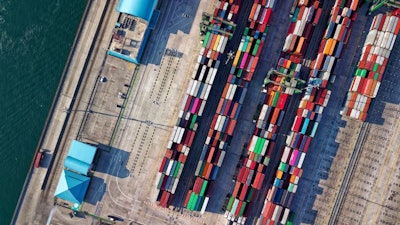
Many of us can empathize with a recent article headline in FreightWaves: “New Year, same supply chain mess.” Indeed, few industries — and certainly not the pet food industry — are immune from the supply chain disruptions that are plaguing the U.S. and many other countries.
Brief recap: ‘Perfect storm’ of supply chain issues
There are worldwide shortages and imbalances of containers and chassis. U.S. West Coast ports, in particular, are snarled with empty containers awaiting transport back to Asia and imports awaiting land transport. Arriving vessels often have to anchor for many days before they can get a berth to unload. Unusually high dwell times for loaded containers have resulted in surging theft of idled container cargo.
Once imported goods escape port bottlenecks, the situation isn’t much better. Rail capacity is overwhelmed on many routes. For years, truck carriers have faced a driver shortage, which has worsened since the pandemic began.
Meanwhile, thanks to the ongoing semiconductor chip shortage, truck manufacturers have a 14-month backlog. Consequently, carriers with aging fleets are coping with increased breakdowns.
In addition to labor shortages in ports, warehouses and distribution centers, almost every industry faces shortages of skilled workers.
Weather delays amplified the logistical delays. For example, in Canada, railroads serving the port of Vancouver were closed for three weeks before the holidays due to flooding and landslides in British Columbia.
Together, all these factors created 2021’s “perfect storm” in the supply chain — and then, the first week of 2022 greeted mid-Atlantic states with a huge snowstorm.
We’ve all seen many articles on the causes of supply chain problems. These seem to be the most commonly cited issues:
- The pandemic led to massive shifts in demand and supply chain logistics.
- Government stimulus money fueled extraordinarily high consumer demand.
- Over-reliance on “just-in-time” delivery models left buyers short of goods at critical times.
- Port and rail infrastructure is inadequate to handle soaring freight traffic and container storage.
- Businesses saw growth hampered by a variety of staffing issues, such as employee illnesses, COVID-19 restrictions, experienced people leaving the workforce and labor shortages across many industries affecting manufacturers and the entire supply chain.
Impacts of supply chain snags on the pet food industry
Our industry mirrors the supply chain problems of the macro economy. As Dana Brooks, president of Pet Food Institute, noted recently, “Manufacturers are experiencing challenges in every node of the supply chain, from the ingredient sourcing to transportation and employee shortages.”
Early in the pandemic, when many hospitality firms and other businesses linked to human food production were shut down for public safety, manufacturers lost a key source of pet food ingredients.
Simultaneously, people working from home turned to pets for companionship. According to the American Pet Products Association, 12.6 million households adopted a new pet between March and December 2020.
Today, pet food manufacturers continue to face ingredient shortages, long lead times and huge price increases in processing equipment, ingredients and transportation.
Labor shortages hit as business was booming. The pet food industry needs a wide variety of skills, almost all of which are in short supply. This forces us to explore new ways to attract and retain talent.
The pet food industry’s situation reminds me of the arcade game whack-a-mole. Manufacturers must plan sourcing, production and sales while dealing with shortages, delays, rising costs and rising demand. Retailers have to explain to pet parents why a pet’s favorite food soared in price — or is out of stock.
The news isn’t totally bleak. A lot is being done to ease supply chain bottlenecks. A few examples:
- Ports and ocean carriers are working to clear empty containers.
- “Inland ports,” connected by rail to major East and West Coast ports, are being established to alleviate congested port areas.
- Target and other large retailers are chartering vessels to assure their stores are stocked.
- Truckers are lobbying to ease restrictions on drivers.
- Employers are trying everything from sign-on bonuses to engagement strategies to make jobs more attractive.
How can pet food manufacturers and retailers cope?
Experts predict current conditions will last well into 2022. I believe pet adoption rates will remain at high levels, driving the need for more pet food capacity in the industry.
Now more than ever in the pet food industry, relationships with suppliers have become super important. It’s key to have partners that are working with you to get essential supplies.
Consumers know that shortages are pervasive, so candor is key throughout the supply chain. Manufacturers, distributors and retailers have to be open and transparent with their customers.
Retailers can consider diversifying brands and lining up alternative suppliers. Another option is private labeling. Private labels used to be driven by cost-conscious consumers, but now they are increasingly formulated for buyers of premium pet food.
Manufacturers can seek domestic alternatives to foreign suppliers. Lead times for imported packaging often exceed 16 weeks, and imported ingredients also have long lead times.
In response, Alphia is now sourcing more supplies domestically. We’re finding that U.S. suppliers of packaging, for example, have much shorter lead times. On the ingredient side, domestic sourcing is tougher because some ingredients are primarily produced in specific countries, like lamb from New Zealand.
If key ingredients have tight supplies, manufacturers can introduce new formulations with alternative ingredients. Another option is to outsource portions of sourcing and production to a partner.
Like many other companies, Alphia is trying to avoid Los Angeles (California, USA) and other backed-up West Coast ports when possible. We have been diverting some shipments to Houston (Texas, USA) and East Coast ports.
Needed: Good forecasting and planning
In the roller-coaster world of COVID-19, no one knows what lies ahead for the economy. We don’t know when our businesses will return to normal and we don’t even know what “normal” will be in the future.
In these turbulent times, the importance of good forecasting and planning can’t be understated. We can assume the current situation will continue until data tells us otherwise. We can plan what actions we will take if more disruptions occur. And most importantly, we can endeavor to keep building strong relationships with our key customers and partners.