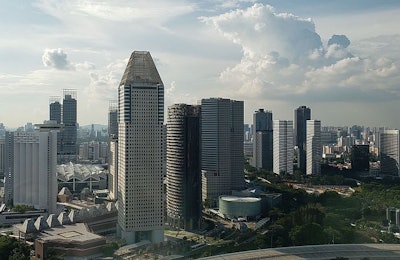
As dog, cat and other pet owner demands change, so too do the demands on pet food extruder operators. The situation facing pet food extrusion divides into seven distinct challenges, Galen Rokey, process technology director for extruder manufacturer Wenger, said during the company’s Pet Food Process Technology Seminar in Singapore on October 1.
1. Expanded ingredient inventories
Numerous novel pet food ingredients have appeared on the market within the last decade or so, Rokey said. Items like quinoa and amaranth moved from the human health food aisle into dog, cat and other pet food formulations. One challenge arises from all those new ingredients’ physical properties and interactions with each other. Extruder operators need to learn how these novel pet food ingredients influence their procedures.
2. Expanded levels of meat and other slurries
The high protein trend also moved into pet food from human dining tastes. High meat formulations in preconditioners and extruder barrels require special considerations compared to traditional kibble. Meat-heavy recipes also make drying more complex, said Robert Sunderland, Wenger dryer technology director, during his presentation.
3. Raw material availability and variation
With so many novel ingredients and unconventional formulations, securing a steady supply of raw materials can be difficult. Certain ingredients may suddenly become unavailable. When that happens, a formulation won’t behave the same in an extruder. Finding a qualitatively consistent supply of specific ingredients is yet more challenging, and those variations in raw materials cause variations in extruder conditions and the finished product.As with high meat, when raw materials vary they also dry differently, Sunderland said.
4. Product stability and freshness
While some obstacles may be new, others have posed a consistent challenge for extruded pet food. Even conventional ingredients like corn and chicken meal must be of good quality. Maintaining nutrient levels and palatability of kibble over an extended period of time has always been and will continue to be a primary concern. High heat and pressure inside extruders can dramatically alter levels of important macro- and micronutrients. Meanwhile, palatability and dietary values must be protected with shelf stability.While drying, pet food makers must be careful not to destroy lysine, vitamin C and other nutrients, Sunderland said.
5. Control of safety hazards
Safety too has always been important, but became even more so with the implementation of the Food Safety Modernization Act in the United States.
“Around the world you’re going to see more focus on meeting safety challenges,” Rokey said.
6. Rising production costs
Meeting those safety challenges can increase production costs, along with other causes of rising expenditures.
“We have to do now that we didn’t 20 years ago,” Rokey said.
7. Process complexity and required flexibility
With all the novel pet food ingredients, high meat formulations, safety measures and other challenges, the entire procedure for making pet food has become more complex. Many factories no longer simply churn out a few varieties of dog kibble, but instead maintain a diverse range of ingredients for a plethora of formulations. Pet food extrusion systems likewise need greater flexibility than before.