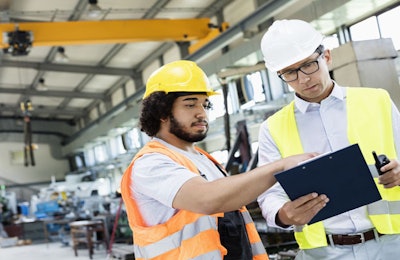
The Food and Drug Administration (FDA) has begun inspections of pet food manufacturing facilities under the Food Safety Modernization Act (FSMA), specifically the current good manufacturing practice (CGMP) requirement of the preventive controls rule for animal food. An FDA officer and members of the pet food industry shared updates and lessons learned from inspections held to date during separate sessions of the eighth annual Feed and Pet Food Joint Conference, held October 23-25 in Louisville, Kentucky, USA.
The preventive controls rule for animal feed (including pet food) is one of seven main regulations issued by FDA under FSMA. The two key requirements of the rule include establishing, documenting and adhering to CGMPs (including elements such as personnel, plant and grounds, sanitation, equipment and utensils, operations and product holding and distribution) and conducting a hazard analysis and establishing preventive controls, documented in a food safety plan.
FDA established a staggered compliance schedule, based on the size of the pet food company and with CGMP compliance coming first. For larger organizations (with more than 500 employees and more than US$2.5 million in annual sales), that compliance date happened in September 2016, followed by compliance to the preventive controls element in September 2017. However, FDA announced in August 2017 that it was delaying the start of routine inspections for preventive controls until fall 2018.
FDA report on CGMP pet food safety inspections
Jenny Murphy, consumer safety officer with FDA’s Center for Veterinary Medicine, discussed the agency’s inspection activities in her presentation at the feed and pet food joint conference, which was organized by the Pet Food Institute and National Grain and Feed Association. First, she emphasized that the delay of inspections for preventive controls and food safety plans applies only to routine inspections; if an issue such as a recall arises, an inspection would likely ensue.
Also, the delay doesn’t mean that large pet food companies should postpone compliance with that requirement. “You should have developed and be following your food safety plan,” she said. The extension of the date simply gives companies more time to “work out the kinks” and further develop their plans.
FDA did conduct 230 CGMP inspections this past fiscal year, Murphy reported, and she shared observations from inspectors:
- Inspections are more conversational (and will continue to be so). They tend to take more time (six to eight hours) than checklist-type inspections because it's a new rule, and people on both sides are still learning.
- Inspectors asked questions (and will continue to do so) about preventive controls readiness.
- The overall industry report card is very positive, even exceeding FDA’s expectations a bit.
- Most common findings in terms of problems were with pest infestations, especially in warehouses.
Murphy said that pet food companies whose facilities were inspected shared concerns with FDA, including why inspectors asked to see consumer complaint files (see sidebar below) and pest management records. She speculated that the “disconnect” comes about because neither of these is required by FSMA, but it is standard operating procedure for inspectors. “So, you're not required to share these files or records, but if you have a good, positive story to tell, do share it!” she said. An inspection is a snapshot in time, she added; the inspector has to make a determination based on what she or he sees at that time. Files and records can help give a more complete or detailed picture.
Finally, for CGMP inspections in fiscal year 2018 – which, in addition to large businesses, will include small businesses (those with fewer than 500 employees but more than US$2.5 million in annual sales) – Murphy said to expect:
- More inspections, which will be conducted by both FDA and state inspectors. (The latter must go through FDA regulatory training.)
- However, they will not inspect all large and small businesses.
- CGMP inspections may be combined with inspections for BSE and, at some point, sanitary transportation; that is still being determined.
- FDA will continue to educate before and during the inspections.
Pet food industry’s take, tips for successful CGMP inspections
During a separate, interactive session at the conference, representatives of pet food companies presented their experiences and lessons learned from CGMP inspections to date. Michele Sayles, executive director of food safety and quality for Diamond Pet Foods, and Richard Driggs, director of operational quality for Nestlé Purina PetCare, role-played an ongoing inspection, with Sayles as FDA inspector and Driggs as the quality and safety manager of a pet food or feed facility.
The enacted inspection included several scenarios: FSMA readiness, inspection preliminary questions and the actual CGMP inspection, in this case of a feed mill and covering plant and grounds, receiving, hazard disclosures and written assurances and outbound product shipments. Matt Frederking, vice president of regulatory affairs and quality for Mid America Pet Food, narrated each scene, while Cassandra Jones, PhD, associate professor at Kansas State University and a participant in FDA inspector training, led audience discussion and questions via online polling, then shared helpful information and tips.
During the discussions, Driggs revealed that Purina facilities have already undergone 16 CGMP inspections, confirming Murphy’s earlier report that FDA was actively carrying out the inspections. His experiences, along with those of the other presenters, also corroborated Murphy’s comments about industry concerns over questions asked by FDA inspectors but not necessarily covered under FSMA. Like Murphy, they advised that, while documentation is not required to answer those questions or for many FSMA requirements, it’s sometimes helpful to create it and share it with an inspector.
“Supporting documentation may be valuable to help defend and justify your determinations, particularly if used to evaluate probability in hazard analysis,” Jones said.
What to share – and not to share – with the inspector
Examples of information and files not required under FSMA but often requested during an inspection include a process flow diagram to guide the inspector through your plant. The investigator likely will want to evaluate process flow, Jones added, and sharing it before the actual inspection, while talking in a conference room, for example, might prevent the inspector from looking at every single step or machine in your plant. “It may get the inspector in and out of there more quickly,” she said.
Other examples presented included pest management plans and questions from the inspector about business information like annual sales, number of employees and top customers and suppliers. Jones shared these take-aways:
- Though not specifically required by CGMPs, FDA generally expects a written pest control plan that includes monitoring records.
- It may be appropriate to ask an investigator why business information is being requested. Also, be aware that FDA may ask questions in a roundabout way or in several ways.
- Develop a policy on how to handle FDA requests for customer and supplier information before you are inspected. Remember that FDA does have authority to access records associated with movement of food in interstate commerce.
- Unless your company is considered a large business under FSMA (more than 500 employees and more than US$2.5 million in annual sales), you do need to provide FDA with information about your business’s size to substantiate your compliance dates and your eligibility for certain exemptions under FSMA.
Other scenarios and questions that arose included the inspector asking about your company’s FSMA readiness – again, the presenters advised developing a plan ahead of time on how to respond – as well as the preventive controls qualified individual (PCQI, the person identified and trained to administer the food safety plan) and their training. The PCQI is not required to complete FDA’s training but still needs to be a qualified individual, Jones explained. Think through how to complete appropriate qualified individual training and who needs to receive documented training.
A free training video, “Animal Food Hygiene and Animal Food Safety,” is available on YouTube and has been reviewed and approved by FDA, Jones added. (See https://goo.gl/oFmPde.)
Play your cards strategically
Jones used the analogy of playing card games in discussing how to respond to FDA questions and requests for non-required documents. “You have a certain number of trump cards,” she said – in this case, refusals of such requests. “Use those cards strategically throughout the inspection.”
The bottom line is that CMGP requirements are flexible due to the breadth of facility types covered under FSMA. Industry requested this flexibility and FDA gave it, Jones said, but the flip side is that there are a lot of unknowns and gray areas. It is the responsibility of each facility’s management to make appropriate decisions for CGMP compliance and decide on those gray areas themselves, well before the FDA inspector shows up at the door.
How to handle FDA requests for consumer complaint files
During a routine FSMA inspection (not investigating a food safety incident), FDA does not have authority to require access to consumer complaint files, emphasized Cassandra Jones, PhD, associate professor at Kansas State University and a participant in FDA inspector training. But, if such files are listed in your food safety plan as verification for something, then it’s fair game – so don't have that in your food safety plan, she advised. It’s wise to develop a policy before an inspection for whether and when to share complaint files.
A member of the audience during an interactive session at the eighth annual Feed and Pet Food Joint Conference shared his experience with an FDA inspector requesting consumer complaint files. In his company’s case, they negotiated to sharing complaints from a specific month. FDA is hearing from consumers, he explained, so it helps the inspection go more smoothly if you address it somehow. But, be sure to provide context, he advised, such as a transcript of the consumer’s call to the company, the size of batch or distribution of the product in question and that there were no other complaints for that batch. Then you can also demonstrate that you have a process for handling complaints.