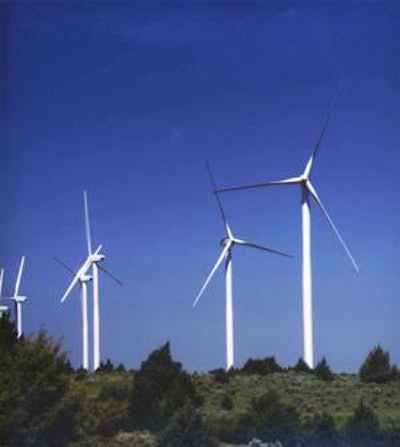
When our industry looks back at 2009, we might consider it the year of the greening of petfood, at least in the US. This year has seen the opening of several new or retrofitted US facilities-plants and office buildings, for manufacturers and suppliers-designed to be more environmentally friendly. Some have even earned Leadership in Energy and Environmental Design (LEED) certification from the US Green Building Council ( USGBC ).
Why the seeming boom in sustainable construction? While their green facilities build good will with communities and customers, these companies are not acting solely to get good PR or help save our planet. Rather, they're learning an equation already discovered by other organizations and in other parts of the world: green = green.
In other words, the sustainable features of these buildings make good business sense, too, especially in a troubled economy. Besides saving on energy usage and waste removal, such facilities are more efficient overall and are often eligible for tax credits or grants as governments encourage use of more sustainable energy sources.
The buildings shown here are not intended to be a complete list of sustainable facilities; we realize more are out there or being planned for the near future. If you know of others, please post information at www.Petfood-Connection.com/group/sustainability or e-mail [email protected] .
Canidae: the answer is blowin' in the wind
On the wide flat plains in the center of the US, nearly constant wind turns 34 massive turbines comprising the Oklahoma Wind Energy Center (in Woodward). The power generated-50 megawatts at peak capacity-supplies 100% of the electricity for the plant where Canidae Pet Food manufacturers its all-natural Snap-Biscuits and Snap-Bits dog treats.
Canidae says it saves about 1 pound of coal for every kilowatt-hour generated by wind. Besides this eco-friendly design, the state-of-the-art plant also employs many safety features. "Our commitment to petfood safety in this wind-powered facility takes the form of an in-house hi-tech laboratory where safety and nutritional tests are conducted daily on both incoming ingredients and finished goods," says Jason Castillo, company controller.
The plant is also designed to support the local community by offering much needed jobs, Canidae says. Click here for more information.
Cardinal: off the grid
At the end of October, Cardinal Laboratories' manufacturing and distribution center in Azusa, California, USA, converted completely to solar power to manufacture its pet care products, including dog food and treats. The company claims to have not only the first completely solar-powered production facility in that city but also the first in the US pet industry.
Working with the Solar Partnership Program of the City of Azusa, Cardinal is now harvesting so much power from its solar collection system-a white roof with 320 solar panels covering 5,440 square feet-that it is sending electricity back to its local utility and was able to install air conditioning for the first time, via a state-of-the-art, optimal efficiency air control system. Other energy-independent features include more efficient machines, new prismatic units to replace skylights and sensors to turn off lights when an area is vacated.
All this comprised phase one of Cardinal's energy independence initiative. Phase two, which just started, will convert its dog food and treat distribution center, two miles away in Baldwin Park, California, to solar power. Phase three involves construction of a 70,000-square-foot distribution center next to the manufacturing facility that will be powered by geothermal and solar and is designed to meet USGBC specifications.
Cardinal president Tony De Vos believes that despite the current economy, these changes are not only good business moves but also the socially responsible thing to do. "Looking at our environment from the big picture point of view, taking steps to get off the power grid and reduce our carbon footprint makes sense for our company, our world and future generations," he says.
Read more about Cardinal's green movement.
Mars: LEED certified in Arkansas
Mars Petcare US has made strides for several years now to reduce its impact on the environment: expanding its plant recycling systems, modifying packaging from paper to woven polypropylene and significantly reducing its solid waste, the company says.
"Just a few of the steps we've taken with our petcare business in the last few years have resulted in the elimination of 4,500 tons of packaging per year and 2,300 tons of carbon dioxide emissions," adds Kevin Rabinovitch, global sustainability director for Mars Inc.
But this year the company topped itself with its new plant in Fort Smith, Arkansas, USA, opened at the end of September. The US$80 million, 305,000-square-foot facility earned LEED gold certification, a first for the company-and, Mars says, it's the first sustainable manufacturing facility in Arkansas and the first sustainable petfood plant in the world.
Using grants and other incentives from the state of Arkansas and the city of Fort Smith, Mars built the plant with water recycling and energy reduction programs as well as mechanisms to protect against erosion and light pollution. Plant manager Chris Hunter says the company will also work toward an operational LEED certification once it has been open longer than a year.
The facility is manufacturing Mars' Cesar Canine Cuisine line for small dogs.
Natura: eco-friendly office in the office, too
Perhaps it's no surprise that a company called Natura--with
brands of petfood such as California Natural, Karma and Mother
Nature--would invest in a green building. That's exactly what it
did with its new office in Davis, California, USA, opened in
April. Environmentally friendly elements include:
• Pre-wiring for future solar panel usage;
• Energy Star-rated equipment (a
US
governmental program
);
• Bike racks to encourage employees to commute by bicycle;
• Low-emissivity windows to allow for natural lighting;
• Operable window to allow for fresh air and natural
heating/cooling;
• Motion sensors to automatically turn off lighting when
not in use;
• Water conserving features such as drip irrigation and a
bioswell for runoff water; and
• A video conferencing system between this office and the
company's plant in Nebraska, to reduce employee air travel.
"The new facility allows us to create an enhanced workplace for our nutritionist team while also reinforcing our commitment to sustainable business practices," says Natura Pet Products CEO Peter Atkins, whose office is also in the new building.
Other steps the company has taken to reduce its carbon footprint include changing to recyclable packaging for its Karma organic dog food, switching to hybrid cars for corporate and sales teams, reducing paper consumption by moving most internal communications online and using 100% post consumer waste paper and vegetable-based inks for printed marketing materials.
Nestlé Purina: power from the sun
In May, Nestlé Purina PetCare celebrated the installation of a pilot solar energy array on its plant in Denver, Colorado, USA. The 467-panel, 100-kilowatt photovoltaic system, covering 21,000 square feet of the plant's roof, made the company the first manufacturer to use renewable energy to produce petfood, according to Nestlé Purina.
Though the system will provide only 1% of the facility's electricity needs, the local utility would emit nearly 300,000 pounds of carbon dioxide per year to produce the same amount of electricity, according to Nestlé Purina. (That amount of emissions is equivalent to what 23 cars would emit annually.)
"Nestlé Purina has taken many steps toward achieving our goal of becoming the leader in environmental sustainability in the petfood industry," said Mark Burns, vice president and director of manufacturing.
"Utilizing renewable energy at our manufacturing facilities is just one part of our overall company plan to create shared value for society, which means going beyond compliance and sustainability and really making a difference for the long-term."
The new system in Denver, which was supported by the Colorado government and is the state's largest privately owned solar array, is just the latest effort by the company to increase energy efficiency; it says that between 1998 and 2008, it reduced energy usage at its nine dry petfood plants by about 20% per ton of product produced. In addition, the company employs a person at each of its US plants who is responsible for environmental and energy management.
Next up are solar arrays for two other Nestlé Purina plants-in Flagstaff, Arizona, and Maricopa, California-one of which will be twice as large as the system in Denver. All these renewable energy systems will help the company work toward its global corporate goal of improving energy efficiency by 2% this year.
Novus: going platinum
Platinum certification is the highest LEED level awarded, and it's been achieved by fewer than 100 buildings in the US. One is the new global headquarters of Novus International, a supplier of animal (and now human) health and nutrition products, based in St. Charles, Missouri, USA.
Opened in June, the US$20 million, 20,000-square-foot building encompasses open office space, the company's research center (including 10 laboratories), a state-of-the-art employee and customer training center, plus a complementary fitness center and cafeteria (offering nutritionally balanced lunches) for employees.
"Our business is the creation of sustainable programs that enable health through nutrition for people and animals," says Thad Simons, president and CEO. "Through the construction of this facility and earning our LEED platinum certification, we are sending a message to the world regarding our sustainable efforts, while achieving a superior work environment and reducing our operating costs."
The building's sustainable features include:
• The largest array of solar panels in Missouri (5,000
square feet);
• 100% of energy purchased through renewable energy
credits;
• 10% of materials from salvaged sources;
• 30% of materials from recycled content, such as
countertops made from recycled milk jugs and scrap aluminum and
the fitness center floor made from recycled tires;
• A state-of-the-art, under-floor air distribution system
for high energy efficiency;
• Landscaping with native grasses and plants requiring no
irrigation, thus saving thousands of gallons of water each
year;
• A framework to grow a plant "canopy" for natural
shading;
• A storm water system to reduce runoff;
• Skylights and floor-to-ceiling windows to maximize use
of natural light; and
• Preferred parking for low emission and fuel efficient
vehicles.