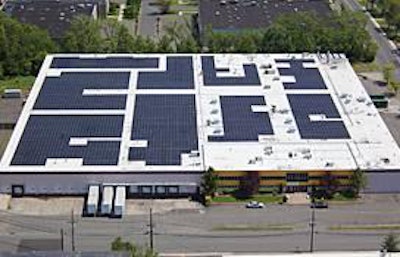
Cutting back on the amount of waste, pollution and damage we do to the earth on a daily basis as individuals can seem like a daunting task, but when you try applying those same practices to your manufacturing processes, it can seem insurmountable. Not only is it important for the future of the industry to learn to adapt, it's also important to let consumers know your company is working hard to make "green" changes to your production lines and manufacturing facilities -- not just your packaging and ingredients. Let's explore how different companies are reducing their carbon footprint with new technologies, while ensuring pet parents their products (and their practices) are ones they can continue to trust.
LPS Industries is a vertically integrated flexible packaging converter powered by renewable energy. "Packaging manufactured with solar power is an attribute that is attractive to our customers with a corporate commitment to sustainability, especially those whose goods are sold at retail," explains Charles Ardman, VP of marketing for LPS. "A supply chain partner with a complementary sustainability commitment that has a real, measurable impact on the environment can meaningfully differentiate a product on the retail shelf in the eyes of the customer."
In June 2010, LPS announced it had completed the largest Solyndra solar panel rooftop installation in the United States, a 704.34kW system. The installation will provide 25% of the power for the 165,000 square foot manufacturing facility and is part of a larger commitment to reduce energy consumption and produce packaging products in the most sustainable manner. The LPS installation consists of 3,870 Solyndra solar panels, producing over 825,000 kWh of electricity and eliminating more than 1.1 million pounds of CO2 emissions annually.
Industrial hot water heating can be a major energy and cost outlay for petfood processors and manufacturers. Reducing that energy usage is good for the company’s bottom line, the environment and the public. An easy-to-use calculator that estimates the energy used for specific process conditions, developed by Hydro-Thermal, is now available online.
The calculator uses sound thermodynamic assumptions and formulas to estimate the energy used for specific process conditions and compares the required energy of a heat exchanger with that of a direct steam injection three-way valve. Users can input their process flow rates, needed output temperature, fuel costs and other data directly into the calculator. A comparison of the energy usage is shown side by side for each heating technology.
Investments of US$1 million provide equipment and environmental control processes, from advanced treatment of waste by filters to the chimneys of steam-generating systems used in the manufacturing process.