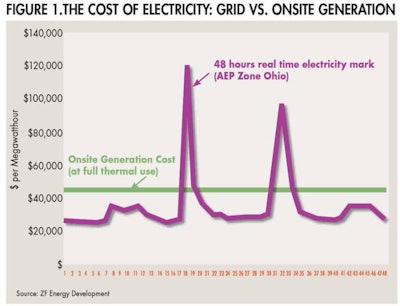
Lean and JIT (Just in Time) are well-established manufacturing principles that improve productivity, return on capital and customer satisfaction. How do these principles apply when it comes to the delivery and use of energy? In this article we suggest a new approach that brings energy management into the “Lean” thinking framework for petfood manufacturers.
Petfood manufacturing is an energy intensive process, where talk of sustainability in the manufacturing and packaging process is prolific. While sustainability is cogent for both consumer and corporate interests, and efficiency is critical in the manufacturing process, energy sustainability today offers little in terms of cost reduction. Reducing energy costs and increasing profits is an imperative for the petfood manufacturer's business and bottom line.
Energy is an expense that, while discretionary, is usually the last thing to be turned off: no energy, no production. Undoubtedly, a reduction in energy cost drops directly to gross profits. Petfood and other manufacturers know this, and have followed the path of efficiency improvements.
Today, however, market deregulation, the Web and control automation, combined with lean energy and JIT principles, offer the opportunity for petfood manufacturers to reduce energy costs further in an unexpected way.
The process of continually improving efficiency is critical to industrial manufacturing success. But does a really efficient machine mean that it is cost competitive?
Deregulated energy markets set the price of electricity in real time. Each day energy prices rise with increased demand, and fall at night when there is less demand. Further, the realtime (daily) dispatch of fuel over the most sophisticated natural gas pipeline network in the world has increased the speed of energy dispatch and cost allocation decisions.
Cogeneration is a natural fit for petfood manufacturing, as thermal demand for cooking, rendering, sterilization or drying is in the 180°F to 400°F range. Some have installed such systems, some are considering it, some have shut theirs down and sold them. As market prices rise and fall, cogenerators—which run at 70% to 85% efficiency—are only cost competitive for part of the time. Why? Because the time that a cogenerator is uncompetitive is significantly longer than the time that a cogenerator is cheaper.
In short, baseload industrial cogenerators lose money in competitive markets. The reason is simple: 60% to 70% of the time, electricity on the grid is cheaper than can be made by a cogenerator, including the value of thermal output (see Figure 1). Cogeneration systems focus on energy efficiency, and not on cost optimization.
Conventional cogeneration projects, while efficient, can’t afford their own cost of capital. After 2008 energy markets started a downward spiral and have remained more or less flat—not because of lack of demand, but because of the price of natural gas. To compound the problem, baseload cogenerators bypass most of the other market mechanisms that earn additional revenues.
If the bottom line is your metric, the numbers just don’t pencil out. An efficiency-focused approach or baseload cogeneration alone is not enough, even if power prices do rise again. Consider a cost-focused approach that leverages lean and efficiency practices, and puts into play JIT principles.
Just like the lean manufacturing revolution stepped on the notion that the run-time ratio of a production process was more important than the amount of unsold inventory it produced, the lean energy revolution is obviating the idea that a generating asset has to run continuously to create value. JIT and lean energy principles combined with new technology allow costs to be so significantly lowered that the effectiveness of the capital investment made eliminates the need of a manufacturer to invest. Petfood manufacturers benefit from lower energy costs, higher reliability and a continuous improvement process without a capital investment.
Saving energy—and money—in petfood drying
Take another look at how energy and cost savings can go hand-in-hand, in this video from Petfood Forum China 2013: http://tinyurl.com/kmgr3ke.