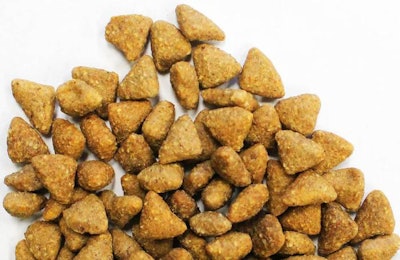
As the specialty pet food market continues to grow, consumer desires are becoming increasingly specific. No longer are “organic” and “natural” the only buzzwords pet owners want to see; instead, the segments of the superpremium pet food world are constantly expanding. High-meat pet foods are among those segments.
“High-meat pet food is generally defined as having fresh meat contents of greater than 30%,” said Sharon Nowak, Coperion K-Tron’s business development manager, and Ed Beecher, Coperion’s senior sales and process engineer. “In some cases, the combination of low-end animal protein with small amounts of vegetable protein is also used to get the texture and appearance of meat.”
It’s not just that more pet food products now contain meat at some level, according to Galen Rokey, director of process technology for the companion animal division of Wenger Mfg. Inc.—the level of meat inclusion is also increasing. “Part of this is marketing to the consumers’ desires and part is often an increase in quality attributes like digestibility,” he said. “When moving from meals to meat as the protein source, we often see substantial increases in protein digestibility in the final product. If a pet food contains at least 4% meat, the label can read, 'Made with Meat.' If the recipe contains at least 14% meat, the label can read, 'Made with Extra Meat.' If the recipe contains at least 26% meat, the label can read, 'Pet Food Meat Dinner' or similar verbiage. Some novel protein sources are only available as meat and are not available in dry meal form.”
It’s a specific response to a more overarching trend in the industry: the desire for high-quality meals for pets. “There is a trend for better-quality pet food, defined in terms of ingredients, nutrition and palatability,” said Will Henry, research and development, Extru-Tech Inc. Within this trend, he said, producers are responding to the demands of different market segments by deriving combinations from the following sub-categories:
- fresh meat (refrigerated, not frozen or dehydrated)
- higher quality (mechanically deboned skeletal muscle and prime organs—not "whole animal")
- non-adulteration (mechanically emulsified, without adulteration from water or enzymes)
- non-traditional formula (grain-free and/or limited ingredients)
- shapes (crouton and bone shapes; not just brown-and-round)
- higher meat inclusion rates (30–75% as opposed to 0–30%)
With every new trend comes new challenges, and high-meat inclusion presents a unique set from a manufacturing point of view—particularly when it comes to extruded pet foods with a high meat percentage. “High-meat, dry pet foods can be produced with a single-screw, medium-shear extruder provided that dry animal ingredients are used,” said Dave Albin, PhD, applied nutrition technologist at Insta-Pro International. “Chicken meal, meat and bone meal, and poultry by-product meal are commonly used and produce high-quality products.”
Staying on top of the high-meat trend and meeting related customer expectations are forefront in the minds of pet food manufacturers, who are attacking the challenges from all angles. | Insta-Pro
Raw, wet ingredients are much more challenging to work with, however. “Moisture and fat in raw animal ingredients counteract friction in the extruder barrel making it very difficult, if not impossible, to achieve the appropriate cooking temperature,” said Albin. “In addition, the high level of variation between lots of raw animal ingredients makes consistent processing a challenge. It’s very important to have incoming raw materials inspection programs for these high-variance ingredients and to tell your suppliers that you will only accept ingredients that are in spec. In my experience, this is a major issue that must be dealt with before products develop with these ingredients should be considered.”
According to Nowak and Beecher, twin screw extruders have the processing advantage over single screws for high-meat pet food extrusion due to the improved mixing and kneading capabilities within twin screw design. “As the request for high-meat products increases, there is an increased request in providing higher throughput rates,” they said. “Customers are currently asking us to provide these higher throughput rates with the twin screw extruder, while at the same time keeping overall machine sizes and footprints. Processing high meat levels requires a reduction in throughput rate relative to classic dry food. The challenge for the extruder manufacturer is to develop methods that allow the higher throughput rates needed to process the high-meat slurries within the extruder, while still maintaining overall physical size.”
But none of the manufacturing challenges exist independently of each other. “Our most significant challenges are not a prioritized list of stand-alone variables but a combination,” said Henry. “To produce a high-quality kibble (shape retention, digest absorption, etc.), from any given permutation-and-combination of the [existing challenges] while meeting food safety requirements—and to do so cost-effectively. For example, it’s relatively easy to extrude shaped kibbles from fresh meat, but to do so at an inclusion rate of 75%, grain-free and without engineered binders is a more intricate challenge.”
Staying on top of the high-meat trend and meeting related customer expectations are forefront in the minds of pet food manufacturers, who are attacking the challenges from all angles. One word key to success, according to industry experts: innovation. “Wenger continues to innovate to anticipate and meet process challenges through a multi-step approach,” said Rokey. “This approach evaluates each process challenge in the following areas: recipe requirements, hardware development, process controls and final product specifications. Flexible process are developed to allow our customers to meet the many needs in today’s market. Where required, education and training programs are provided to assist customers to develop their own unique products.”
According to Nowak and Beecher, Coperion has worked closely with its pet food customers in the company’s pilot plant facilities in both Stuttgart, Germany, and Sewell, New Jersey, USA, to develop specific process configurations that can handle high levels of meat slurries and digests. “This includes providing very special screw element combinations, which are specifically designed to properly mix and cook the high-meat ingredients within the extruder. In addition, the process experts at Coperion provide added experience in overall extrusion system design both upstream and downstream of the extruder. Recommendations include possibly splitting the meat feed streams to the extruder as well as use of high accuracy Coperion K-Tron feeders for the dry ingredients of the process. All system design recommendations are engineered with an emphasis on overall process efficiency, cost savings and product food safety.”
Coperion’s newest twin screw extruder, the ZSK Mv PLUS, is ideally suited to achieve the requirements of high-meat processing, according to the company. The combination of its deeply cut screws, resulting in a higher free volume (Do/Di of 1.8) and its ability to run at speeds up to 1800 RPM result in higher capacities of difficult high-meat products, all within the same footprint. | Coperion K-Tron
Extru-Tech has worked on two innovations that are especially pertinent to high-meat inclusions. “First, we developed operational methodology and process parameters, combined with performance-enhancing extrusion components and barrel configurations, to produce any combination of [high-meat inclusion needs] on a cost-effective single-screw architecture, without the need for a meat pre-heat unit, a pre-dryer before the main dryer or costly engineered binders,” said Henry. “Second, we made significant advances in our scientific validation of pathogen kill-steps. This is particularly relevant due to the elevated pathogen risk associated with fresh meat and higher inclusion rates. In this context, we assist customers by testing new recipes at the 1SG Extrusion Laboratory in Manhattan, Kansas, USA, particularly to evaluate kill-step effectiveness using natural occurring pathogens. We conduct trial runs and develop both process methodologies and validated kill-step procedures, enabling them to safely produce these recipes either at their own or co-packing plants.”
As the high-meat trend continues to grow, the industry is anticipating—and preparing—for further challenges. “High-meat pet foods and treats will continue expanding into intermediate moisture-soft products,” said Albin. “These finished products might contain around 40% moisture or more, and use various methods to maintain shelf life, including refrigeration.”
As public awareness of food safety continues to grow, and pet food manufacturing regulations reflect this consumer awareness, being able to achieve sterility with raw, wet animal ingredients is a nice option, according to Dave Albin, PhD, with Insta-Pro. | Insta-Pro
A wet animal product extrusion line can play several roles with these products, according to Albin. “To deal with the high variation of meat ingredients and animal products, a blend of meat ingredients and dry carriers, co-extruded and used as a higher-moisture ingredient, could help maintain final product consistency by reducing ingredient variation,” he said. “And, if more minimal processing is the goal, the high-shear extruder could be configured to cook at lower temperatures, assuming that some other method of final product stabilization (like reduced pH) will be used. In addition, these higher-moisture ingredients avoid any potential nutrient damage associated with drying at elevated temperatures for long periods of time.”
Optimizing not only the extrusion system but the entire process line to meet the complexities associated with the market’s growing demand for better nutrition, superior palatability and safer pet food will be key, according to Henry. “This requires further research and closer collaboration with a number of other organizations—conducting these efficiently is yet another challenge.”