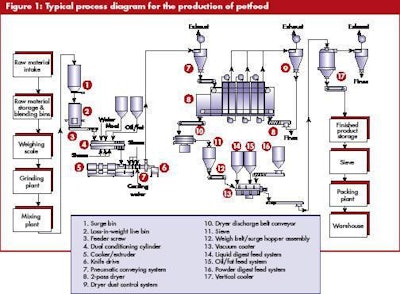
In the petfood industry we use massive amounts of energy. With the combination of ever increasing energy costs and public and legislative pressure to reduce energy use, now is the time to increase efforts to measure and minimize energy costs.
Most major retail chains have made commitments to drastically slash the carbon footprint for their own operations, with a parallel target of adding a carbon label to all of their products. It is in our interest as an industry to tackle these issues urgently.
Start at the top
I recommend a unified method for approaching the subject, thus preventing fragmentation of standards and techniques. The first issue with any company is to ensure the project is fully endorsed by all of the key decision makers, starting at the top. One senior person is normally designated as energy manager. For smaller companies this can be an existing manager.
Often there is a need to bring in support from outside the company, usually in the form of consultants with the appropriate skills. The company need not rely on any one organization, as there will be a lot of expert help available from existing suppliers.
Define scope and implement
The next step is to define the overall scope of the project. This may be a simple definition of targets for energy reduction or may be much more complicated, covering corporate ambitions to achieve ISO 14000 environmental quality management accreditation.
As with all projects, poor planning produces pretty poor performance (5 Ps). Initial planning should be thorough. There are plenty of public resources available that can help. Use the Web to check federal, regional and state resources. These will help with advice on implementation strategies, financial assistance available and regulatory issues. Also study models of strategies used by companies around the world.
When implementing the plan follow these rules:
- Plan and re-plan before doing anything.
- Measure consumption before acting.
- Make changes to improve performance.
- Validate the beneficial effects of the changes.
Look at overall consumption
Overall consumption can be reported in several ways, usually cost per unit of product, expressed either as monetary value of product or as weight. Expression as cost per weight of product is more convenient because historical comparisons can easily be made as the project progresses, especially where external influences produce large changes in product pricing. However, energy costs as a proportion of product value is important, especially when looking at added value products vs. low margin products.
Map before measuring
Map out the process before starting detailed measurements or committing money to expensive instrumentation. This can be in the form of block flow diagrams, plan maps of the facility or a process flow chart of the plant (Figure 1).
Use the process map to identify key points for energy measurement. It is a good exercise to measure no-load and full-load power consumption of all electric motors, but at the very least target the large motors with the most potential for savings. Also have product samples tested thoroughly for quality characteristics, as these will be used later for comparison.
It's ideal if the entire plant has all its parameters measured for every product when running under equilibrium conditions, with all the motors also measured when under no-load conditions. This will allow a snapshot view of key performance indicators (KPIs) for each product. The following list indicates some useful baseline KPIs per unit of product, whether this is measured in weight or value.
- Total direct energy costs;
- Extruder specific mechanical energy;
- Extruder total electrical energy;
- Extruder/conditioner specific thermal energy;
- Dryer thermal energy costs per unit of product;
- Dryer thermal energy costs per unit of water evaporated;
- Dryer electrical costs;
- Extruder cooling water costs;
- Loading factors on dryer and cooler exhaust air systems;
- Loading factors on pneumatic conveyor;
- Energy cost of pneumatic conveying; and
- Power factors.
This baseline can be examined against known standards.
Improving performance
The ideas presented in this article are strategies that have been used to reduce energy costs and/or improve rate and product quality. These are opportunities, in some cases, to save up to 25%. These savings are over and above all the other savings that can be realized.
Reducing energy costs is highly complex and should be approached in a highly systematic way, ideally reflecting methodologies and practices recommended by government authorities and the many initiatives introduced by retail chains. There are many competent organizations that can help us audit our energy costs and carbon footprint, but it is in our own industry that we have the skills to address the heart of our processes to minimize these costs.