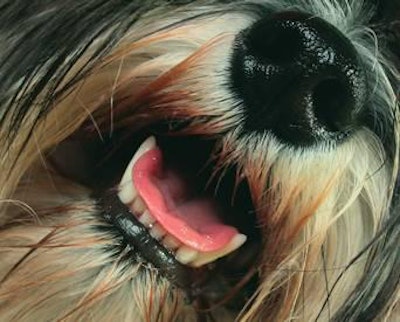
"Odor reduction is important to stakeholders, which includes people living in the community near your plant," said Tjitze Smit of GrainTec A/S in his 2011 Petfood Forum Europe presentation, "Energy Recovery and Odor Reduction in Petfood Production." An angry mob of townspeople showing up at your facility's door, complaining about how your business stinks, is no way to foster community spirit, much less garner popularity with local consumers. Let's sniff around for the best, most cost-effective, energy-saving methods available to petfood producers today.
The good news? When you compare aquafeed, petfood and animal feed in terms of odor, aquafeed produces the most intense aromas. There’s a large drop between aqua and petfood in “extruder flash-off” when odor is emitted, but not as much as from the dryer, according to GrainTec research. You can measure this, in addition to perception and intensity of odor.
According to Uniqair, makers of plasma injectors and other odor reduction technologies, odor is complicated because very often it is a cocktail of hundreds of different organic components. The weight concentration (ppm) is mostly very low, but the odor concentration (ou/m3 or DT = number of required dilutions with clean air in order to just become odor free) can be very high. The odor components with the lowest concentrations cannot all be detected analytically, but the human nose may very well notice them. So by this way it is impossible to make accurate calculations or predictions on odor emission. The only way to determine odor reduction efficiencies, according to Uniqair, is with olfactometric measurements.
What kind of odor reduction methods are available and how effective are they? Smit breaks them into these six categories:
1. A chimney is not very efficient but is inexpensive, and is often the logical first step towards reducing production odors.
2. An ozone (plasma) reactor operates at 70-85% efficiency. GrainTec says this technology has low capital costs, but is expensive to operate, while manufacturers of the equipment (like Applied Plasma Physics A/S) claim higher efficiency and lower operating costs.
3. Biological/chemical or seawater scrubbers boast 70-90% efficiency, but also come with both high investment and high operating costs. This odor reduction technology is mostly used in aquafeed production because those plants are usually close to the sea.
4. A bio filter —like wood chip fillers—output a 70-95% efficiency. Often used in conjunction with freshwater scrubber, a bio filter requires a good deal of space to operate in and can be costly to run.
5. A regenerative thermal oxidizer is certainly an expensive odor reduction alternative (high investment, very high costs to operate), but provides 90-98% efficiency.
6. Total recirculation systems including a coal filter will provide 98-99% efficiency. Although an initial high-investment cost, this technology recovers and reduces thermal energy, as well as reduces odor emissions.
Once you have determined what odor reduction technology is best for your company, you must implement an installation process. If you are starting from the ground up with a brand new facility, you can build and design for odor control from the beginning. If you are Roger Mohr, director of BYNSA, however, you have to retrofit an existing factory by adding equipment—in this specific case, three Applied Plasma Physics (APP) units, one for each extrusion line and new airflow ducts. In Europe, Mohr and his competitors also have odor control regulations manufacturers in other parts of the world don't yet have to worry about, but would be better off getting prepared for now. As it stands, the current EU standard has been written, but responsibility for regulation is up to individual countries. Eventually the regulation could be mandatory, and there's no question it’s good for the community—if neighbors complain about odor, local authorities can crack down.
The APP units are flushed with water to clean dust deposits once a month at the BYNSA plant. They have fans with three different speeds, based on temperature of the dryer air coming from the extrusion lines. Each unit has a cooling system, too. Each unit has its own control interface, according to Mohr, but it’s also part of the factory’s overall PC control system. In addition, the units are connected via the Internet to APP in Norway for remote monitoring and service, reducing cost/time if a problem arises. The APP technology falls in the Best Available Technique category under IPPC. For more information on APP, go to www.app.no/solutions/odour-abatement.
Uniqair not only recognizes the petfood industry as an important market segment for their plasma odor control systems, but knows how hard it can be to obtain regulatory approval for expansion of production, while controling the odors from dryers, extruder air conveyers and coolers. The company has sold over 50 plasma odor control systems to the petfood and feed industry world-wide. In October 2011, Uniqair introduced their latest innovation with cold plasma technology: PECO with Stack-Xtender for up to 98% odor control (PECO: Plasma Enhanced Catalytic Oxidation). This new plasma technology causes no impact on the production process, no chances of plugging/jamming and has little to no maintenance, according to the company. For more information, go to www.uniqair.com.
There are no competitive advantages to controlling odor pollution—only costs—and you can't promote the great lengths your company goes to to provide odor reduction since the public at large already expects such strides. But it’s certainly the right thing to do. And your neighbors' noses will thank you!