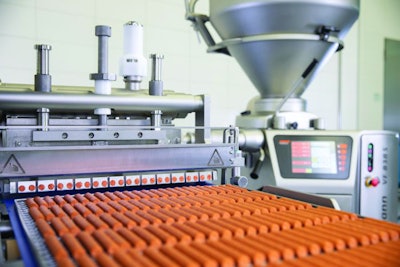
Automation serves many purposes, and the more technology advances the more benefits — and challenges — are revealed. In pet food production, automation’s many advantages are currently outweighing the potential downsides (see sidebar, "The challenges of pet food automation"), so let’s take a look at what those advantages are — and where the future of automation lines up with the industry.
Automation in pet food: providing answers to manufacturing challenges
There are many points in pet food production where errors can occur, and any one error could snowball into a line-stopping situation. Mitigating these errors, according to experts, is where automation really shines.
“The top benefits of automating your pet food production are the same for most industries; it improves accuracy, repeatability, increases productivity, ease of scalability, decreases waste, reduces human error and improves safety,” said Pete Ensch, CEO of WEM Automation, a company that designs, installs and services process automation systems.
Any one of these benefits might make some sort of automation a worthwhile venture, but with so many potential benefits it’s certainly worth a closer look.
“The immediate first-level production benefits are processing and product quality consistency throughout a shift and from shift to shift; weight accuracy with an integrated scale can virtually eliminate waste and eliminate the danger of underweights,” said Patrick McGady, vice president of sales and marketing for Handtmann, which has divisions working in process technology, filling and portioning systems, plastics engineering, light metal casting and systems engineering. “Machine monitoring with alerts helps reduce maintenance and repair issues and manage stops more quickly when they occur. Automaton with product recipes in memory also speeds start-up and changeovers while also simplifying operations which is very helpful with a changing workforce. The integration of production planning simplifies and speeds that process while also eliminating many of the most common planning conflicts and resource management issues.”
Resource management includes literal manpower, something many industries are currently facing challenges with.
“Automation is a great benefit to pet food manufacturers, especially at this moment where operation and distribution are being affected by a shortage of labor resources,” said José Coelho, Americas business director for Clextral, a company that provides turnkey processing lines that integrate extruders, dryers and ancillary equipment. “So we are seeing pet food manufacturers investing more and more into automation at different plant operation levels. Line automation enables processors to optimize their operations and improve their productivity, through continuous monitoring and feedback on any equipment’s process and/or running condition and operational performance, and can provide product traceability from raw material receipt to the finished product. Automation also enables processors to take advantage of resources from outside suppliers who offer online support.”
[clextral-extruder-automation]
Automation provides more data than ever for pet food producers looking to optimize their processes. | Photo by Clextral
Recent advances in automation: adapting human food solutions to the pet food process
By now we’re all familiar with the entrenchment of humanization in the pet food world. Unsurprisingly, advances in pet food automation come straight from the human food segment, and according to those in the industry it’s becoming more common than ever to adapt human food technology to the pet space.
“As pet food has become more humanized, the transfer of equipment from human food processing to the pet food industry has become more commonplace,” said Lloyd Parks, vice president of sales (Americas) for Cuddon Freeze Dry, which sells freeze drying equipment. “Companies that cater to human production are now offering modified equipment to suit pet food manufacturers. This is mostly true for forming, slice and dice. As regulations in pet food have become stricter and now mimic human production, equipment manufacturers are now putting more emphasis into sanitary design.”
Data is also a significant driver of automation advancements in the pet space.
“There have been several recent advancements in automation in the past several years and most of those have been around data,” said Ensch. “The cost of sensors has come down significantly, so it is more cost effective to add instrumentation to equipment. This combined with the advancements in networking has enabled pet food facilities ‘to wire’ the entire facility and bring data back to a central location. The data can be used both instantly to make process adjustments or used to look at longer-term trends to support continuous improvement projects like improving the accuracy of your batching.”
The increased availability of data throughout the pet food production process leads to a safer, more efficient plant.
“Automation has taken a deeper dive in gathering process and operation data at different levels,” said Coelho. “Nowadays, plant operations have access to each device's information from drives, sensors, motors and actuators. We now have immediate and remote access to all the information which helps in plant floor operation and quality control. Processors can track and monitor precisely from raw material reception, product manufacturing, energy consumption, waste, and production efficiency and costs.”
The future of automation in pet food production
With hot topics like food safety, traceability and sustainable processes weaving their way throughout the pet food manufacturing world, odds are automation will become even more of a sought-out solution than it already is.
“The future of pet food is heading toward improved quality, safety and the humanizing of pet food,” said Brandon Dohn, senior systems engineer for Coperion K-Tron USA, which provides solutions for state-of-the-art process equipment, particularly in feeding and pneumatic conveying components. “The owners of pets are likely to purchase and administer a diet to their pets that is produced in accordance with the safety and review expected of human food production. Product quality and safety is largely dictated by the raw ingredient delivery to the process, and with the continual recalls challenging the pet food manufacturing sector, this topic will continue to be relevant.”
Automation, according to experts, will continue to get “smarter” — to pet food’s benefit.
“Longer term, it will be using the data to create even smarter systems,” said Ensch. “We already use the data now to trigger certain events or system responses. Many critical pieces of equipment like micro scales, extruders and dryers use feedback from the various sensors to the algorithms that adjust the equipment to tighten the process control. The future will simply use more complex math and even machine learning (AKA, A.I.) to build systems that are able to respond to even greater variances. It’s amazing where things are going.”
Read more: The top 2 challenges of pet food automation