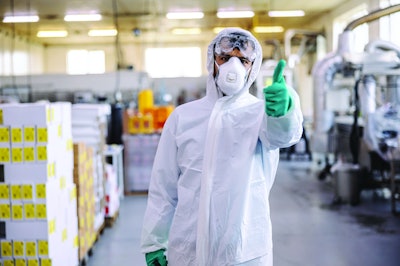
The ongoing COVID-19 pandemic has significantly affected the ways everyone does business, and one topic of primary concern has been safety. Employee safety in particular became top-of-mind as essential industries like pet food manufacturing continued in the midst of a spreading virus, including everything from personal protective equipment (PPE) to the facilities those employees work in.
“The novel coronavirus has changed everything,” said Jessica Stank, marketing manager at APEC, an equipment and control systems manufacturer. “It also brought with it more questions, as we learned about the nature of the spread and how it affects employees in the plants and the products themselves. Concerns about cross-contamination and worries about staffing shortages due to illness were at the top of mind for all industry leaders. As we adapt to the still-evolving situation, there are already noticeable changes and considerations brought on by the events of 2020. Processors are looking at better ways to keep their workers safe while meeting the increased demand brought on by things like panic buying.”
Protecting pet food facility employees
While the pet food industry already included its employees in food safety considerations, COVID-19 caused a quick adoption of even more focused plans.
“Manufacturers in both rendering and pet food production laid the foundations of safety and quality by meeting requirements of the Food Safety Modernization Act (FSMA),” said Megan Ross, food safety product manager for global ingredient supplier Kemin. “Heightened hygiene protocols, handwashing and social distancing are now tied to a plant’s food safety plan — addressing layout, segregation, airflow and sanitation protocols. This holistic approach to safety isn’t likely to go anywhere and will go far in protecting both people and product.”
One of the primary challenges in keeping production facility employees safe is proximity.
“Safety considerations changed in 2020 as processors looked to get space for the welfare of their employees,” said Jason Robertson, market director of food and beverage for CRB, a supplier of sustainable engineering, architecture, construction and consulting services. “The challenge in these operations is the proximity employees need to work next to each other in processing and packaging. Employee break areas were always a challenge [and are even more of one now] as you think about those areas and how to include social distancing requirements with so many plant workers. Many processors came up with their own novel approaches of using plexiglass or vinyl material to provide that safety barrier for their staff on the processing and packaging lines.”
Even long-established employee safety and sanitation practices have received an overhaul.
“Face masks/shields are becoming or have become standard PPE,” said Jeff Herbster, director at 1 Solution Group, a global project solutions group for the feed and food processing industries. There is also an increased importance of boot and hand-washing stations within the facilities.
But behind this renewed focus on basics is training, and ensuring every employee follows the rules to keep everyone as safe as possible — particularly if staff shake-ups occur due to COVID-19 protocols.
“Most manufacturers are struggling to staff production shifts on a daily basis due to the volatility of lost time due to COVID-19 and quarantines,” said Herbster. This has led to the possibility of an increase in total employees to help offset quarantine protocols, which means increased training in food safety and life safety, as well as specific operational or cross training, he said.
Ensuring facility safety
Obviously workplace cleanliness is top-of-mind for anyone operating in a food production environment, but 2020 really highlighted the benefits and need for up-to-date safety systems.
“As we look at the design and construction of new facilities, clients are beginning to have more conversations around bringing more fresh air into facilities with their HVAC systems,” said Robertson. “This will have an impact on operating costs based on the pure size and magnitude of pet food plants, but it helps.”
Sanitation at all levels is in sharp focus.
“Plant sanitation measures are on the rise, as we have seen renewed interest in natural biocidal compounds for the food production environment which can be used in conjunction or rotation with traditional sanitizers,” said Ross. “Other strategies gaining interest include ultraviolet sanitation protocols, advancing automation efforts and investments in new types of processing equipment.”
And as always, pet food purchasers are helping to influence how everything plays out at the production level.
“With so many consumers now embracing e-commerce, some for the first time in response to pandemic-driven shelter-at-home orders and practices, this buying strategy is not only experiencing tremendous growth but also highlights the expanding fresh diet direct-to-consumer market,” said Ross. “Ensuring that quality parameters and safety standards are appropriate and upheld in the industry is crucial to maintaining the high level of trust that consumers enjoy, especially in the context of direct-to-consumer and fresh, never-frozen, product safety.”
So, what’s to come as 2021 continues? More of the same, as heightened processes become the new standard.
“I think you can expect to see social distancing become the norm, where possible,” said Stank. “This may be achieved by automating processes (see “Automation gains interest as pet food safety evolves” on p. xx) to limit the number of people in an area. I think you will see the use of additional sanitation practices and PPE become commonplace as well; things like plexiglass dividers, face shields, etc. Businesses will adapt to this and safer, more efficient work environments will be a big priority in 2021 in order to keep staff healthy and allow the company to maintain operation, come what may.”
Top safety challenges in the pet food industry
According to Jeff Herbster, director at 1 Solution Group, a global project solutions group for the feed and food processing industries, one of the main challenges involving safety is ensuring everything is up to date, which necessitates the review of and potential modifications to:
- Facility foot traffic patterns
- Rolling stock traffic patterns
- Hand washing and boot washing stations
- Filtration and make up air systems
- Facility sanitation protocols
- Incoming ingredient testing (e.g., mycotoxin, pentobarbital, or Salmonella testing and analysis)