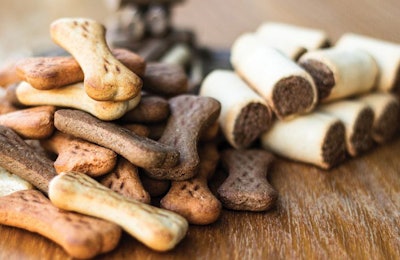
Sustainability, as a trend and as a corporate responsibility, is touching every aspect of pet food. Some parts of the process seem more straightforward: pet owners are looking to the traceability of raw ingredients and the recyclability of packaging as the frontmost attributes of sustainability. But those desires encompass a lot more than just their specific place in the pet-food-making process. Take extrusion, for example. What does sustainability look like to those who make and maintain the machines and processes that help create the end product?
Optimization in machinery a key facet of extrusion sustainability
“Sustainability is the consistency of the optimum running of an extruder,” said Nigel Lindley, managing director and independent consultant at N.L.C. Eco, which focuses on extrusion sustainability in the pet and aquatic industries. “That’s one of the key points. It’s keeping down costs, it’s how long parts last — being able to run a machine for the longest time without having to change a part.”
But since everyone needs something different, being able to maintain flexibility as a supplier is important in order to meet individual sustainability goals.
“[We are] listening and making sure our product portfolio is diverse, flexible and modular, so process solutions that are created make the most for the goals of fiscal responsibility (value), product diversification (new creative SKUs), operational excellence (performance) and environmental integrity (efficient),” said Andy Hollister, product marketing director for the companion animal and aquafeed division of Wenger Manufacturing, which specializes in extrusion and dryer technologies. “Our goal is to have not just one type of extrusion process section or one type of conditioner, but a range of single, twin, large-volume thermal twins and conical unit operations with a variety of complementary components to make sure a correct, flexible and accurate process is implemented.”
Automation steps in to maximize control
One of the most important facets of optimizing efficiency in extrusion is being able to control the process, and the best way of doing that seems to be automation, according to the experts.
“In general, many of the underlying reasons for expanding automation also support sustainability initiatives; the most obvious one is efficiency,” said Pete Ensch, CEO of WEM Automation, which designs, installs and provides maintenance for process automation systems. “At the start of the process, automation can provide improved planning. By tying your process automation to your planning process, efficiency can be gained at managing your supply chain better, from JIT (Just in Time) receiving to reduced inventories. Better planning can result in longer campaigns or production orders, reducing lost production time from changeovers.”
Of course, the human element will always need to be involved, so it’s important to ensure both aspects — man and machine — are running smoothly.
“Sometimes you just need to have a person there,” said Lindley. “But [the technology] gives you a good starting point. You can now analyze all your production methods to show how each product is produced, how much energy is used and how efficient the operation is. You can see how a machine ran during the night shift, the day shift, etc. and see what the optimum setup was. And then you can train your guys how to produce in that optimum manner.”
The opportunities to enhance sustainable operations via automation are everywhere, right down to the day-to-day tasks that keep a business running.
“Even simple things like reducing paperwork with electronic records makes the overall organization more efficient, opening up team members to work on continuous improvement priorities versus filing out routine paperwork,” said Brad Stokke, director of business development for WEM Automation. “Most automation systems have extensive reporting capabilities.”
Ongoing sustainability efforts in extrusion
Obviously, working with customers to meet their needs is the true path to success. Optimizing products and processes, offering advice and solutions, and staying on top of the latest trends will always be sure bets, and it’s no less true with achieving sustainability at all stages of pet food production. Certifications are yet another way to help customers effectively.
“Clextral has achieved ISO14001 certification,” said Hadrien Delemazure, feed extrusion expert at the multimarket extrusion technology company. “This is the international standard for environmental management, including controlling environmental aspects, reducing impacts and ensuring legal compliance in accordance with environmental sustainability guidelines. Eco-conception is integrated in each step of the manufacturing process at Clextral.”
Extru-Tech Inc., a global extrusion parts supplier, installer and maintainer, focuses significantly on client cooperative efforts to meet their sustainability needs. According to Bob Annan, consulting/sales for Extru-Tech, some of the top ways the company assists customers is through formulation adjustments to offer a broader re-usage of raw materials, processing consultations, audits and optimization of extrusion and other components, and ongoing equipment advancements. Extru-Tech’s continuing improvement in these areas, said Annan, is how the company intends to stay on top of the evolving trend of sustainability in pet food.
As for the future of that evolution, according to Lindley, education will be important if extrusion wants to have the answers pet food producers need.
“I think [we’re in a] learning phase where everyone’s trying to find things from other industries to bring into extrusion, and it’s going to be our way into the future so we can get stronger,” said Lindley. “There’s no way back; there’s only forward from now on. I think some of it will be education that [extrusion experts] will get from experience. People are used to thinking about production and hitting numbers, not sustainability. It’ll come, but when you have a global industry and people are making big money, it takes time to shift ways of thinking.”