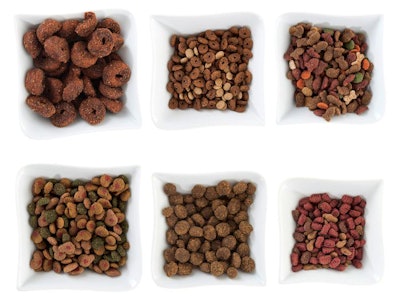
At the end of 2018, “true meat slurries/raw meat additions to extruders” was one of the top trends extrusion experts listed as presenting challenges to their evolving business. As 2019 comes to a close, fresh meat inclusion continues to be a primary focus, now being listed as the single top trend expected to affect extrusion technology in 2020.
Consumer desires and technical challenges
Unsurprisingly, pet owners wanting the “best” for their animals are largely responsible for higher meat inclusion rates in pet food. In fact, high-protein formulas (which can include both animal and plant proteins, though animal protein is the more common selling point) are now a staple on premium and superpremium pet food shelves, in everything from “standard” diets to “ancestral” or “biologically appropriate” formulations.
According to the Association of American Feed Control Officials (AAFCO), adult dog foods should contain at least 18% crude protein (on a dry matter basis), while reproducing female dogs and puppies’ foods should contain a minimum of 22.5% crude protein. While not strictly official, most in the pet food industry have settled on a dog formula with at least 30% protein as a food that can claim to be “high protein.” For cat food the protein levels are higher, at 26% for adult maintenance diets and 30% for growth and reproduction-focused formulas, according to AAFCO.
“This trend allows label claims ‘made with fresh meat’ or ‘from meat,’ which are valued by consumers looking for high-quality protein sources in their pets’ food,” said Gilles Maller, vice president, sales and international for Clextral. “However, it requires understanding of the meat ingredients, special handling and storage, a focus on hygiene and modifications in extruder parameters as well as upstream equipment.”
Clextral operates test plants in Tampa, Florida, USA, and Firminy, France, and works with partners in research centers and universities around the world. | Courtesy Clextral
Twin screw extruders get a lot of play when high-meat formulas enter the picture, presenting both benefits and challenges of their own.
“As the request for high-meat products increases, there is also an increased request in providing higher throughput rates,” said Sharon Nowak, business development manager for Coperion K-Tron USA. “Customers are currently asking to provide these higher throughput rates with the twin screw extruder, while at the same time keeping overall machine sizes and foot prints. Processing high meat levels requires a reduction in throughput rate relative to classic dry food. The challenge for the extruder manufacturer is to develop methods that allow the higher throughput rates needed to process the high-meat slurries within the extruder while still maintaining overall physical size.”
Coperion’s newest twin screw extruder, the ZSK Mv PLUS, has a combination of deeply cut screws that result in a higher free volume and an ability to run at speeds up to 1800 RPM, which result in higher capacities of difficult high-meat products, all within the same footprint. | Courtesy Coperion K-Tron USA
Expert solutions for a changing business
Efficiency in all areas is the name of the game, with extrusion experts seeking various ways to ensure high-meat mixes don’t slow things down.
“A primary focus within Extru-Tech that has been at the forefront of almost all of our project design criteria is the directive to increase operational efficiency,” said Will Henry, R&D for Extru-Tech Inc. “As the pet food product shelves become more densely packaged it becomes more difficult to provide solutions that are simply 'flexible' ... the solution must prove to also be cost-effective and provide operational efficiency.”
One area of opportunity for improvement the company is focusing on is change-over/out downtime, but it’s preventive maintenance that Extru-Tech sees as having the most promise.
“With the ability to monitor and cross-check all wear components with current and upcoming production runs, the potential of drastically reducing un-scheduled down time due to equipment failure will undoubtedly improve the bottom line,” said Henry.
Clextral has been developing advancements in hygiene, a significant topic when dealing with high-meat products.
“Our focus on hygienic design is ongoing, which is critical when working with ingredients that can carry pathogens, whether wet or dry,” said Maller. The company maintains technology that includes advanced thermal control, providing precision in temperature control to the benefit of the essential pathogen kill step during processing.
Several of Coperion’s technologies focus on efficiently mixing a variety of disparate ingredients, such as fresh vegetables and other products which can’t be fed by traditional screw feeder devices, as well as high-meat formulations needing special equipment. Even material flow, faster product changeover, less downtime and of course quality of the final product are all keys to success, according to the company.