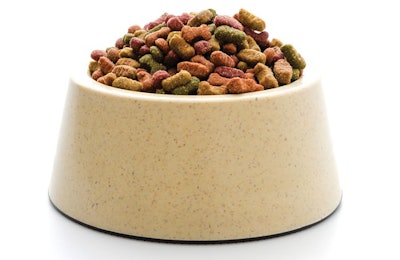
Pet food and treat extrusion generally produces far higher volumes than can be sold by small dog, cat or other animal food companies. However, as more pet food start-ups enter the field, smaller companies may still use ingredients produced on extruders. Similarly, as consumers demand pet foods that resemble their own artisanal eats. However, the extrusion process tends to produce uniform kibble and treats that clearly were made in an industrial process. To address this, extruder operators can manipulate their machines to make mass produced pet foods look like they came out of a small batch oven. Two pet food industry experts shared tips for using an extruder to make artificially artisanal kibble and pet treats, during the Q&A of the Petfood Forum Connect-ED presentation by Will Henry, R&D for Extru-Tech.
“There are some tricks we can do at the extruder kind of give it a non-cookie-cutter look,” Henry said.
When Henry’s team helps clients develop new products at the company’s pilot facility in Manhattan, Kansas, USA, they often do the opposite and turn an artisanal pet food or treat recipe into a process formulation. Part of that transformation involves keeping the sensory characteristics of the recipe produced in a mixing bowl.
Tricks to make extruded pet products look homemade
For example, to give texture to the outside of a product, extruder operators can mount a powder feeder. In a current project, Henry’s team will attach a powder feeder to the throat of the extruder. The powder feeder will drop whole steamrolled oats into the extruder.
“When it comes out the extruder, you're getting a nice biscuit shape, but it's got a texture with those steamrolled outs as well,” he said. ”It gives you the mass production you need to hit a broader market at an economy of scale, but still gives you an artisanal kind of look and feel to the product.
Another trick Henry’s team uses is to turn the knives in the extruder around backwards. Instead of consistently cutting the product at a set shape, it becomes a bit more irregular. To create meat analogues, he uses a different technique.
“If you want it to look like just a chunk of meat that you pulled off of a cooked chicken breast, we've done those type of products with some adjustments at the die,” he said. “Sometimes we flip the geometry of the die around, so instead of funneling the product to a smaller shape, we funnel out to give it an irregular expansion characteristic.”
Extruded pet food ingredients for small companies
At a typical scale, pet food extruders produce 10 to 12 tons an hour, Henry said.
“The process of extrusion is really an extraordinarily high throughput starch cooking machine,” moderator Greg Aldrich, associate professor and pet food program coordinator at Kansas State University, said. “It's generally designed or engineered for large scale production, so it may not fit in homemade or small-scale operation directly, and I'm going to emphasize that.”
For smaller companies that don’t need tons of kibble or treats per hour, extruders may come into play, Aldrich said.
He gave the example of using an extruder to produce sorghum crisps, resembling puffed rice cereal. Those crisps then went into a formulation for something like a granola bar for dogs.