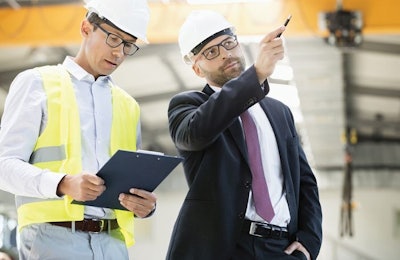
Pet food safety is a highly complex area, and given the stakes — assuring safe, healthy products for people’s beloved pets — determining the cause of an issue often requires a completely thorough approach. Where do you start?
During an Ask the Pet Food Pro Zoom chat, “Tips to maintain safety in an aging pet food safety plant,” Andy Dean, technical support coordinator for Ecolab, offered his “secret recipe” for uncovering a safety issue that isn’t readily apparent. “In some cases, if I’m working on a micro issue and walk into the plant, and I can see a piece of equipment, I notice the issue,” he said. “That’s not always the case. And you’ll have to dig deeper. It’s not real common for just like, aha, that’s the smoking gun.”
That’s when Dean’s secret recipe comes in, and I think he uses the term ironically because it’s such a commonsense, straightforward idea: Listen, ask and look. This recipe, he said, is one that any pet food plant operator, safety or quality manager can use.
Listen and ask pet food operators
In listening to what operators are voicing as their concern, try to truly discern what the point of pain is, Dean advised. “Have an open and honest communication to really get at the significance, that this is our true issue.”
Asking means starting with the five W questions: Where, what, why, when, who? “What is the specific issue, and when did it occur? You might have a seasonal issue, or we may have had some changes,” Dean explained. “So if we have a change management program, something may have changed that we can go back and say, ‘Aha, we have this, we made this change and added in product, X, Y, Z to our formula. And now we’re having issues.’
“Or, seasonal issues can play a big role with roof leaks and changes in relative humidity, even changes in weather,” he continued. Pests also tend to be more prevalent during certain seasons. “Windows and doors being left office open in the summer; usually, that’s a big one,” he added.
“Also ask what’s been tried so far, the corrective action or preventive action. So they may have already tried some things. Hopefully, it wasn’t a shotgun approach,” Dean said, explaining that if you try too many corrective actions at once and the problem goes away, you probably won’t know why. “We tried 12 different things and we really didn't solve the problem; it’s probably going to come back.”
Finally, in terms of asking, what does the data say? “Everybody has data in the plant, whether it’s paper records or electronic records, we can do some visual interpretation of what that data says. That’s pretty important,” Dean explained.
Look at everything, using all your senses
That transitions into the “look” part of recipe: reviewing the documentation and what the data tells you. “Then physically look at the conditions in the facility,” Dean said. “What do you see? What do you smell? What does it feel like? What is the overall aura of the plant?” Look up, look down, look under, even look inside. “If you do look inside, make sure you're following your safety protocols,” he cautioned.
Dean added that he follows this same recipe every time he visits a pet food plant. Pet food safety and production personnel should consider following it, too.