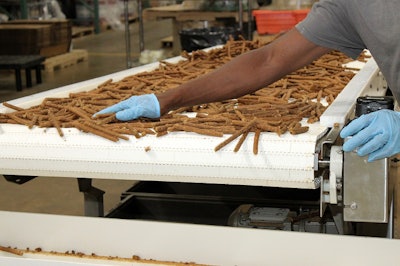
Equipment is a significant capital investment in any manufacturing facility, and pet food is no different. The machines that produce pet food are expected to do their job, well, for a significant number of years before needing replacing. How, then, does the industry keep up when production needs grow more complex and pet owners continue to demand more of the products they buy?
“The equipment that built the pet food industry (such as ovens, retorts, extrusion, co-extrusion, batch and blend) is reliable, well-understood and not likely to fade from favor,” say experts at CRB, a full-service facility design, engineering, construction and consulting firm for biotech, pharma, food and beverage, and science and technology. “Still, balancing the fit and function of this legacy equipment with the need to optimize is key. By focusing their attention on improving these aging systems while also taking steps to reduce supply chain risks and retain a skilled workforce, manufacturers will get the greatest bang for their capital spend.”
Four ways to generate value from existing equipment while addressing current needs
According to CRB, there are four opportunities to make this happen.
First: Address aging, inefficient and bottlenecked equipment. It’s neither practical nor necessary to get rid of traditional equipment that works and has staying power, such as machinery involved in oven baking — a popular processing method that isn’t going anywhere any time soon.
“If ovens are here to stay, how can manufacturers improve their efficiency at a process level?” asks CRB. “The key is twofold: First, look to other food categories that have perfected the oven baking approach, like bread manufacturing, and learn from their success. Next, conduct a detailed study of your current approach and use that as an opportunity to run scenarios before you make real-world adjustments. This is good advice for manufacturers seeking to improve any processing equipment, not just ovens: Taking a step to uncover exactly where your efficiency gaps are (rather than jumping at the first available solution) could save you time — and money — in the long run.”
Second: Adopt an integrated supply chain strategy. If companies weren’t considering their supply chain two years ago, they certainly are now, with global instability forcing everyone to take a hard look at how they might both diversify and tighten up their supply chains.
“What can these manufacturers do at a process level to enable new supplier relationships while mitigating against quality risks?” asks CRB. “The best approach is an integrated one. Think of the end-to-end product development and manufacturing pipeline as a whole, with R&D, quality control and process development teams working hand-in-hand to support any necessary ingredient changes. Shifting to a nut-based protein source, for example, invites the risk of contamination from bird droppings or other sources of bacteria common to outdoor crops; this may require adjustments at the kill step to ensure ongoing quality and regulatory compliance. By continuously sharing knowledge between the lab and the commercial production floor, manufacturers can make these process updates proactively, readying their plant for a fast and flexible response to supply chain interruptions and opportunities.”
Third: Implement a robust labor strategy. Pulling together a reliable and productive workforce has also become a more complex prospect during the pandemic, with many companies reconsidering their labor needs moving forward.
“A forward-thinking manufacturer can make a few strategic changes at the process level to partially address ongoing labor constraints,” say experts at CRB. “First, there’s automation. The more you’re able to design automation into your process and design human operators out of it, the less exposure you have to the risks of an unpredictable labor market. Of course, along with automation comes the need for workers who understand how to design and maintain these advanced systems, which poses its own challenge — particularly for pet food manufacturers whose facilities are often located far from urban technology hubs.”
Of course, automation will never be able to completely replace the human factor, so it’s important to ensure that your facility is one worth working at.
“Attention is due to factors that will attract and keep workers on the job,” says CRB.
Fourth: Rethink your approach to sanitation. The need to attract a reliable labor force segues directly into this thought, as the sanitation aspects of any job are often the least desirable.
“For manufacturers looking to make the biggest impact on the environment inside their plant, the best place to focus is also the dirtiest part of the process: cleaning and sanitation,” says CRB. “Small and relatively inexpensive adjustments in this area could yield significant gains over time. The largest companies have figured this out, reducing their wash cycle to just 10% of their overall effort (according to CRB’s 2022 Horizons: Pet Food report). Smaller companies would be wise to follow this example and reap the rewards in terms of labor retention (because cleaning is an unattractive job), increased throughput (because less time cleaning means less downtime) and improved sustainability (because an efficient cleaning process uses fewer resources).”
For the companion article, "Efficiency, flexibility current top pet food equipment needs,” published in the December 2022 issue of Petfood Industry magazine, see www.PetfoodIndustry.com/articles/11769.