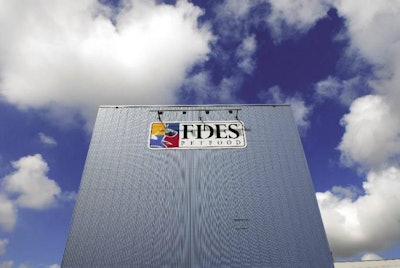
Being a successful player in today's fiercely competitive private label petfood arena requires exceptional flexibility and solid cost controls. This basic thinking guided the setup of Fides Petfood-both its business model and the 2006 construction of its plant in Ostend, Belgium.
Part of Group Depré, Fides Petfood operates an ultra-modern plant that stems from the decision to establish an autonomous, dedicated production site, entirely focused on private label dog and cat foods. The goal was to improve its products and better meet specific market requirements.
A diverse feed mix
Group Depré, one of the top five feed companies in Belgium, is a diverse mix of animal nutrition endeavors. It has produced compound feeds for more than 60 years. It entered the petfood industry in the 1990s, with the production of foods for birds, small animals and cats and dogs. Fides Petfood represents a big step toward expanding the group's branded lines, which are marketed through its sister company Beduco.
"We see Fides as a private label company in every respect," says Kurt De Cock, Fides' plant director. "We do produce our own brands like Fides Breeder Line and Euro Premium, and they are distributed by our sister company Beduco, but Beduco operates totally separate from us.
"All we do is petfood manufacturing," De Cock continues. "From our point of view, Beduco is a customer just like any other. However, when it comes to attaining maximum efficiency," explains De Cock, "Fides monitors Beduco stocks, thus allowing optimum production planning for just-in-time delivery."
Just-in-time approach
One of Fides' goals is to use the just-in-time approach with as many customers as possible. This produces benefits for both sides, but it requires a lot of work building partnerships based on mutual commitment, according to De Cock.
From the beginning, Fides chose to have a very limited warehouse capacity and produce based on customer demand. With a one week lead time, Fides fills 95% of its orders.
"On one hand, this eliminates some potential clients that need more products in stock," states De Cock, "but it enables us to produce as efficiently as possible. Most important for a private label company are volume and reducing costs. If you can't control your costs, you lose your profits. Cost control and the ability to produce on demand are what make us different from our competitors," he says.
Tailor-made kibble
A key issue for Fides is guaranteeing the consistency of all tailor-made kibbles, which range from superpremium to mass market products. Various products are produced for different clients in both wholesale and retail (supermarkets, horticultural centers and specialized pet stores).
Fides responded to this challenge with a lean organizational model. This was not a reengineering of a pre-existing, less efficient process, but the application of a systematic improvement approach, aimed at obtaining greater efficiency and reducing wasted effort, time, space and cost. In other words, Fides worked toward reducing all activities that did not add value.
The new factory was designed to allow further expansion (e.g., to double the extrusion line) with minimum additional investment. It is fully automated and needs only eight people to run-mostly working on the packing line.
Fides Petfood can therefore count on a modern and flexible production line that complies with the highest quality standards and makes it possible to deal with shifting customer demands. The company has the flexibility it needs to deal efficiently with business variability.
Energy efficiency tactics
Establishing the new Fides plant in Ostend, Belgium, was a strategic decision by Group Depré. The company has been very careful in selecting every supplier and setting up a modern production unit with a fully automated, PLC-controlled extruder line and state-of-the-art equipment.
Fides chose Ottevanger Milling Engineers, one of the leading European companies specializing in equipment for processing grain and the production of compound feed and petfood. Ottevanger designed the Fides plant and managed construction and procurement of equipment: a macro dosing system, a micro dosing system, a grinding and mixing section, an extrusion line and a drying, coating and cooling system. The plant can produce 6 to 9 tons of petfood per hour.
Future improvements
Future improvements include the possibility of further automation of the packing line, as De Cock explains: "So far the majority of our bags are 15 kg, but the smaller packs are becoming more and more popular.
"Now we can do it all on the same line, but we have to divert the 4 kg or smaller bags to another line where we can pack separately," De Cock continues. "So this is something we are definitely looking at right now, but we must be sure we can do it with maximum efficiency."